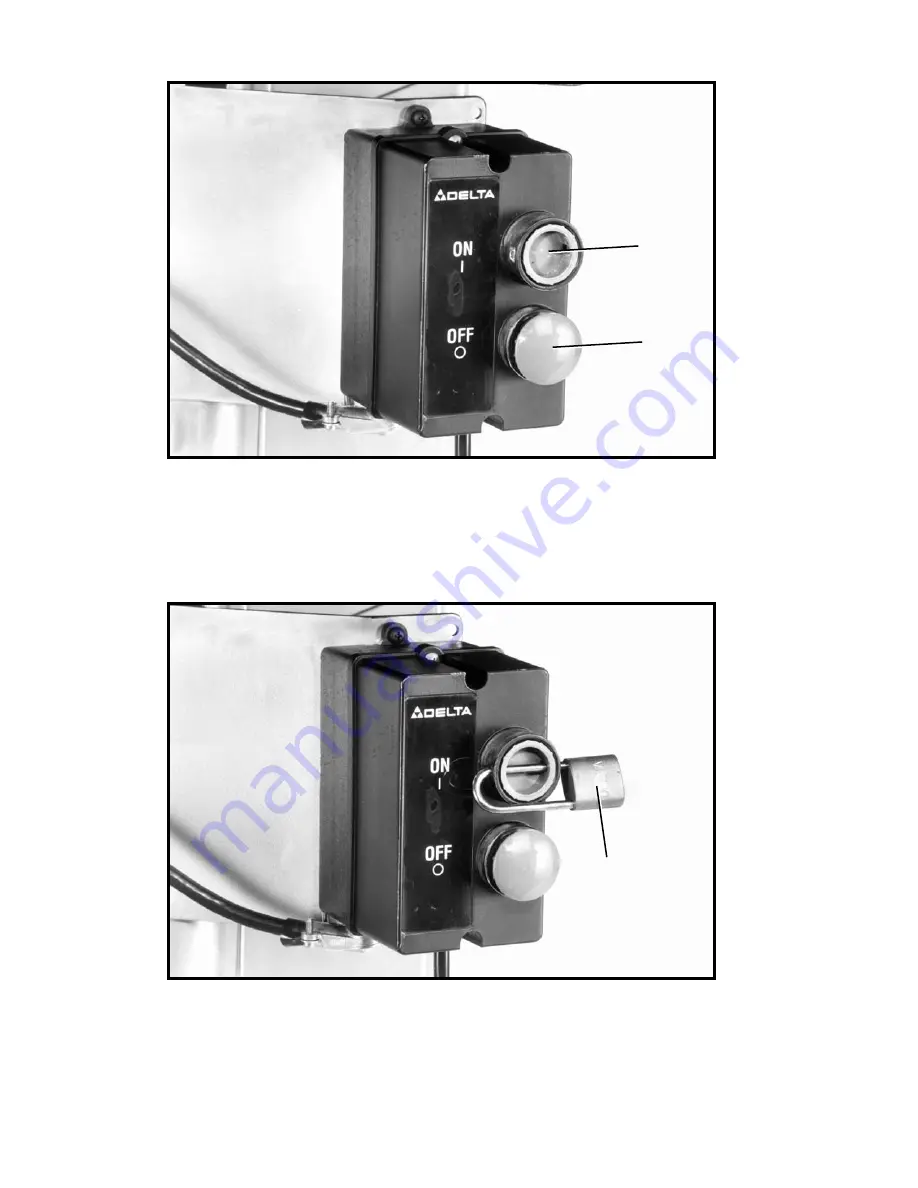
16
STARTING AND STOPPING THE SHAPER
To apply power to the machine, push “ON” button (A) Fig. 43. To stop the machine,
push “OFF” button (B).
LOCKING SWITCH IN THE “OFF” POSITION
IMPORTANT:
We suggest that when the shaper is not in use, the switch be locked
in the “OFF” position using a padlock (C) Fig. 44 , through the switch plate and “ON”
button as shown.
OPERATING CONTROLS AND ADJUSTMENTS
Fig. 43
Fig. 44
A
C
B