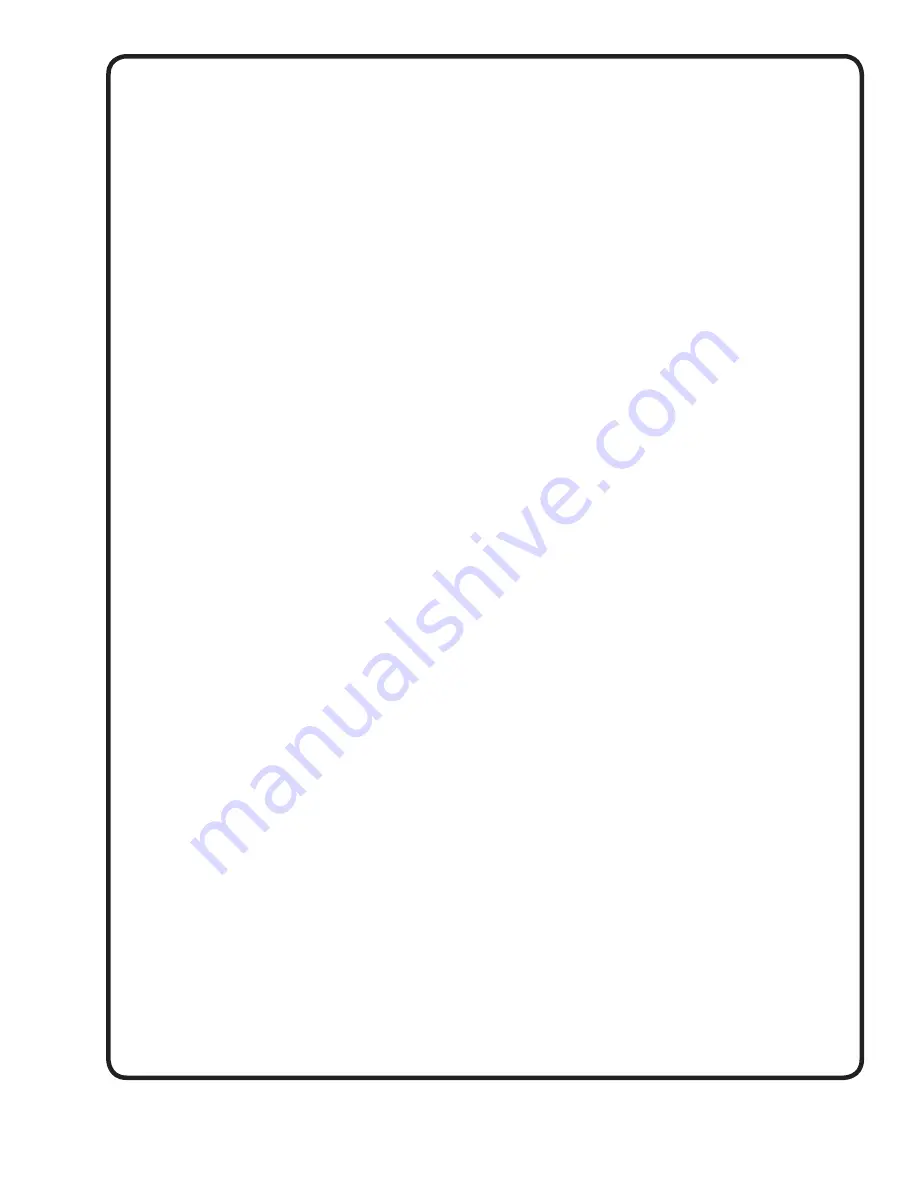
9
WEARING RINGS (8 and 25)
a. To replace suction cover ring (25), remove cap
screw (215) and suction cover (9) from casing (1).
Remove machine screws (343) and then remove
ring (25). Clean ring seat before installing new ring.
b. To replace impeller ring (8), (remove set screws
(296) when used), place a wedge-tipped or
pointed cold chisel against the side of the ring
and tap chisel sharply with a hammer, forcing the
ring from the impeller (2).
5. REASSEMBLY
FRAME (19)
a. Position grease retainer (51) onto the shaft (6) to
position previously-marked and tighten set
screws. Press inboard ball bearing (16) onto the
shaft until inner race is against shaft shoulder.
Apply fresh grease to the bearing (don’t over
grease),
fi ll chamber 1/3 full.
