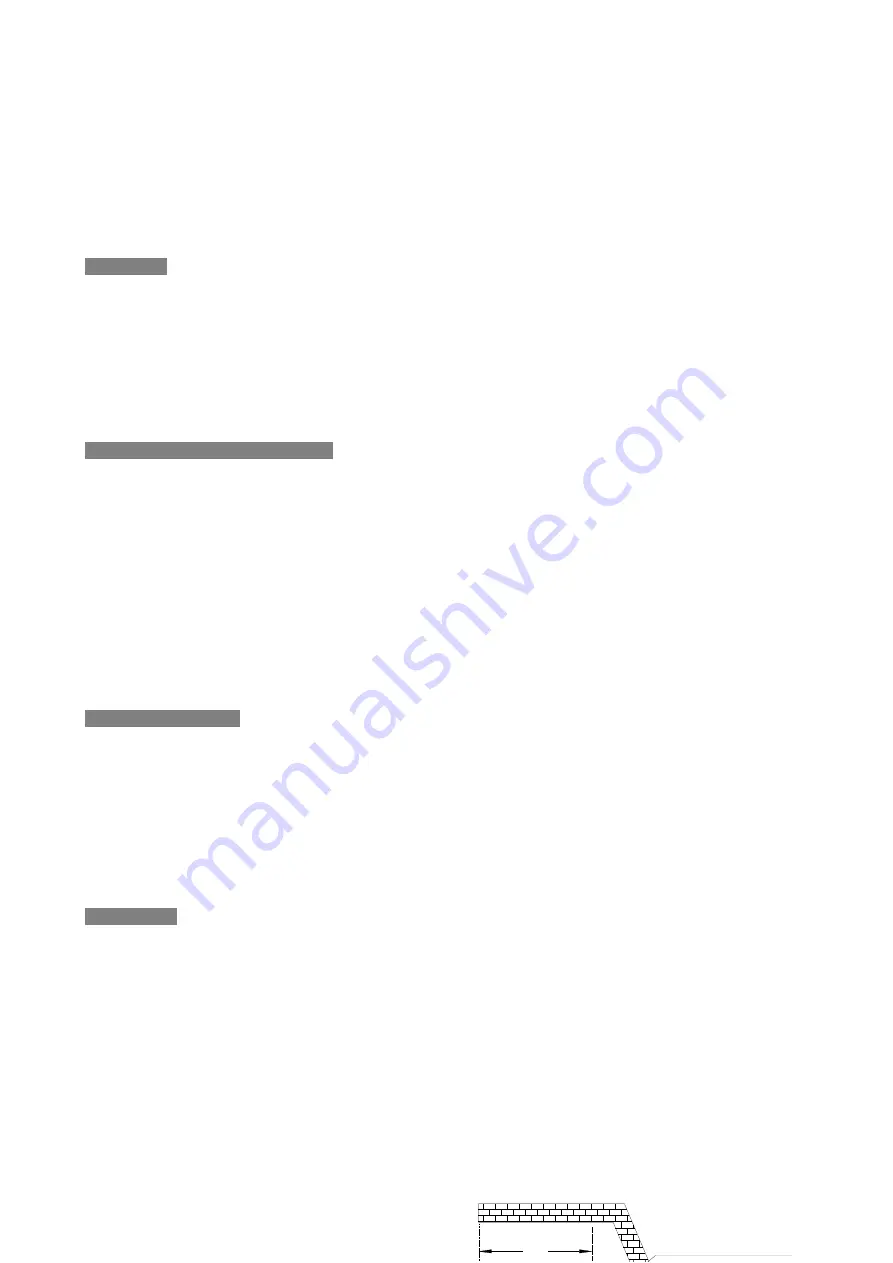
NJL/GTECH- 3/10/06 Revision No.3
11
Spacer Box
On completing and positioning of the gas supply pipe, slide the Hot Box into position, then using the four
countersunk screws provided, place the screws through the four holes outer trim of the Hot Box, and into
the corresponding screwed holes of the spacer.
Screw and seal the Hot Box to the spacer box, ensuring that the heads of the screws are not protruding
above the countersunk holes.
Fitting the Fire without Spacer Box
Slide the appliance fully into the fireplace opening. Ensure that the appliance is level, square, and central,
mark the position of four holes in the outer trim, and remove the appliance. Using a pilot drill, carefully drill into
the fireplace surround at the positions marked. Then using a 6mm drill, carefully drill out the pilot holes
and plug.
On completing and positioning of the gas supply pipe, slide the Hot Box into position. Seal and screw the
Hot Box to the fireplace surround, ensuring that the heads of the screws are not protruding above the
countersunk holes.
Fitting the Brass Trim
After the appliance has been commissioned and spillage tested, the final operation is to clip the decorative
brass trim onto the outer trim of the Hotbox.
Gently slide the two sidepieces into position. Using the inner return edge of the brass trim to clip over the
inner edge of the Hotbox trim. The top piece is then placed in position in the same manner. Finally the
plastic protective cover is carefully removed.
Gas Supply :
Connection
A means of isolating the gas supply other than the appliance control valve should be fitted in the gas supply
line to the fire.
The inlet pipe to the appliance should be 8 mm O.D. rigid or semi-rigid tubing. If the supply pipe is more
than 1.5 metres in length then the gas supply pipe diameter should be increased to a minimum of 15 mm
from that point.
110
Restrictor elbow
Concealed Connection
There is access through the outer casing of the appliance,
via, the rear and side access holes. The gas supply pipe
should be positioned within the fireplace hearth as detailed
Fig. No. 21. A hole is made through the fibre, and the tube
push through it, the fibre acting as a seal around the tube.
Fig 21