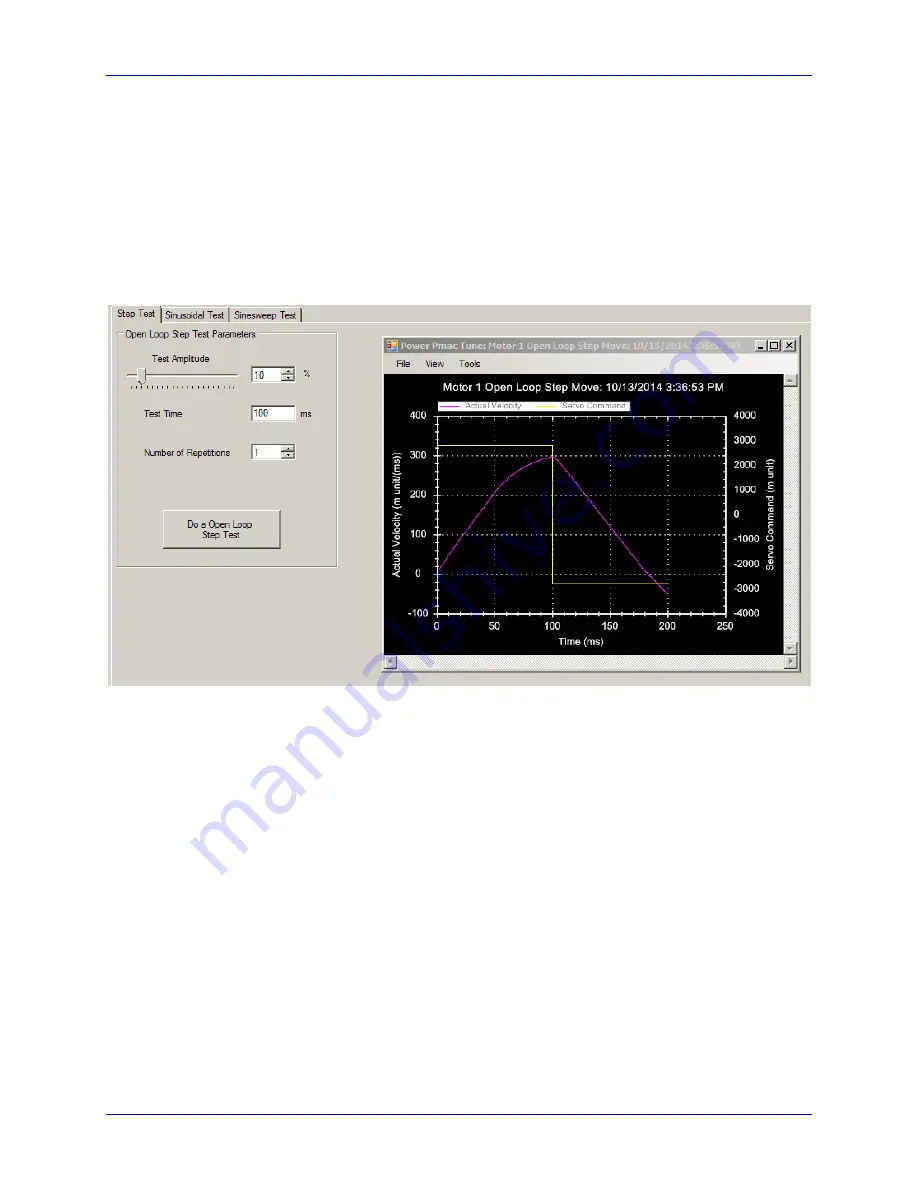
Power PMAC Clipper User Manual
DRIVE - Motor Setup
62
Open Loop Test: Encoder/Decode
The open-loop test is critical to verify the direction sense of the encoder counting versus the command
output. A positive command should create a positive velocity and a position counting in the positive
direction; a negative command should create a negative velocity and a position counting in the negative
direction. The Open Loop test utility in the IDEs “Tune” tool can be used to execute and open loop test. It
can also be carried manually from the terminal window while gathering position, velocity data or simply
monitoring the motor velocity in the position window.
Satisfactory Open-Loop Test Result
The open-loop test is usually performed on an unloaded motor. The open loop command output is
adjustable, start off with a conservative 1 to 2 percent command output (i.e. #1Out2) value and increment
gradually until you see a satisfactory result.
If the failure persists (inverted saw tooth, as shown in the plot), or you observe oscillations in the
response instead of a saw tooth, then most likely the direction sense of the encoder is opposite to the
command output.
General recommendation for troubleshooting an unsuccessful open loop test
An inverted saw tooth response, most times, indicates that the direction sense of the encoder is opposite to
that of the command output.
Quadrature | Sinusoidal:
Change
Clipper[0].Chan[j].EncCtrl
to 3 from 7 (default) or vice-versa.
Absolute Serial Encoders (EnDat, SSI, BiSS, Yaskawa, Panasonic, Tamagawa, Mitutoyo):
The Power PMAC Clipper has no control on the direction sense of the serial data stream
(packets). There are no software parameters that allow changing the direction sense of absolute
serial encoders. Normally, it is set by jumpers or software at the encoder side.