NOTE:
On pumps having Figure No. ending in 9, ie 7159;
fi tted with roller bearing, heat the bearing inner race in an
oven to approx. 400°F then quickly slide race onto the shaft,
until tight against the shaft shoulder.
b. Carefully press outboard ball bearing (18) into the
bearing housing (33) until seated in the bottom
of the housing. Press bearing housing assembly
onto the shaft (6) until bearing inner race is
against shaft shoulder. Apply fresh grease to the
being and the housing.
If bearings are oil lubricated, Figure 7160 Series
only, apply light oil to exterior of the bearing
housing (33) and o-ring (232) before inserting in
frame.
c. Insert shaft assembly into the frame from the
coupling end until the space between the fl ange
of the bearing housing and end of the frame is
approximately as shown below:
Pump Fig. No. ending in 3, 5, 6, 6H - 5/16” space
Pump Fig. No. ending in 8 (7158) - 3/8” space
Pump Fig. No. ending in 9 (7159) - 3/8” space
Replace cap screws (213) fi nger-tight.
On pumps having Fig. No. ending in 9 (7159),
apply grease to outer race and rollers of the roller
bearing (16) and in frame bore then guide bearing
over shaft and insert bearing into the frame until
the outer race is against shoulder in the frame bore.
d. Place bearing lock washer (69) on the shaft and
thread bearing lock nut (22) tight against the lock
washer. Bend tangs of the washer into the lock
nut when tight.
e. Press shaft seal (49) into the bearing cover (37)
with lip of the seal extending toward the coupling.
Position bearing cover over the bearing housing
(33) and replace and tighten cap screws (332),
also replace jack screws with nuts (286 and 204),
but do not tighten.
On pumps with Fig. No. ending in 8 or 9, press
inboard shaft seal (47) into the bearing cover
(35) with lip of seal extending toward the casing
(1). Press grease retainer into the frame bore and
replace capscrews (219) where used.
SHAFT SLEEVE (14)
a. Pumps having Fig. No. ending 3, 5, 6, 6H, having shrink
fi t sleeve.
1. After old sleeve has been removed, clean shaft
with emery cloth and wipe thoroughy to remove
metal particles, also wipe inside of new sleeve to
be sure that it is clean.
2. Note that the new shaft sleeve is chamfered on
one end. This end will be installed against the
shoulder of the shaft (6).
3. Place the shaft sleeve in a preheated oven set at
650
0
F for 1-1/2 hours to allow sleeve to heat
uniformly and expand.
4. Place shaft in a vertical position in a vise, impeller
end upward. Remove shaft sleeve from the oven
and drop sleeve, chamfered end fi rst, over the
shaft; making certain that the end of the sleeve is
seated against the shaft shoulder.
5.
NOTE:
This operation must be done rapidly
without allowing the shaft sleeve to cool. Do not
allow the sleeve to stop before it is properly seated.
Hold Shaft sleeve snug against the shaft shoulder
until shrink begins. Allow the sleeve to cool below
100
0
F before proceeding with pump assembly.
b. Pumps having Fig. No. ending in 8 or 9:
1. After old sleeve has been removed clean shaft
with emery cloth and wipe thoroughly to remove
metal particles also wipe inside of new sleeve
to be sure that it is clean. Apply light oil to shaft
and Permatex® or Silastic® to end of sleeve that
will seat against shaft shoulder.
2. Place shaft sleeve key (279) in keyway, align
sleeve keyway with key and press sleeve onto
shaft until tight against shaft shoulder.
c. Replace defl ector (40) according to original location.
PACKING BOX COVER (11) ASSEMBLY
a. To install new packing see Section D, Paragrah 3.
Position packing box cover against frame (19)
Be sure registered fl ange is fully-seated in power
frame.
b. To install mechanical shaft seal, clean and
inspect all parts and remove all burrs, nicks, etc.
from shaft and sleeve.
CAUTION:
Protect the
lapped faces of the seal during installation.
WITH TYPE 1 CRANE DOUBLE SEAL
a. Pumps with Fig. No. ending in 3, 5, 6, 6H.
1. Apply light oil to the outer surface of the
stationary seal seats and O-rings (89A) and press
one seal seat into the seal gland (251), and the
other seal seat into the packing box cover (11).
Slide seal gland and gand gasket (259) onto the
shaft. (See Drawing).
2. Apply light oil to the inside of the seal bellow and
shaft sleeve (14) and slide the rotating seat
assembly (89B) onto the shaft sleeve.
3. Place packing box cover (11) against frame
(19). Be sure register is aligned and fl ange is
fully seated in power frame and in proper position.
Then attach seal gland (251) to packing box
cover with belts and nuts (209-210). Tighten
securely. Seal may be tested for leakage by
applying 20 pounds of water ressure to the seal
cavity of packing box cover.