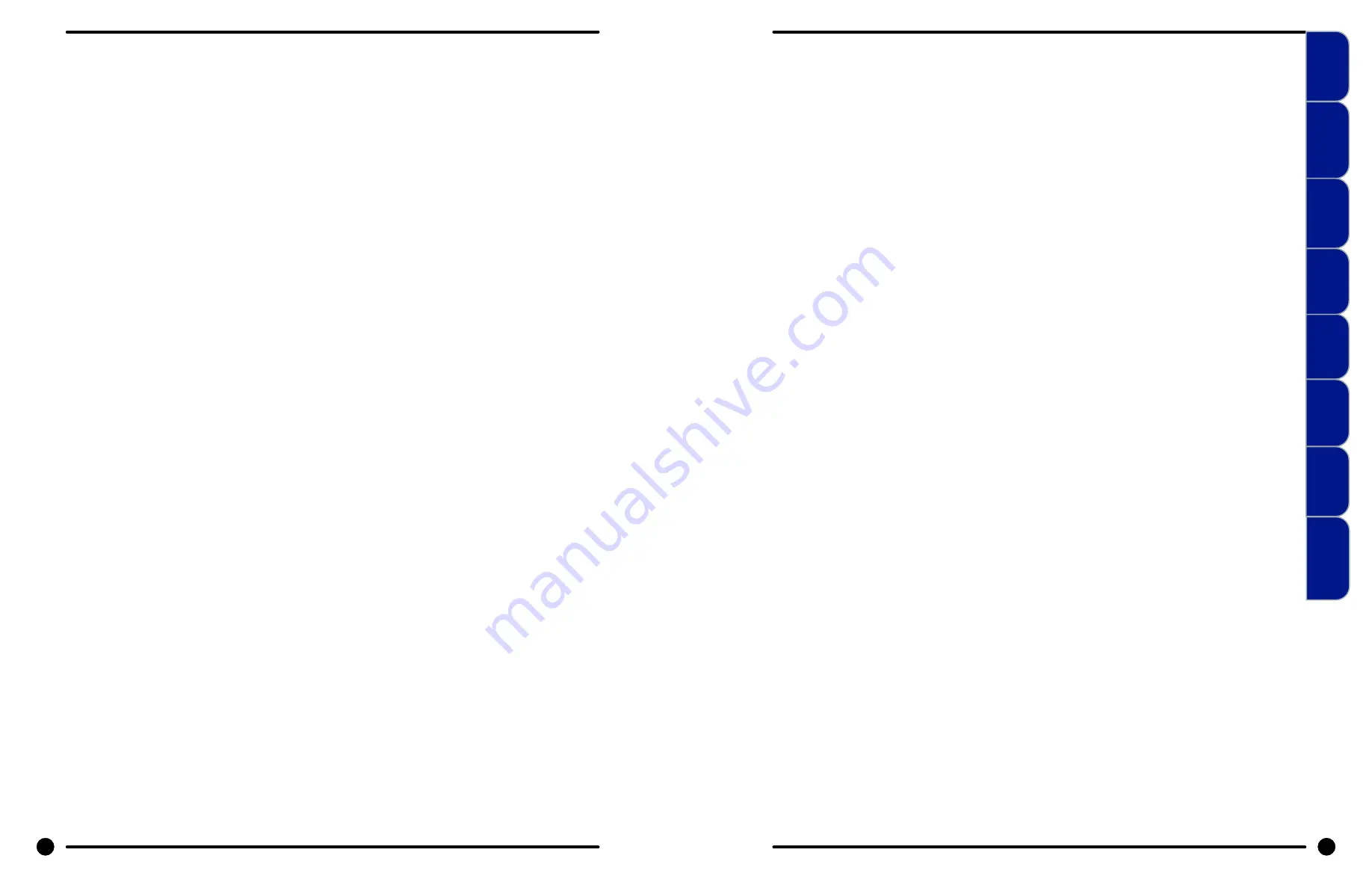
from the S3 Door Switch. The Drain Contact in the Main Timer is closed and provides 120VAC to the Drain
Valve on the brown/ yellow wire which closes the valve. The Wash Motor Contact in the Main Timer is
closed and provides 120VAC to the Reversing Timer and the Reversing Timer Motor on the blue/black wire.
