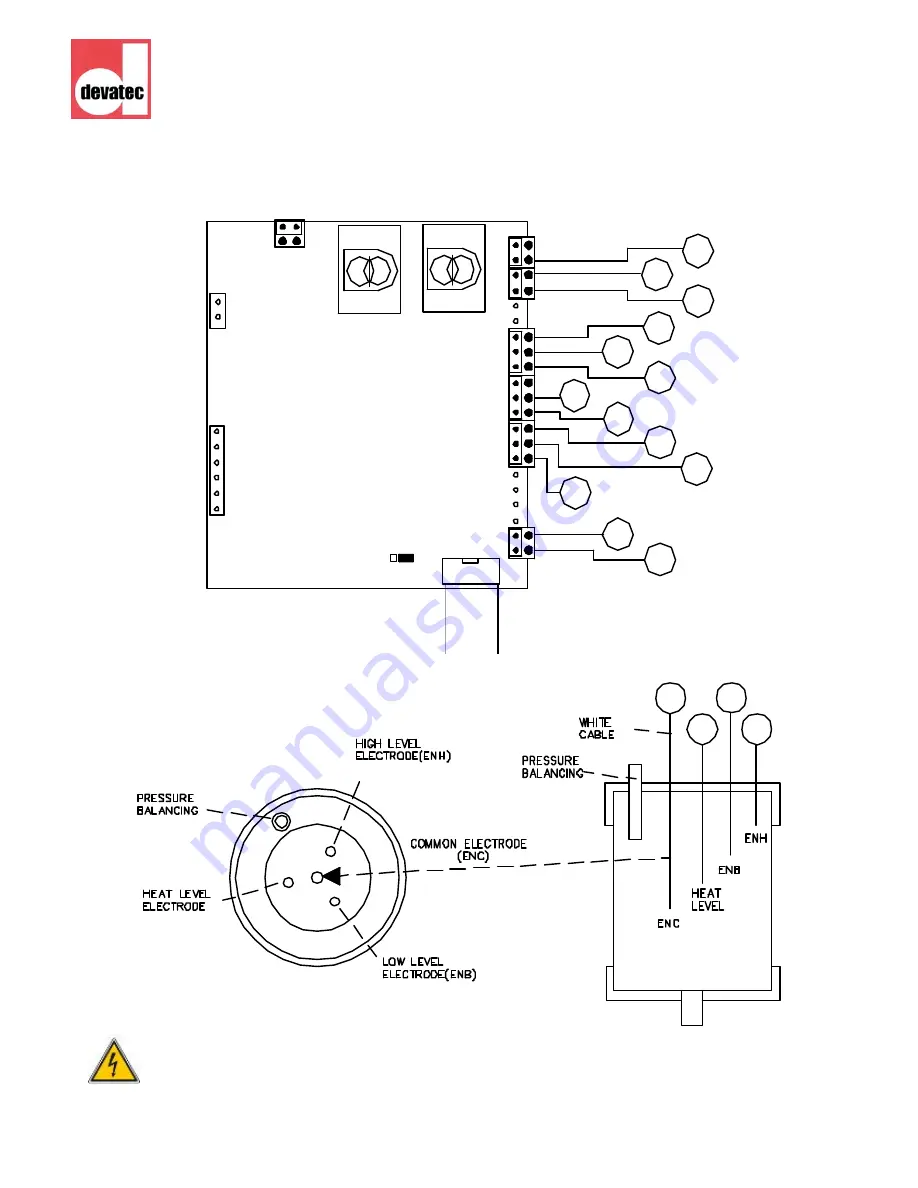
36
Pictures for illustra tive purpos es
WATER LEVEL MANAGEMENT BOARD
50
45
51
52
WATER LEVEL
SENSOR
X1
Devatec
Ref: 500851/02
78
77
76
75
73
74
CO1
X51
68
70
X3
X2
69
67
22
56
62
64
63
64
63
25
61
59
60
58
57
23
24
50
21
55
53
54
52
50
51
51
52
47
44
45
46
42
43
45
E
LECTRO
V
AP
RTH-LC
Wiring diagrams
ALL WORKS CONCERNED WITH THE ELECTRICAL INSTALLATION MUST BE CARRIED OUT BY SKILLED AND QUALIFIED PERSONNEL.