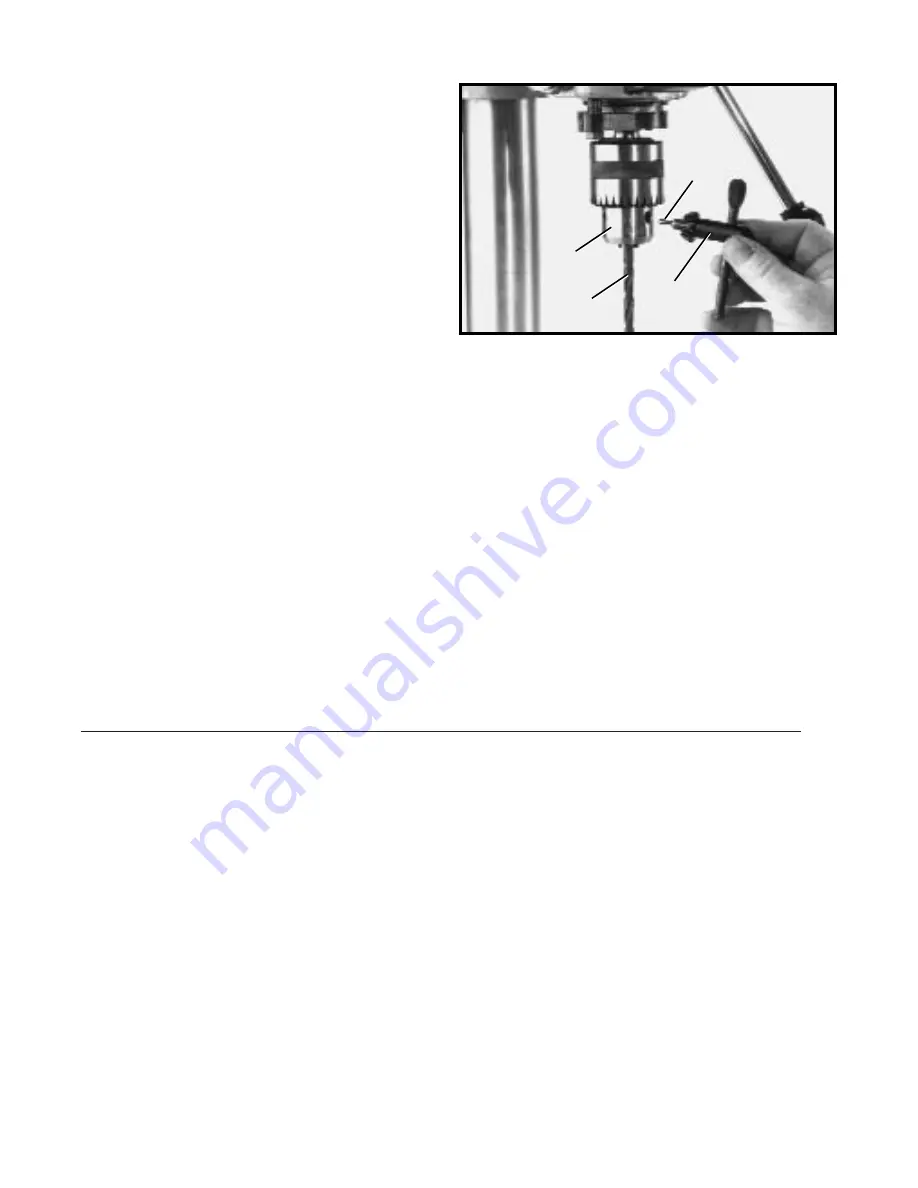
14
BORING IN WOOD
Twist drills, although intended for metal drilling, may also be used for boring holes in wood. However,
machine spur bits are generally preferred for working in wood; they cut a square bottom hole and are
designed for removal of woodchips. Do not use hand bits which have a screw tip; at drill press speeds
they turn into the wood so rapidly as to lift the work off the table and whirl it.
For through boring, line up the table so that the bit will enter the center hole to avoid damage. Scribe
a vertical line on the front of the column and a matchmark on the table bracket, so that the table can
be clamped in the center position at any height.
Feed slowly when the bit is about to cut through the wood to prevent splintering the bottom face. Use
a scrap piece of wood for a base block under the work. This helps to reduce splintering and protects
the point of the bit.
DRILLING METAL
Use clamps to hold the work when drilling in metal. The work should never be held in the bare hand;
the lips of the drill may seize the work at any time, especially when breaking through the stock. If the
workpiece is whirled out of the operator’s hand, he may be injured. The drill will be broken when the
work strikes the column.
The work must be clamped firmly while drilling; any tilting, twisting or shifting results not only in a rough
hole, but also increases drill breakage. For flat work, lay the piece on a wooden base and clamp it
firmly down against the table to prevent it from turning. If the piece is of irregular shape and cannot be
laid flat on the table, it should be securely blocked and clamped.
INSTALLING AND REMOVING DRILL BITS
1.
Insert smooth end of drill bit (A) Fig. 31, as far as it
will go into the chuck (B), and then back the bit out
1/16”, or up to the flutes for small bits.
2.
Make certain that the drill bit (A) Fig. 31, is centered
in the chuck (B) before tightening the chuck with the key
(C).
3.
Turn the chuck key (C) Fig. 31, clockwise to tighten
and counterclockwise to loosen the chuck jaws.
4.
Tighten all three chuck jaws to secure the drill bit
sufficiently so that it does not slip while drilling.
5.
MAKE SURE
chuck key (C) Fig. 31, is removed from
chuck before starting drill press. Your chuck key (C) is
equipped with a self-ejecting pin (D) which eliminates
the hazard of the key being left in the chuck.
C
D
B
A
Fig. 31
Summary of Contents for 17-900
Page 15: ...15 NOTES...