This will start the Reversing Timer operating which will alternately open and close the Micro Switches that
provide the direction of tumble for the wash basket. The Wash Light Contact in the Main Timer is closed
and provides 120VAC to the Wash Light. The orange wire coming from the S3 Door Switch provides power
to the Wash Water Contact in the Main Timer. 120VAC connects from the Wash Water Contact to the Wash
Temperature Contact via an internal timer connection.
With 120VAC on the orange wire & neutral on the orange/yellow wire, the Coin Accumulator Board turns
on the Time Remaining Light & starts counting down in minutes. (If delay fill kit is installed, time count
down is stopped during fills.)
Now a cycle must be selected with the Selector Switch. We’ll use Normal Wash. The washer fills the tub
through the back of the machine with either one or both the C1 Cold and H1 Hot Water Valves. At the
beginning of the cycle, the detergent dispenser flushes the detergent into the tub. This is accomplished
with the Wash Dispenser Contact in the Main Timer. 120VAC travels through the closed Wash Dispenser
Contact and is supplied to the H2 Hot Water Valve Solenoid by the red/orange wire. As the washer fills
with water, the Wash Basket will tumble one direction for 19 seconds, pause, and then reverse direction
for 19 seconds.
120VAC travels from the Wash Water Timer Contact to the Heavy Duty Contact in the Selector Switch via
the white/black wire. 120VAC goes through the closed Heavy Duty Contact in the Selector Switch and
energizes the C1 Cold Water Valve Solenoid via the white/orange wire. 120VAC also travels to the closed
Wool/Delicate Contact in the Selector Switch. This closed contact provides power to the H1 Hot Water
Valve Solenoid via the red/yellow wire. When the water reaches the predetermined level the Pressure
Switch moves to the full position and opens the neutral side of the line to the Water Valves. This shuts the
Water Valves off.
Wash Circuit
As the washer fills the tub through the back of the machine with either one or both the C1 Cold and H1
Hot Water Valves, the Wash Basket will tumble one direction for 19 seconds, pause, and then reverse
direction for 19 seconds. This is accomplished through the use of a Reversing Timer. 120VAC is sup-
plied to the Reversing Timer Motor on the blue/black wire from the Wash Motor Timer Contact in the
Main Timer. The Reversing Timer will alternately open and close the two Wash Micro Switches and provide
120VAC to the R1A (brown/white wire) and R1B (orange/green wire) Wash Contactor Coils. These coils
open and close the Contactor Switches to operate the Drive Motor.
As discussed in Start and Fill, the Thermoactuator, Drain Valve, On Light, and Main Timer Motor are all
operating throughout the Wash Cycle.
Drain, Rinse 1 & 2, and Final Rinse Circuit
The Drain Contact in the Main Timer opens removing power to the Drain Valve. The normally-open spring-
loaded Drain Valve opens and empties the tub.
For Rinse 1 & 2, the Rinse Light Contact in the Main Timer closes and provides 120VAC to the Rinse Light.
The Rinse Water Contact in the Main Timer also closes and provides 120VAC to the Ci Cold Water Sole-
noid. The tub will fill until the predetermined level is achieved at which time the Pressure Switch Contact
will open the neutral side of the line shutting off the C1 Cold Water Solenoid.
For the Final Rinse, the Final Rinse Light Contact in the Main Timer closes and provides 120VAC to the
Final Rinse Light. Rinse water is the same as in Rinse 1 & 2 above.
