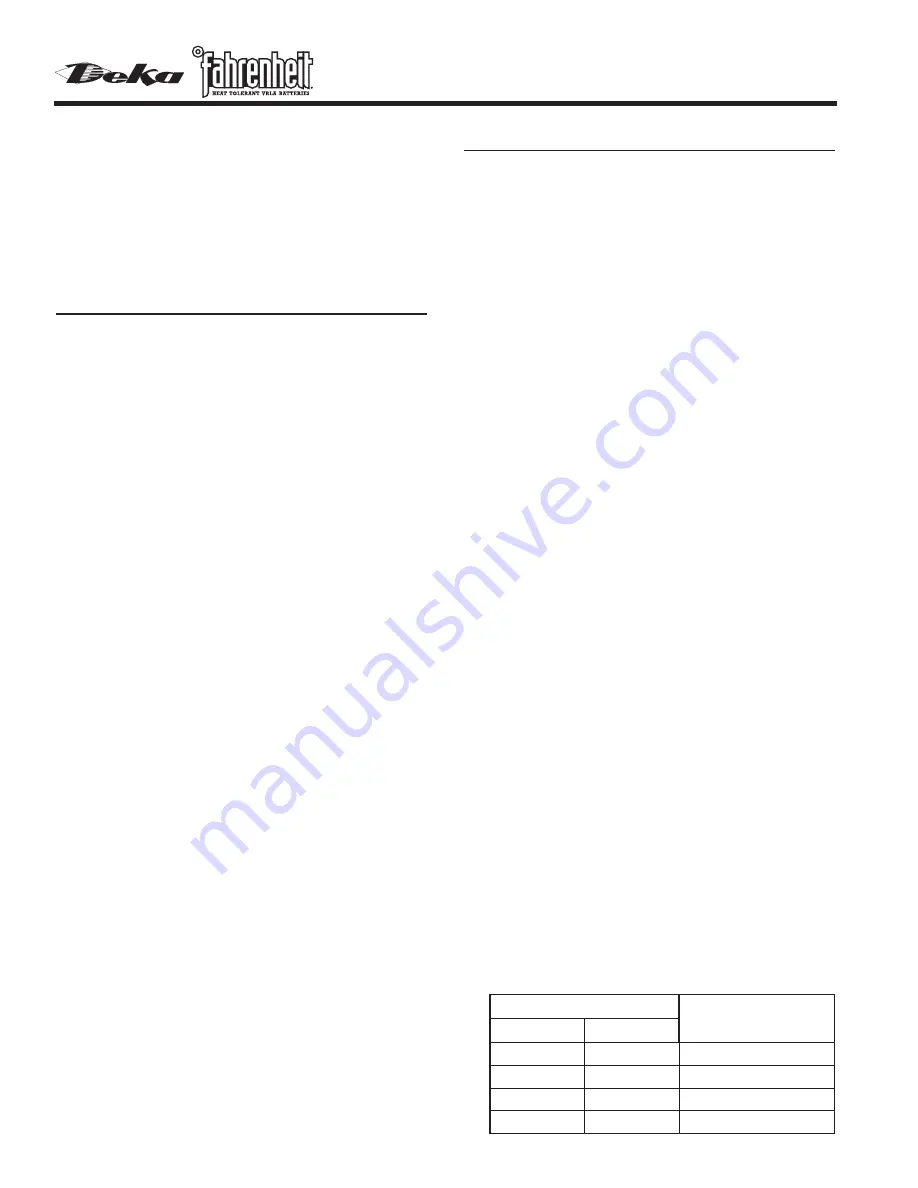
4
®
SYSTEM OPERATIONS
Charger Voltage
These batteries are designed for continuous
float applications.
FLOAT / STANDBY (per battery)
13.50V +/- 0.06 @ 77°F (25°C)
When setting the float voltage on the charger, the
battery string should be set to float at the nominal
battery float voltage times the number of batteries
in the string. The charger must be able to maintain
the system voltage within ± 0.5% of the desired level
at all times. The desired float voltage varies with
temperature.
Consult Voltage Compensation Chart
(Pg. 8 – Appendix B).
TEMPERATURE COMPENSATION
Battery voltage should be adjusted for ambient
temperature variations.
12mV per °C (1.8°F) per 12V battery
Consult Voltage Compensation Chart
(Pg. 8 – Appendix B)
for temperature compensation
voltage maximum and minimum limits.
Charger Current
Charge currrent should not exceed the recommended
min. and max. requirements. Consult
Appendix C
for
min. and max. charge current limits.
Battery Voltage
Although the charger must maintain the system volt-
age within ± 0.5%, individual battery voltages may
vary by ± 0.30V per battery of the average battery
string float voltage.
Equalizing
Upon installation of the battery string, an optional
charge of 14.40V per battery ± 0.06 @ 77°F (25°C) for
24 hours (not to exceed 24 hours) can be applied.
(NOTE: Verify that the higher battery voltage will not
adversely affect any other connected equipment).
If
this is done, be sure to reset the charging equipment
to the proper float voltage.
Battery Operation
Battery operating temperature will affect battery string
capacity and operating life.
Temperatures greater than 95°F (35°C) will reduce the
operating life of the battery. For every 19.8°F (11°C)
increase in operating temperature above 95°F (35°C),
the warranty period will be proportionally reduced by
50% as shown below:
Venting
Under normal operation, VRLA batteries emit hydro-
gen gas, which is combustible at certain concentra-
tions. Proper ventilation should be provided per IEEE
1187 and/or local codes. Some batteries are designed
to accommodate the use of vent tubing. Ventilation
equipment is not designed or supplied by East Penn
Mfg. Safe installation of any venting equipment is the
responsibility of the installer.
BATTERY ASSEMBLY
(ALWAYS WEAR EYE PROTECTION.)
1. Set up the battery string so that the positive post (+)
of one battery is connected to the negative post (–) of
the next battery for all series connections. The inter-
battery connector contact surfaces shall be cleaned
by rubbing gently with a non-metallic brush or pad
before installing connectors.
Only approved oxide inhibitors (No-Ox-ID “A” from
Sanchem, Inc.) may be applied to connections or
battery posts.
2. For future identification, individual batteries should
be numbered in electrical connection sequence, be-
ginning with number one (1) at the positive end of the
battery string.
3. Install all interbattery connectors using lock washer
and bolts loosely to allow for final alignment of bat-
teries, then torque to 100 in lb +/- 5. After torquing the
connections on racked batteries, read the voltage of
the battery string to assure that individual batteries
are connected correctly. The total voltage should be
approximately equal to the number of batteries times
the measured voltage of one battery (when connected
in series). If the measurement is less, recheck the con-
nections for proper voltage and polarity.
4. Read and record interbattery connection resistance
and note the method of measurement. This helps
determine a satisfactory initial installation and can
be used as a reference for future maintenance
requirements.
See Battery Maintenance Report. (Pg.
10 – Appendix D ).
Clean, remake and re-measure any
connection having a resistance measurement greater
than 10% of the average of all the same type of
connections (interbattery, inter-tier or shelf, inter-rack
or intercabinet).
5. Battery performance is based on the output at the
battery terminals. Therefore, the shortest electrical
connections between the battery string and the
operating equipment results in maximum total battery
string performance.
Do not select cable size on current carrying capability
only. Cable size should not provide a greater voltage drop
between the battery system and operating equipment
than specified. Excess voltage drop will reduce the
desired support time of the battery system.
Operating Temperature
Proportional Percentage
(%) of Life
ºF
ºC
95º
35º
100%
100.4º
38º
80%
109.4º
43º
60%
114.8º
46º
50%