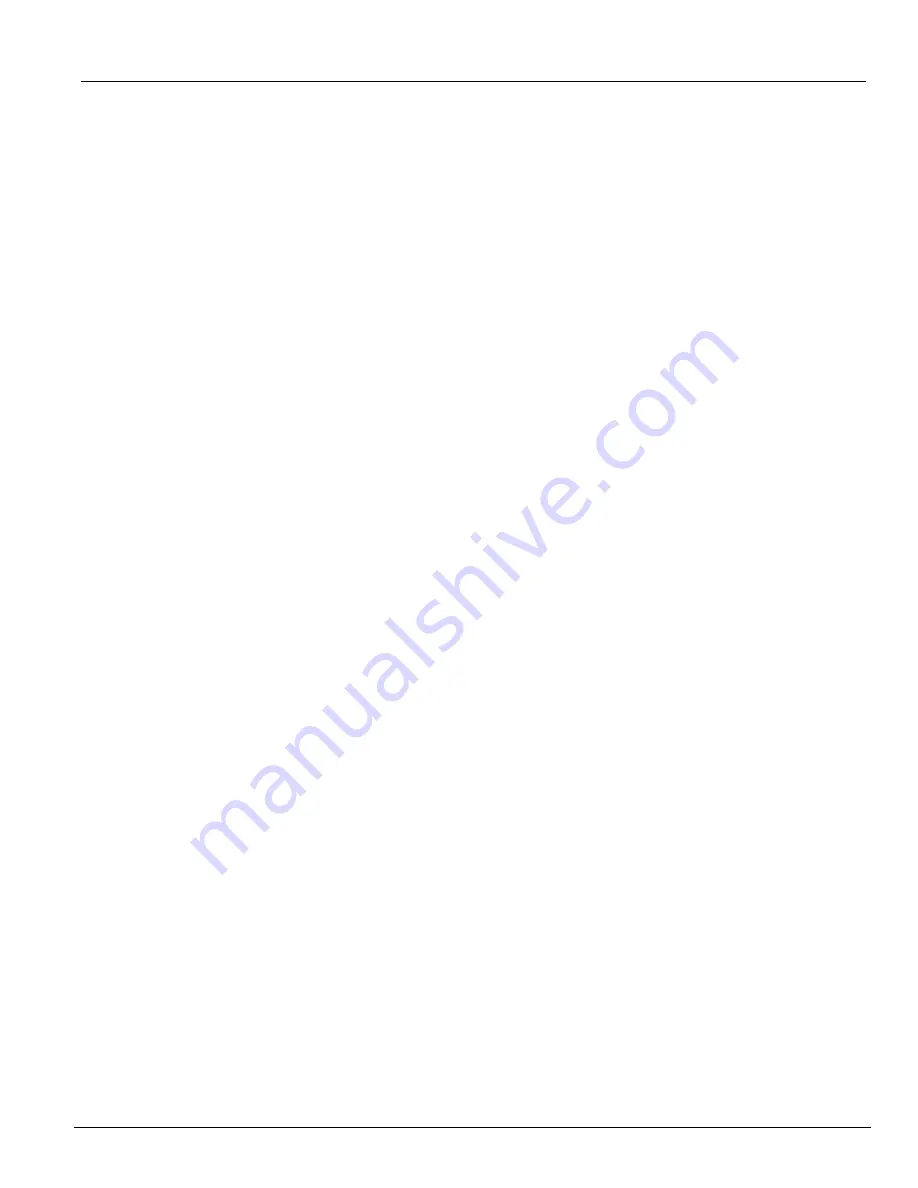
Diagnostic Repair Manual
iv
Table of Contents
Test 22 – Check Carburetion .................................32
Test 23 – Choke Test .............................................32
Test 24 – Check Valve Adjustment ........................32
Test 25 – Check Engine / Cylinder Leak Down
Test / Compression Test ........................33
Test 26 – Check Ignition Coil .................................34
Test 27 – Check Flywheel ......................................35
Test 28 – Remove Shutdown Wire ........................35
Test 30 – Check / Adjust Governor (Mechanical) ..35
Test 31 – Check Oil Pressure Switch
(if equipped) ...........................................36
Test 32 – Check Oil Level Switch (if equipped) .....36
Test 33 – Test Recoil Function ..............................37
Test 34 – Test Engine Function .............................37
Test 35 – Test Battery Charger ..............................37
Test 36 – Test Idle control .....................................37
Section 4 Major Disassembly.................................... 39
Section 5 Electrical Data ........................................... 43