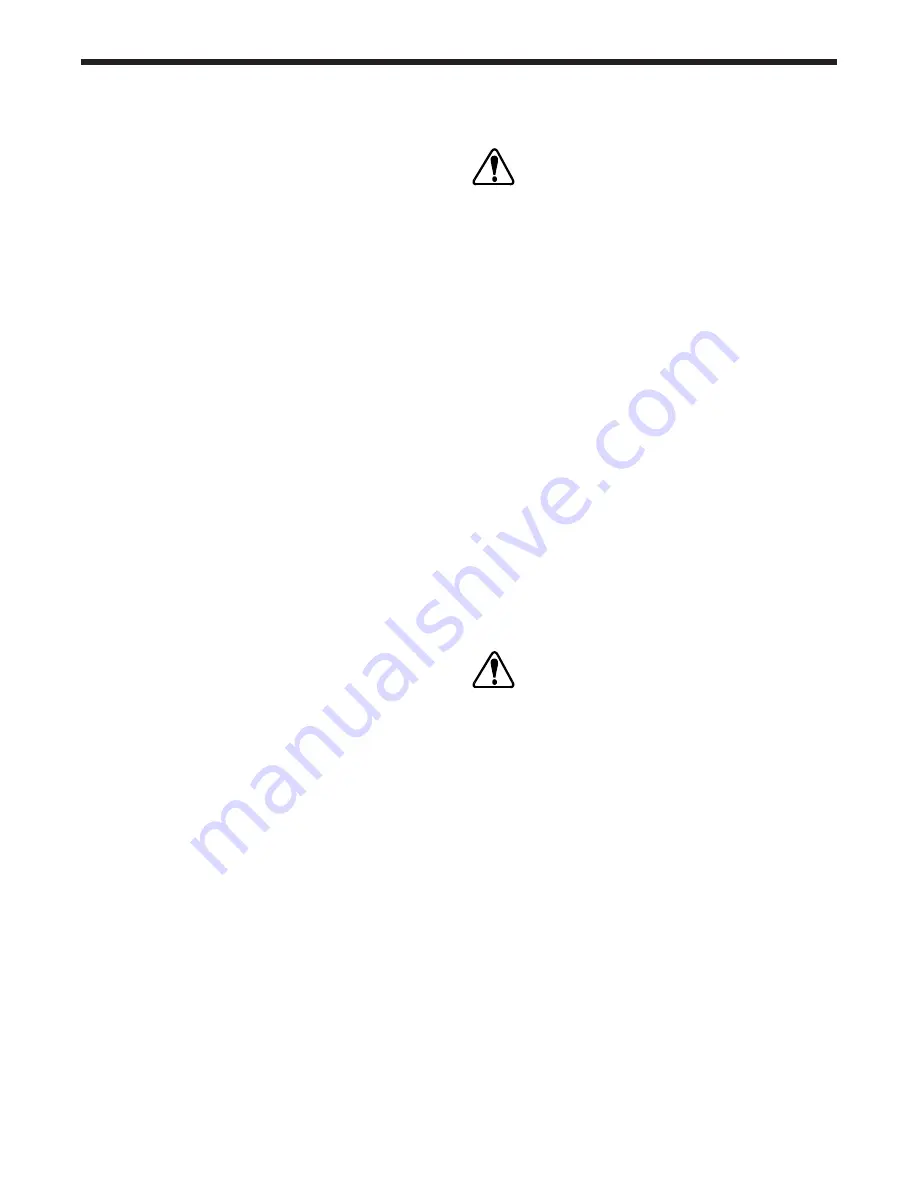
22
Delfield
3.
Adjust the time/temperature control for the
freezer to the desired temperature and time
settings.
4.
Set the temperature control for the desired tem-
perature
5.
Turn the unit off by placing the POWER ON/
OFF switch in the OFF position.
6.
Clean equipment as discussed in the mainte-
nance section of this manual.
