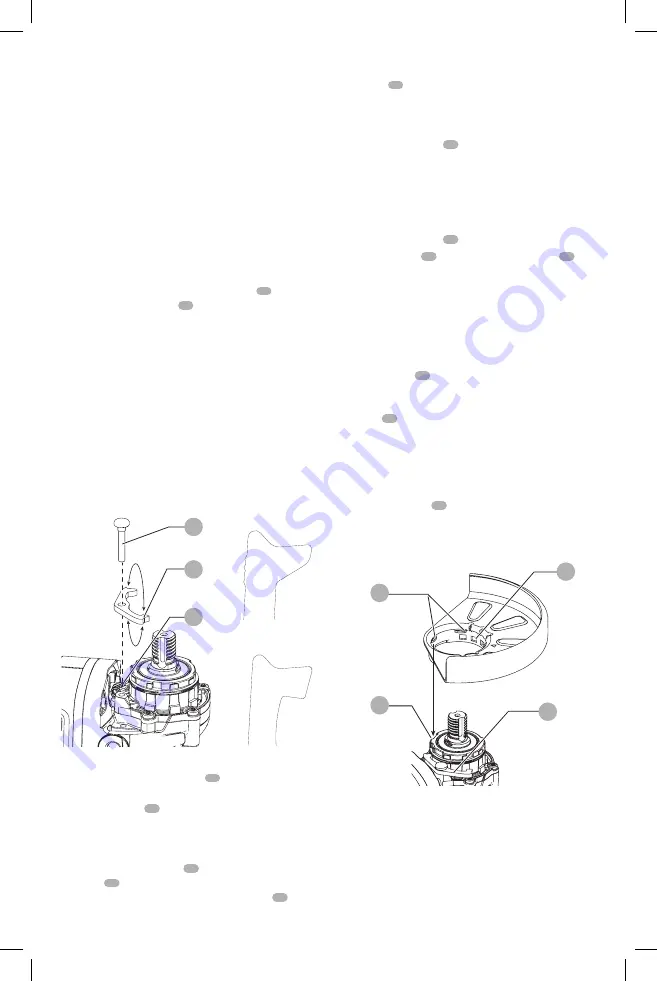
English
11
for the manufacturer's label to see if they can be used for
surface grinding or only edge grinding/cutting. A Type 1/41
guard must be used for any wheel where surface grinding
is forbidden. Cutting can also be performed by using a
Type 1/41 wheel and a Type 1/41 guard.
nOTE:
See the
Accessories Chart
to select the proper guard
/ accessory combination.
Adjusting and Mounting Guard (Fig. F, G)
CAUTION:
Turn unit off and unplug the tool before
making any adjustments or removing or installing
attachments or accessories.
CAUTION:
BEFORE operating the tool, identify which
guard adjustment option your tool is set to.
Adjustment Options
For guard adjustment, the guard release lever
10
engages
one of the alignment holes
17
on the guard collar using a
ratcheting feature. Your grinder offers two options for this
adjustment.
•
One-touch
TM
:
In this position the engaging face
is slanted and will ride over to the next alignment
hole when guard is rotated in a clockwise direction
(spindle facing user) but self-locks in the counter-
clockwise direction.
•
Two-touch
TM
:
In this position the engaging face is
straight and squared off. It will NOT ride over to the next
alignment hole unless guard release lever is pressed and
held while simultaneously rotating the guard in either
a clockwise or counter-clockwise direction (spindle
facing user).
One Touch
Two Touch
Fig. F
14
10
13
setting guard Adjustment Options
To adjust the guard release lever
10
for desired
adjustment option:
1. Remove screw
14
using a T20 bit.
2. Remove the guard release lever taking note of the
spring position. Choose the end of the lever for the
desired adjustment option. One-touch will use the
slanted end of the lever
10
to engage the alignment
holes
17
on the guard collar. Two-touch will use the
squared end to engage the alignmnet holes
17
on the
guard collar.
3. Replace the lever, positioning the chosen end under the
spring
13
. Ensure the lever is in proper contact with
the spring.
4. Replace screw and torque to 2.0-3.0N-m. Ensure proper
installation with spring return function by depressing
guard release lever
10
.
Mounting guard (Fig. g)
CAUTION:
Prior to mounting guard, ensure the screw,
lever, and spring are fitted correctly before mounting
the guard.
1. With the spindle facing the operator, press and hold the
guard release lever
10
.
2. Align the lugs
15
on the guard with the slots
16
on
the gear case.
3. Push the guard down until the guard lugs engage and
rotate them in the groove on the gear case hub. Release
the guard release lever.
4. To position the guard:
One-touch
TM
:
Rotate the guard clockwise into the
desired working position. Press and hold the guard
release lever
10
release lever to rotate the guard in the
anti-clockwise direction.
Two-touch
TM
:
Press and hold the guard release
lever
10
. Rotate the guard clockwise or anti-clockwise
into the desired working position.
nOTE:
The guard body should be positioned between
the spindle and the operator to provide maximum
operator protection.
The guard release lever should snap into one of the
alignment holes
17
on the guard collar. This ensures
that the guard is secure.
5. To remove the guard, follow steps 1–3 of these
instructions in reverse.
Fig. G
17
16
15
10
Flanges and Wheels
WARNING: To reduce the risk of serious personal
injury, turn unit off and remove the battery pack
before making any adjustments or removing/
installing attachments or accessories.
An
accidental start-up can cause injury.