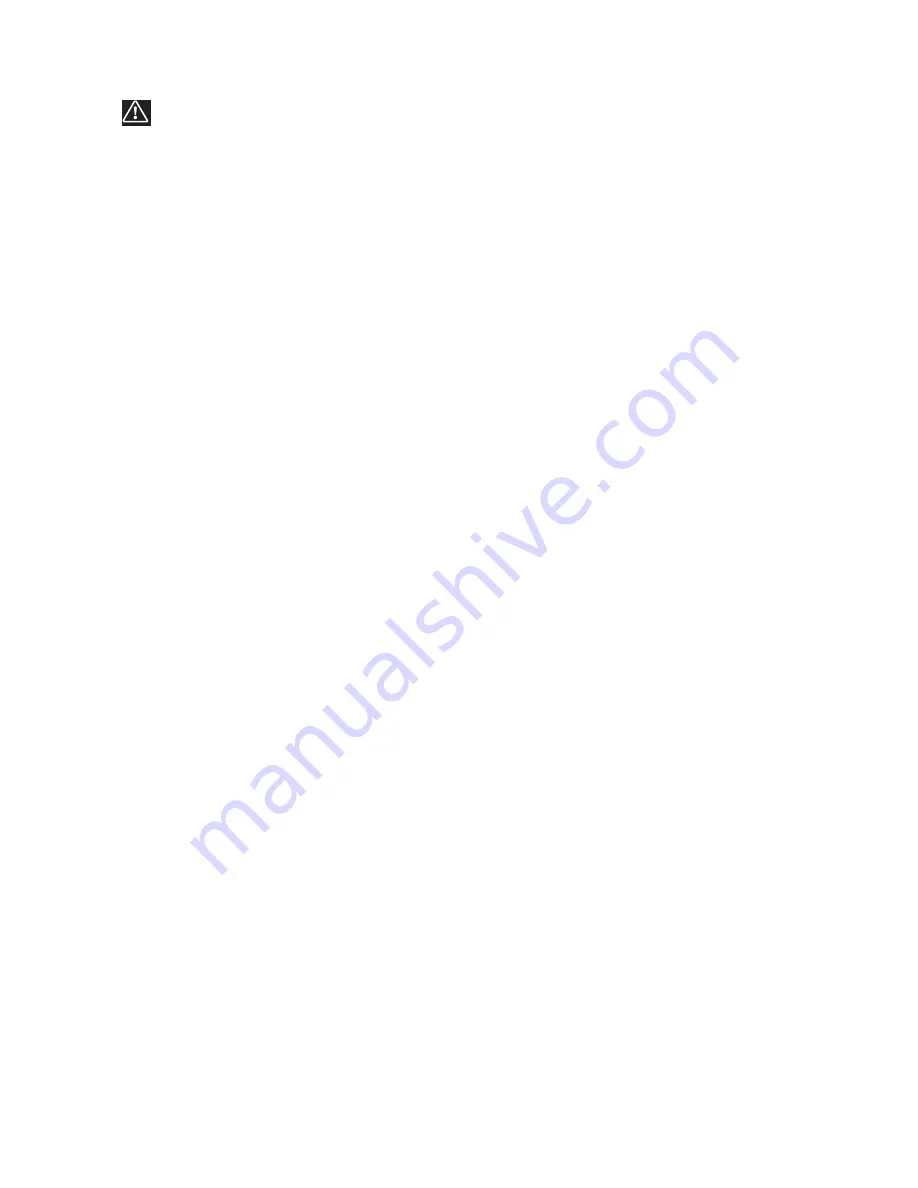
3
ADDITIONAL SAFETY RULES FOR
FOR DRILL PRESSES
1.
DO NOT OPERATE THIS TOOL UNTIL
it is
assembled
and
installed
according to the
instructions.
2.
OBTAIN ADVICE from your supervisor, instructor,
or another qualified person
if you are not familiar
with the operation of this tool.
3.
FOLLOW ALL WIRING CODES
and recommended
electrical connections.
4.
NEVER START THE MACHINE BEFORE
CLEARING THE TABLE
of all objects (tools, scrap
pieces, etc.).
5.
NEVER START THE MACHINE
with the drill bit,
cutting tool, or sander against the workpiece.
6.
TIGHTEN ALL LOCK HANDLES
before starting the
machine.
7.
USE ONLY DRILL BITS, CUTTING TOOLS,
SANDING DRUMS, OR OTHER ACCESSORIES
that have shanks of 1/2" in diameter or less.
8.
USE ONLY DRILL BITS, CUTTING TOOLS, OR
SANDING DRUMS
that are not damaged.
9
. PROPERLY LOCK DRILL BIT, CUTTING TOOL,
OR SANDING DRUM IN THE CHUCK
before
operating this machine.
10.
USE RECOMMENDED SPEEDS
for all operations.
11.
AVOID AWKWARD OPERATIONS AND HAND
POSITIONS
where a sudden slip could cause a
hand to move into the cutting tool.
12.
KEEP ARMS, HANDS, AND FINGERS
away from
the cutting tool.
13.
HOLD THE WORKPIECE FIRMLY AGAINST THE
TABLE.
Do not attempt to drill a workpiece that
does not have a flat surface against the table.
Prevent the workpiece from rotating by clamping it
to the table or by securing it against the drill press
column.
14.
TURN THE MACHINE “OFF” AND WAIT FOR THE
DRILL BIT, CUTTING TOOL, OR SANDER TO
STOP TURNING
prior to cleaning the work area,
removing debris, removing or securing workpiece,
or changing the angle of the table. A moving drill bit,
cutting tool, or sander can be dangerous.
15
PROPERLY SUPPORT LONG OR WIDE
workpieces
.
16.
NEVER PERFORM LAYOUT, ASSEMBLY
, or set-
up work on the table/work area when the machine is
running.
17
TURN THE TOOL “OFF”, disconnect the tool
from
the power source before installing or removing
accessories, before adjusting or changing set-ups,
or when making repairs.
18.
DISCONNECT THE TOOL
from the power source,
and clean the table/work area before leaving the
tool.
LOCK THE SWITCH IN THE “OFF” POSITION
to prevent unauthorized use.
19.
ADDITIONAL INFORMATION
regarding the safe
and proper operation of this tool is available from the
Power Tool Institute, 1300 Summer Avenue,
Cleveland, OH 44115-2851. Information is also
available from the National Safety Council, 1121
Spring Lake Drive, Itasca, IL 60143-3201. Please
also refer to the American National Standards
Institute ANSI 01.1 Safety Requirements for
Woodworking Machines and the U.S. Department of
Labor OSHA 1910.213 Regulations.
WARNING: FAILURE TO FOLLOW THESE RULES MAY RESULT IN SERIOUS PERSONAL INJURY.
SAVE THESE INSTRUCTIONS
.
Refer to them often
and use them to instruct others
.