CONVERT-A-TEMP
This unit can be used as either a refrigerator or a freezer.
A key switch located behind the hinged upper shroud
performs conversion. A master POWER ON/OFF switch
controls power to the unit.
In the refrigeration mode the temperature is held be-
tween 27°F and 44°F. In the freezer mode the tempera-
ture is held between -5°F and 0°F. Refrigerant is metered
using a highly responsive thermostatic expansion valve.
Evaporator defrost is automatic off cycle in refrigeration
mode and a time initiated, time/temperature terminated
system with electric heaters in the freezer mode. Evapo-
rator condensate is eliminated using an energy efficient
hot gas system. An exterior digital thermometer monitors
cabinet temperature. To operate the Convert-A-Temp
cabinet, refer to Figure 6 for location of operating controls
and proceed as follows:
1.
Check that unit is properly connected to the
power source.
2.
Set the main POWER ON/OFF switch, to the
ON position.
3.
Using the key switch select either the refrigera-
tor or freezer mode.
4.
Adjust the electronic temperature control to the
desired temperature.
5.
Turn the unit off by placing the POWER ON/
OFF switch in the OFF position.
6.
Clean equipment as discussed in the mainte-
nance section of this manual.
MAINTENANCE
Stainless Steel Care and Cleaning
To prevent discoloration of rust on stainless steel several
important steps need to be taken. First, we need to
understand the properties of stainless steel. Stainless
steel contains 70-80% iron which will rust. It also contains
12-30% chromium, which forms an invisible passive film
over the steels surface, which acts as a shield against
corrosion. As long as the protective layer is intact, the
metal will not corrode. If the film is broken or contami-
nated, outside elements can begin to breakdown the
steel and begin to form rust or discoloration.
Proper cleaning of stainless steel requires soft cloths or
plastic scouring pads.
CAUTION
Never use steel pads, wire brushes or scrapers!
Cleaning solutions need to be alkaline based or non-
chloride cleaners. Any cleaner containing chlorides will
damage the protective film of the stainless steel. Chlo-
rides are also commonly found in hard water, salts and
household and industrial cleaners. If cleaners containing
chlorides are used, be sure to rinse repeatedly and dry
thoroughly upon completion.
Routine cleaning of stainless steel can be done with soap
and water. Extreme stains or grease should be cleaned
with a non-abrasive cleaner and plastic scrub pad. It is
always good to rub with the grain of the steel. There are
also stainless steel cleaners available which can restore
and preserve the finish of the steels protective layer.
Early signs of stainless steel breakdown can consist of
small pits and cracks. If this has begun, clean thoroughly
and start to apply stainless steel cleaners in attempt to
restore the passivity of the steel.
Never use an acid based cleaning solution! Many food
products have an acidic content which can deteriorate
the finish. Be sure to clean ALL food products from any
stainless steel surface. Common items include toma-
toes, peppers and other vegetables.
DANGER
The power must be turned off and disconnected
whenever performing maintenance or repair func-
tions.
Cleaning the Condenser Coil
The condenser coil requires regular cleaning, recom-
mended is every 90 days. In some instances though you
may find that there is a large amount of debris and dust
or grease accumulated prior to the 90-day time frame. In
these cases the condenser coil should be cleaned every
30 days.
If the build up on the coil consists of only light dust and
debris the condenser coil can be cleaned with a simple
brush. Heavier dust build up may require a vacuum or
even compressed air to blow through the condenser coil.
If heavy grease is present there are de-greasing agents
available for refrigeration use and specifically for the
condenser coils. The condenser coil may require a spray
with the de-greasing agent and then blown through with
compressed air. Coil should be rinsed thoroughly after a
degreasing agent is used.
Summary of Contents for SAH2-S
Page 30: ...30 Delfield NOTES ...
Page 31: ...31 Specification Line ...
Page 32: ...DMSPECLINE 10 05 ...