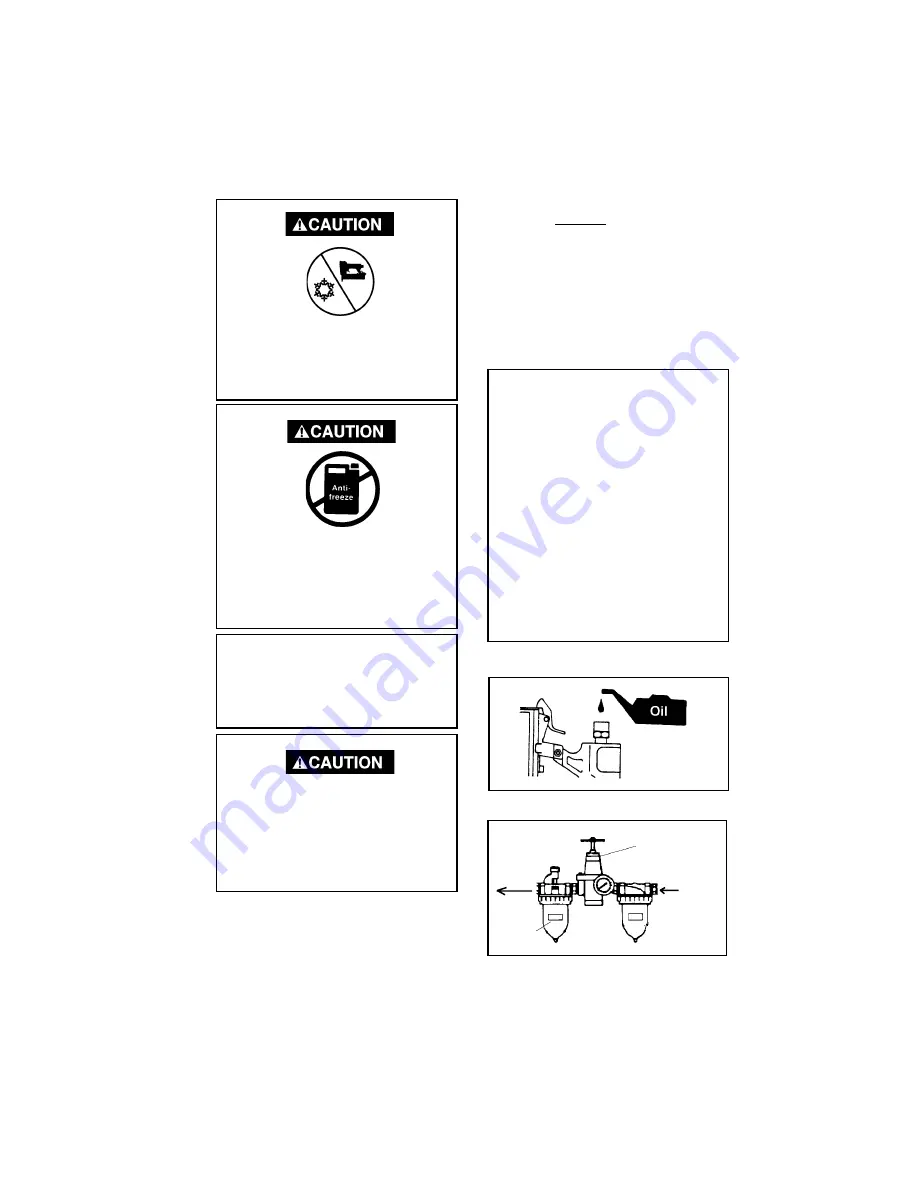
PAGE
7
Do not store the tool in cold weather. Frost
or ice can form on the operating valves or
mechanisms and the tool may not operate
correctly.
In cold weather operation (near or below
freezing), DO NOT USE a permanent
antifreeze such as ethylene glycol for a
cold weather lubricant. This type of
anitfreeze will damage o-rings and seals
of the tool.
NOTE
Proper lubrication is the owner's re-
sponsibility.
Failure to lubricate the tool
properly will dramatically shorten the life
of the tool and void your warranty.
1.
Disconnect the air supply from the tool
before manually lubricating.
Your tool requires lubrication before
you use it for the first time and before
and after each additional use.
If an
Oiler
is used, manual lubrication through the air
inlet is not required on a daily basis.
Lubrication prevents wear and prevents
rust from forming.
LUBRICATION AND MAINTENANCE
2.
Turn the tool so the air inlet is facing up
and put
one drop
of DeVilbiss AC230 Air
Tool Oil, high speed spindle oil, such as
Unocal RX22, or 3-in-1 oil into the air
inlet. DO NOT USE detergent oil or addi-
tives. Operate the tool briefly after add-
ing oil.
(See Figure 1)
DO NOT OVER LUBRICATE AIR TOOL.
3.
Wipe off excessive oil at the exhaust.
NOTE
Many air tool users find it convenient to use
an
Oiler
to help provide oil circulation
through tool. An
Oiler
also increases the
efficiency and useful life of the tool. An oiler
is recommended for tools that receive heavy
or constant use. Check oil level in the oiler
daily.
(See Figure 2)
Many air tool users find it convenient to use
a
Filter
to remove liquid and solid impuri-
ties which can rust or "gum up" internal
parts of the tool. A
Filter
also increases the
efficiency and useful life of the tool. Drain
water from the filter periodically.
(See
Figure 3)
Regulator
Oiler
Figure 1
Air Flow
Figure 2