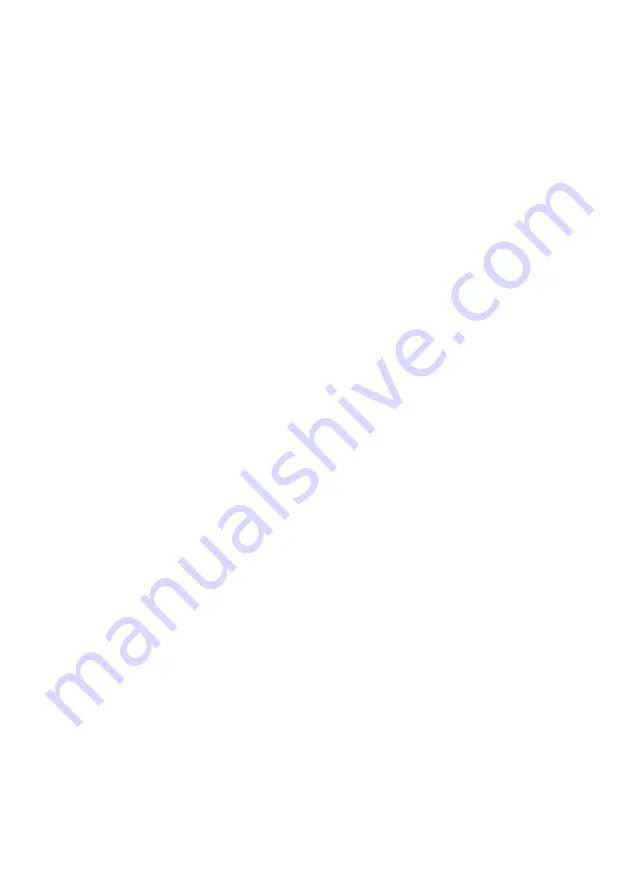
12
3.2.
Unpacking Inspection
Out of the box before check the packaging for damage, if there is damage,
please contact the carrier.
Carefully remove the packaging and check whether there are internal devices
scratches, impact, if any, please contact the carrier.
The packing list an inventory of accessories are complete, if not complete,
please contact the supplier.
After removing the desiccant check whether the needle has a needle cap, a
short press will remove the valve needle cap, whether gas emissions, if not,
contact the supplier. If so, then the needle cap to re-install the good.
3.3.
Installation
3.3.1.
Outdoor Installation
Installation DN-97332/DN-97333/DN-97334
1.
The outdoor unit placed on the base.
2.
The outdoor unit expansion bolts fixed to the base.
Piping Installation
Piping principle
1.
The use of copper pipe connection between the indoor unit and
outdoor unit, 3.9 kW/7.2 kW/12 kW which an indoor unit and an
outdoor unit are imperial quick connector nipple (when the pipe
length exceeds standard pipe length requires the use of welding
connections the brass);
2.
SmoothAir refrigerant air conditioning units as standard is R410A.
3kW/7kW/12kW refrigerant factory prefilled.
3.
All refrigerant pipe should be as short as possible and beautiful, neat,
smooth vertical and horizontal, to minimize the elbow, fixed.
4.
Comply with industry standard selection Pipe Size, Pipe size
recommended values refer to Table 3-2.
5.
Between the evaporator and the condenser recommended maximum
distance of 30m (equivalent length), If the distance exceeds this,
please contact the manufacturer for help. Equivalent length of the
sub-assembly is shown in Table 3-3.