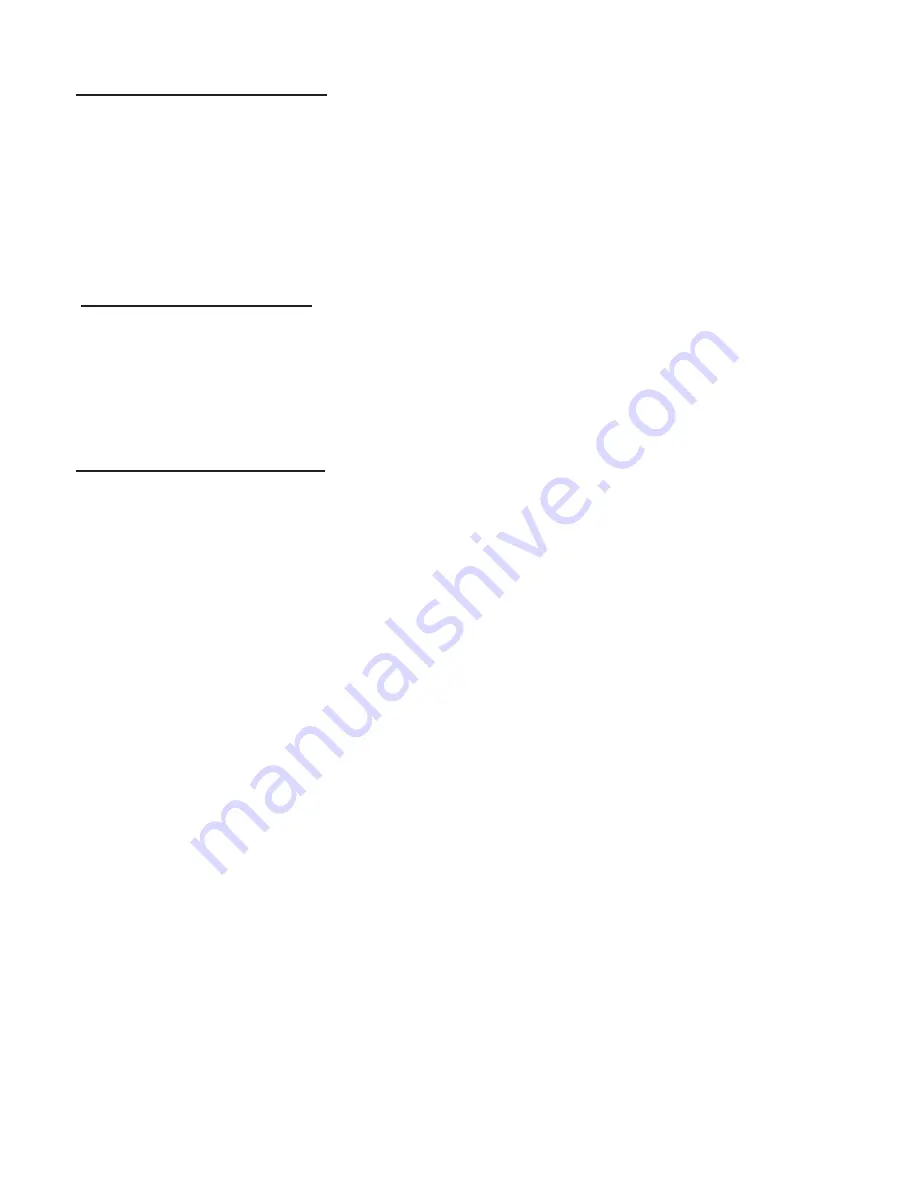
Owner's Manual
Page 8
SHUT DOWN INSTRUCTIONS
1. If the burner is on turn control switch to position 1(pump).
2. Run water through the pump until cool water flows from the cleaning gun. Failure to do this could
result in increased coil scaling.
3. Turn the control switch to off.
4. Turn off the water supply.
5. If the machine will be exposed to freezing temperatures, see winterizing procedure.
THINGS TO CHECK DAILY
1. Check oil level in pump.
2. Fill fuel tank at the end of each day’s use to prevent condensation build-up in fuel system.
3. Fill soap container.
4. Check oil level in engine.
THINGS TO CHECK WEEKLY
1. Check and clean water float tank and pump inlet screen.
2. Check all hoses for leaks and damage. Repair or replace as needed.
3. Check pressure nozzle for wear. Replace if needed.
4. Check all nuts and bolts. Tighten as needed (DO NOT OVER TIGHTEN.)
5. Check all water connections for leaks. Tighten if loose.
6. Check belts and pulleys for wear and tightness. (DO NOT CHECK WHILE MACHINE IS
RUNNING.)
Summary of Contents for C984040V
Page 13: ...Owner s Manual Page 13 Notes ...
Page 14: ...Owner s Manual Page 14 EZ4040G PUMP COMPONENT LOCATOR ...
Page 16: ...Owner s Manual Page 16 UNLOADER COMPONENT LOCATOR ...
Page 19: ...Big Brute Owner s Manual Big Brute 12V ELECTRICAL SCHEMATIC ...
Page 20: ...Manual Page 20 GUNVALVE AND HOSE ASSEMBLY COMPONENT LOCATOR ...
Page 22: ...Manual Page 22 GC 590 40 GUNVALVE COMPONENT LOCATOR ...
Page 24: ...Manual Page 24 1111 E Lake Francis Dr Siloam Springs AR 72761 1 800 BUY DELCO ...