Electrical Path Circuit Schematics
Timer Sequence Chart
The timer sequence charts are used in conjunction with the wiring diagrams to trace the circuitry during
the timer cycle. The timer contacts and the operation or component that each contact controls are listed
down the left side of the chart. The phases of the complete cycle are shown across the bottom of the
chart.
The timer switch increments are numbered across the top of the chart. The solid horizontal bars in the
chart denote when tne various contacts are closed during the cycle.
To use the timer sequence chart to trace the circuitry:
1.
Locate the particular part of the cycle on the sequence chart.
2.
Determine which timer contacts are closed during that particular step of the cycle by noting the
solid vertical bars in that step across the chart.
3.
Draw in the gap of the respective contacts on the wiring diagram with a soft dark pencil, to
illustrate the contacts as being closed.
4.
Similarly, determine which switch contacts are closed, by the switch chart, and illustrate them as
closed on the wiring diagram.
5.
The circuitry during the particular step of the cycle may then be easily traced on the wiring
diagram, since all contacts and switches are then properly illustrated as being open or closed.
Start Circuit
Power travels into the machine on L1 & L2 (3 phase) or L1 & N (1 phase). On 3 phase, 240VAC goes to a
Control Transformer that steps the voltage down to 120VAC for the controls. 120VAC then travels to the
1.5 amp Circuit Breaker. On 1 phase, 120VAC goes directly to the 1.5 amp Circuit Breaker. There is no
need for a step-down transformer.
From the Circuit Breaker, 120VAC travels on the white/red wire to the Coin Accumulator Transformer where
it is stepped down to 12VAC. This 12VAC powers the Coin Accumulator Board via the gray wire. With the
board now powered up, the insert coins light will be illuminated and it’s ready to count coins. 120VAC is
also supplied to the Main Timer Start and On-Off Contacts on the white/red wire. The Start Contact is
closed before the machine has been started so 120VAC travels through the Start Contact and is supplied
to the Coin Accumulator Board Start Relay. The S4 Coin Switch counts the quarters and sends a signal
to the Coin Accumulator Board. When the coin count is satisfied, the Coin Accumulator Board closes the
Start Relay and sends a short 120VAC signal on the orange/white wire to the Rapid Advance Timer Motor.
This timer motor starts advancing the Main Timer to the preselected starting position. A few seconds
after the Coin Accumulator Board sends the start signal to the Rapid Advance Timer Motor, the Coin
Accumulator Start Relay opens, the display goes blank and the On-Off Contact in the Main Timer closes
and provides 120VAC to the S1 Door Switch. The On-Off Contact also provides 120VAC to the On Light
on the red wire. With the S1 Switch closed (door is latched) the Door Lock Solenoid is now powered with
120VAC via the white/red wire. The Door Lock Solenoid pulls in, locking the door and closing the S2 and
S3 Switches. The S2 Switch is a backup to the S1 Switch so that the adjustment on S1 isn’t as critical. The
S3 Switch provides 120VAC to Timer Contact RA-3 to power the Rapid Advance Motor again and the Main
Timer is allowed to advance on to the preselected start
position. The blue wire furnishes the neutral for the controls.
Fill Circuit-Warm
120VAC is supplied to the controls through the S1, S2, and S3 Door Switches. The On Light and the Door
Lock Solenoid (discussed in Start Circuit) will remain on throughout the cycle as well as the Main Timer
Motor. The Lock Thermoactuator Contact in the Main Timer is closed and provides the neutral side to
operate the Lock Thermoactuator. This contact cycles open and closed keeping the Lock Thermoactua-
tor activated until 1 1/2 minutes before the end of the cycle. At this point the contact opens and removes
power to the Lock Thermoactuator. 120VAC is provided to the Lock Thermoactuator on the orange wire
32
33
Part # 8533-035-002 4/22
Part # 8533-035-002 4/22
Machine
Mounting
Installation
& Operation
Trouble-
shooting
Machine
Service
Electrical
Wiring
Parts
Data
Coin
Handling
Maintenance