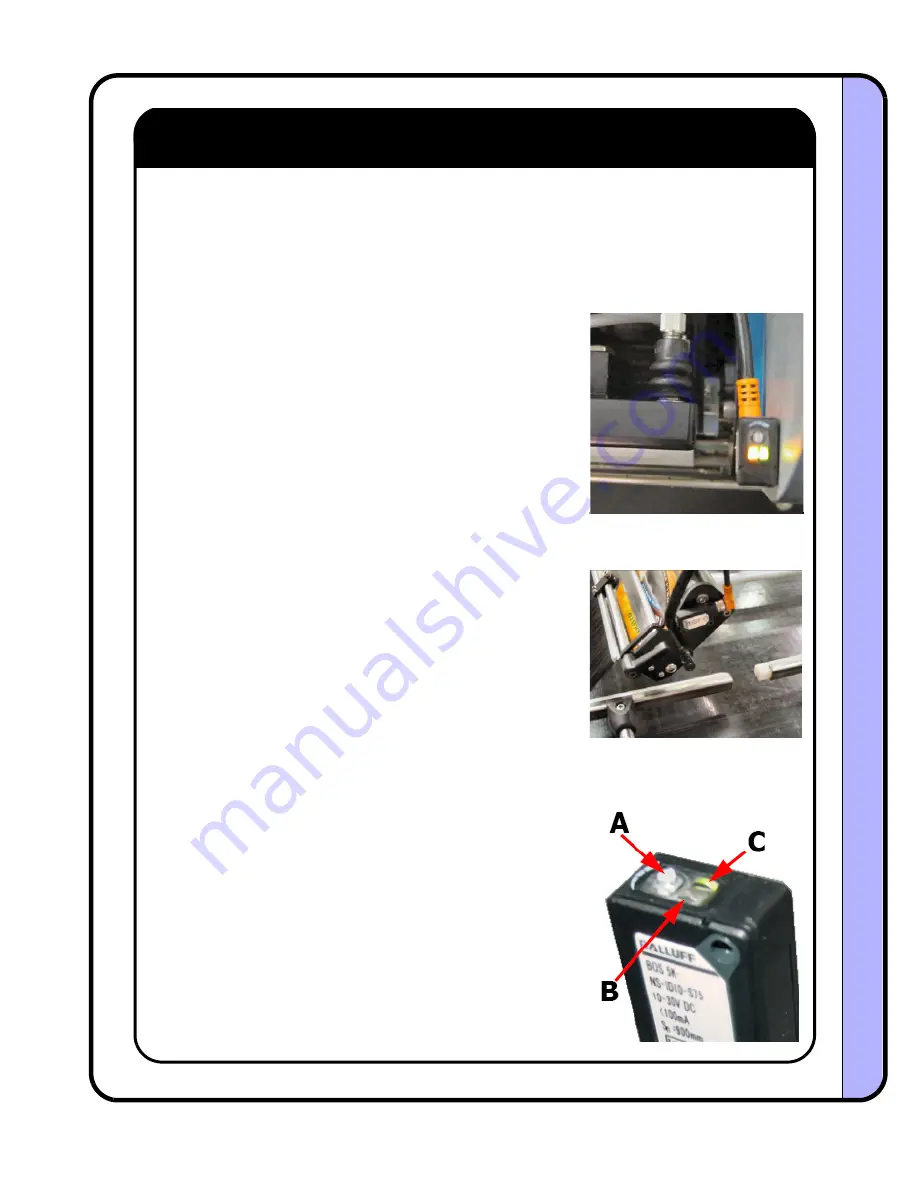
Step 4 - Mount and Adjust the Product Detector
Goal:
Determine which mounting location is ideal, either on the baseplate, on the snorkel, or on the
conveyor system.
Goal:
Adjust the sensor to detect just the product, and ignore background objects, such as forklift
trucks, personnel, or other objects that may pass in front of the sensor’s view.
•••• Sub-Step (a) ••••
Determine if a product detector mounting location on the baseplate
or snorkel (wipe-on) will work for this application. Typically, the
location on the baseplate or snorkel is ideal for mounting ease and
mobility. This location works best if the products are approaching
from the side of the sensor, in relation to the tamp pad. If this
location cannot apply the label in the desired position due to
timing, mount the sensor in an alternate location (such as the
conveyor) using the supplied mounting bracket.
•••• Sub-Step (b) ••••
Adjust the sensor’s sensitivity to detect just the product, and ignore
the background. This can be done by placing the actual product in
the path of the sensor’s view. Adjust the sensitivity setscrew (A)
until the yellow light (B) illuminates, and the green light (C) is
steady and bright. The yellow light shows that the output is active.
The green light shows the relative signal strength in the presence
of the product. When the sensor is not detecting a product, the
green light is on to show that the sensor is powered on. This can
be useful for troubleshooting and calibration. Remove the product
and verify that the yellow light is off. If not, adjust the setscrew
counter-clockwise to reduce sensitivity. Once the background is
eliminated from triggering the sensor, place the product under the
sensor again to verify output.
Baseplate mount shown
Snorkel mount shown
Diagraph - an ITW Company LA/4700 User Manual - Revision B
Setup
Page 20
Setup
Summary of Contents for LA/4700
Page 1: ...4700 010 Revision B...
Page 61: ...Diagraph an ITW Company LA 4700 User Manual Revision B Maintenance Page 60 Maintenance...
Page 62: ...Diagraph an ITW Company LA 4700 User Manual Revision B Maintenance Page 61 Maintenance...
Page 63: ...Diagraph an ITW Company LA 4700 User Manual Revision B Maintenance Page 62 Maintenance...