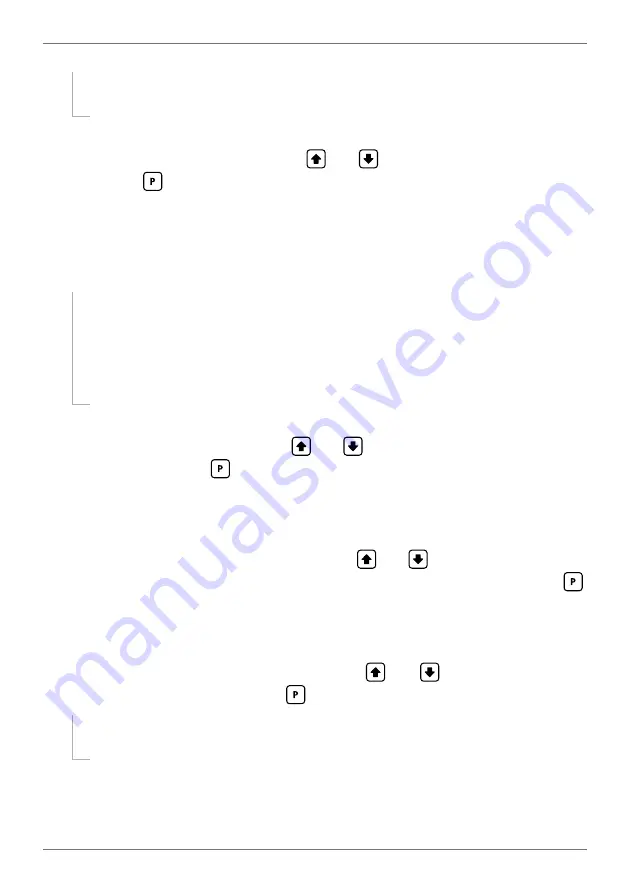
PRO-WEI100-MAN-19V01 (0225)
Copyright © 2019 Define Instruments
25
¨
If you are currently editing
SP 1
, skip to 7.2E now.
¨
If you are currently editing
SP 2–4
, continue to 7.2D now.
D _ _ _ TRAIL SP1
scrolls across the display and toggles with the tracking setting
for the selected setpoint. Using the
and
buttons, select
OFF
or
ON
, and
then press
.
A setpoint with
TRAIL SP1
enabled will track the setpoint value of
SP 1
, with the setpoint value
of the tracking setpoint becoming an offset value.
E
The step that you proceed to now will depend on which setpoint you are editing
(selected in 7.2A):
¨
If you are currently editing
SP1–2
, then the step that you proceed to now
will depend on your controller's weighing mode (selected in 6.2F):
`
If your controller is in
NORMAL
mode, continue to 7.2F now.
`
If your controller is in
BATCH
mode, skip to 7.2J now.
¨
If you are currently editing
SP 3–4
, continue to 7.2F now.
F
_ _ _ SP SOURCE
scrolls across the display and toggles with the activation source
for the selected setpoint. Use the
and
buttons to choose
NET
/
BATCH
or
LIVE
, and then press
.
Note that where
NET/BATCH
is indicated, the option that will be displayed is controlled by the
weighing mode selected in 6.2F.
NORMAL
mode =
NET
,
BATCH
mode =
BATCH
.
G _ _ _ SP ACTIVATION
scrolls across the display and toggles with the current ac-
tivation for the selected setpoint. Using the
and
buttons, select the relay
activation to operate
ABOVE
or
BELOW
the setpoint value, and then press
.
ABOVE
: Relay turns on above the setpoint value and off below it.
BELOW
: Relay turns on be-
low the setpoint value and off above it.
H _ _ _ HYSTERESIS VALUE
scrolls across the display and toggles with the hyster-
esis value for the selected setpoint. Use the
and
buttons to adjust this
value if required, and then press
.
¨
If you set the Hysteresis Value to
0
, skip to 7.2J now.
¨
If you set the Hysteresis Value to anything else, continue to 7.2I now.
The
HYSTERESIS VALUE
defines the separation band between setpoint activation and deacti-
vation, and will operate as per the
HYSTERESIS TYPE
setting selected in 7.2I.