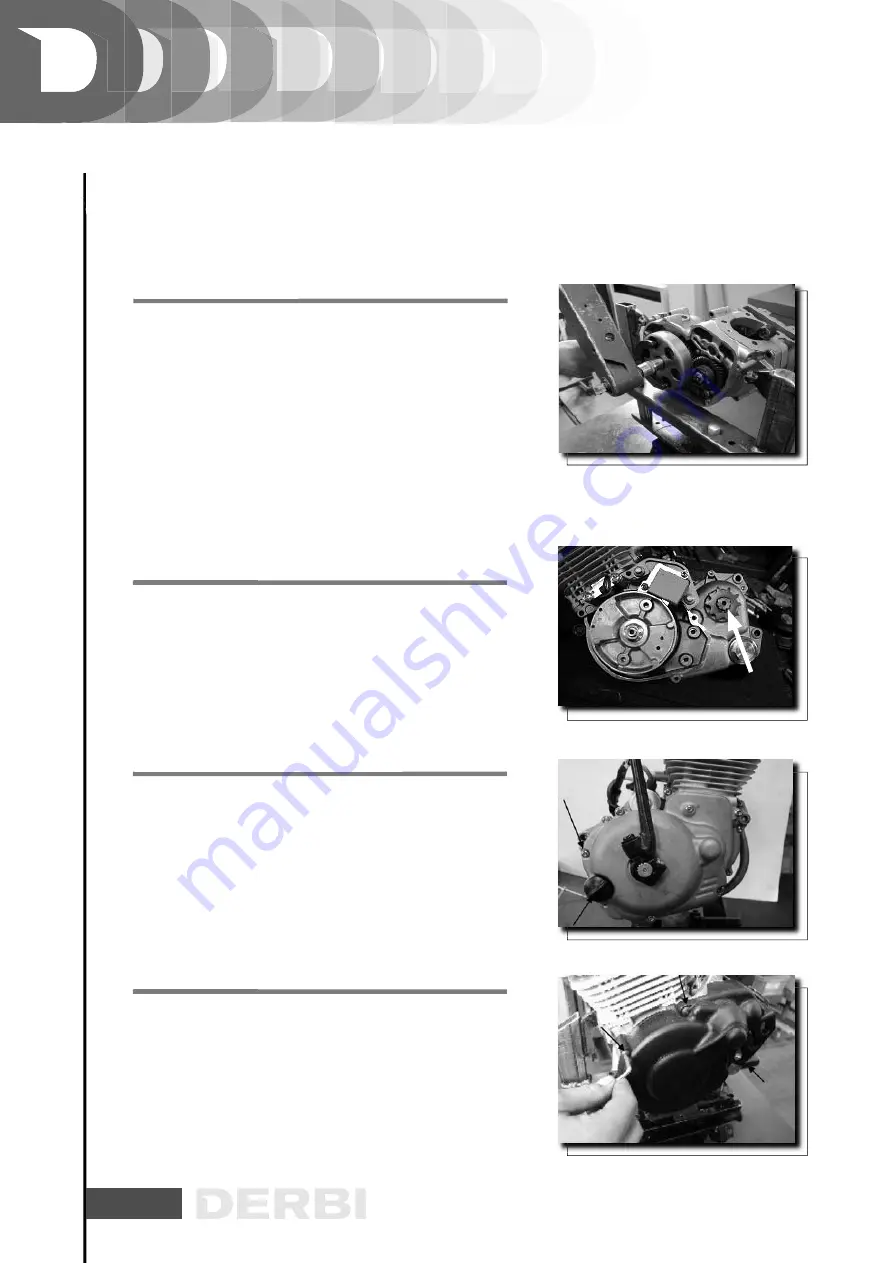
16
R
EFITTING
THE
CLUTCH
- Before refitting the assembly, carefully grease the roller
bearing inside the gear housing.
- Refit the clutch assembly, the drum washer, and the nut
using the special tool.
-After refitting, ensure the drum spins freely.
Specific tooling
020565Y Compass flywheel stop spanner
Locking torques (N*m)
Coppia di bloccaggio 40-44 Nm
E
ND
GEAR
SHAFT
Insert the chain gear shaft and secure with its circlip, as
shown in the figure.
R
EFITTING
THE
TRANSMISSION
COVER
- Refit the gasket (new).
- Refit the cover tightening the seven screws at the prescribed
torque.
- Refit the oil filler cap.
Locking torques (N*m)
Transmission cover fixing screw: 8 ÷ 10 Nm.
F
LYWHEEL
COVER
R
EMOVING
THE
HUB
COVER
Remove the shroud by acting upon the four fittings, as shown
in the figure.
ENGINE
EE
ENGINE
R
EFITTING
THE
CLUTCH
E
ND
GEAR
SHAFT
R
EFITTING
THE
TRANSMISSION
COVER
F
LYWHEEL
COVER