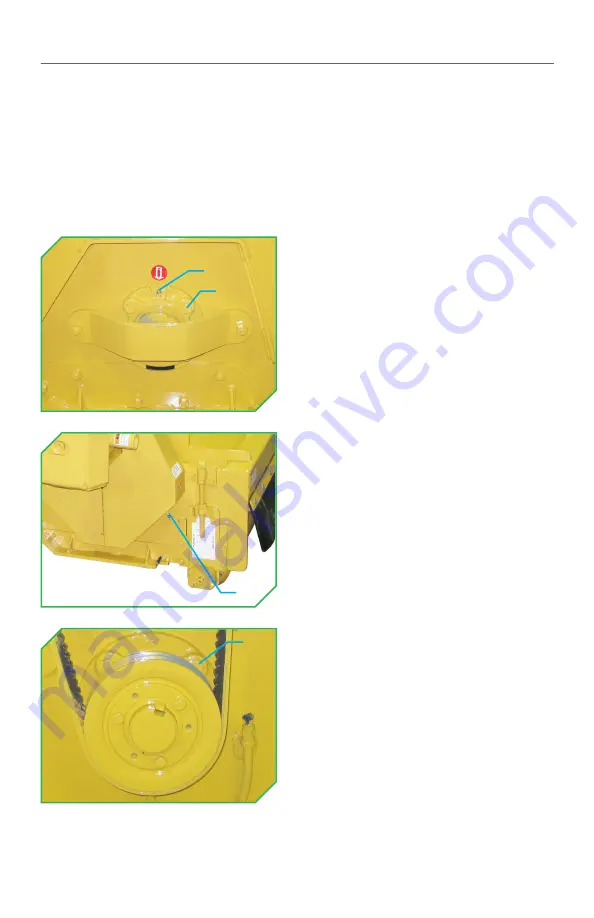
REAR SWING FLAIL
OPERATOR’S MANUAL
CONTINUED ON NEXT PAGE
BELTS AND PULLEYS
Reversing Cutting Shaft Rotation:
•
Install the front shield
(11)
for reverse rotation, or remove it for
forward rotation.
•
Install the baffle with bolts
(12)
for forward rotation, or remove it for
reverse rotation.
◦
Reference the parts pages for additional information.
CUTTING SHAFT
•
Grease the cutting shaft bearing
zerks
(1)
(1 on each side of the flail)
every 10 hours or daily with #2
lithium based grease from a hand
grease gun until grease purges from
the bearing seals.
•
Torque the cutting shaft bearing
bolts
(2)
to 90ft-lbs (122Nm) on each
side of the flail every 50 hours
or weekly.
◦
NOTE:
The access covers covering
the pulleys and belt must be
removed to gain access to the
cutting shaft bearing bolts
located underneath the bottom
pulley of the flail.
(1)
(2)
(1)
(2)
22