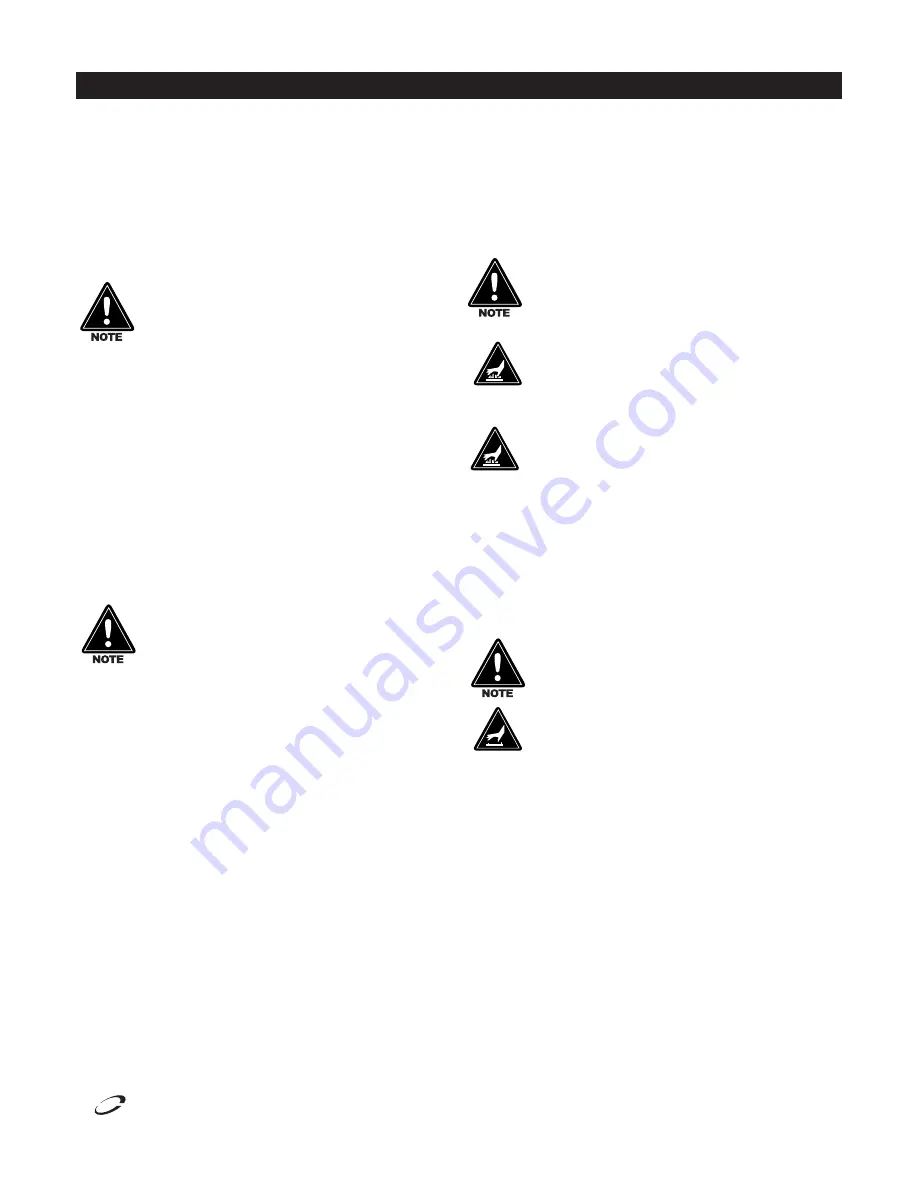
N8000 Series Drop-In Installation and Operation Manual
15
For customer service, call (800) 733-8829, (800) 733-8821, Fax (989) 773-3210, www.delfield.com
Delfield
™
®
These units are designed to hold warm food product between
140ºF to 160ºF (60ºC to 71ºC).
N8700-D, N8700N and N8700-R series individually heated
hot food units may be operated “wet” (with water in the wells)
or “dry”. However, “wet” operation is recommended for better
performance.
N8800 Series single tank hot food units are designed to be
operated “wet” (with water in the tank) only.
Proper water level (approximately 2” [5.1cm])
must be maintained to prevent damage to the
tank on the N8800 Series units.
After the unit is hard wired to the electrical system, select
desired temperature by rotating temperature control. A knob
and indicator light are provided for each individual heated food
well.
First Time Use
Before the unit is used the first time for serving, turn the
temperature knob to “HI” and heat the well for 20 to 30 minutes.
Any residue or dust that adhered to the heater element(s) will
be burned off during this initial preheat period.
When serving thick sauces always use the hot food well in
“wet” operation. This provides more uniform temperature for
the sauce.
Never place food directly in well. Always use
pans.
For most efficient operation, keep covered inserts in each well
during preheating or when empty.
Always place covers on pans when not serving to prevent food
from drying out.
Wet Operation
Fill the food well with a minimum of 2” (5.1cm) of water and
cover with lid or empty pan. To preheat water, set temperature
control at “HI”. With pans in place, wells will boil water. Food
temperature will vary depending on type and amount of product.
To minimize steam and water usage, set control at lowest
setting that will maintain proper food temperature. To reduce
preheating time, use hot water to fill the well.
When operating these units “wet,” never use
anything other than plain water in the wells or
tank. Failure to observe this warning may result
in personal injury or damage to the unit.
When operated at the highest temperature
setting, the top of the unit will become very
hot. Staff and customers using the equipment
should be informed about this.
Steam can cause serious burns. Always use
some type of protective covering on your hands
and arms when removing lids from the unit. Lift
the lid in a way that will direct escaping steam
away from your face and body.
Dry Operation N8700 Series only
Wet operation is usually much more efficient and is preferred.
However, these units may be operated without water with no
damage to the unit.
When operated dry, the bottom of the well will discolor. To clean,
use a stainless steel cleaner or mild abrasive.
The dry well should never be preheated longer
than 15 minutes.
When operated dry, the well bottoms become
very hot. Do not allow unprotected skin to
contact any well surface.
D
A
R
NGE
Operation N8700-D, N8700N, N8700-R & N8800 Series
D
A
R
NGE
D
A
R
NGE