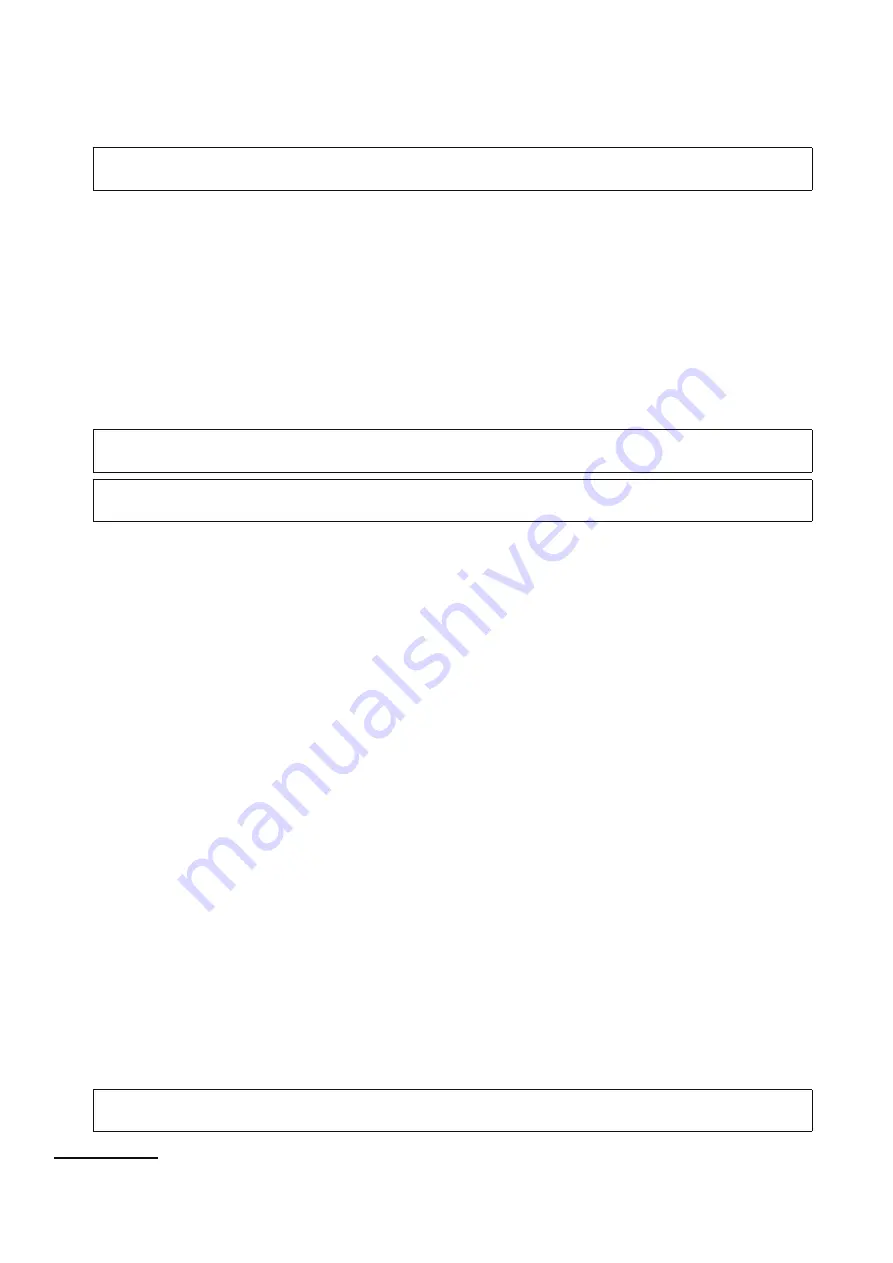
8
4.0 TRAINING
It is the responsibility of the purchaser and the user of this equipment to assure that they understand these
instructions and are trained in the correct care and use of this equipment. They must also be aware of the
operating characteristics, application limits, and the consequences of improper use of this equipment.
IMPORTANT:
Training must be conducted without exposing the user to a fall hazard. Training should be
repeated on a periodic basis.
5.0 INSPECTION
5.1 i-Safe™ RFID TAG:
The i-Safe™ RFID tag on the ExoFit NEX™ Harness (see Figure 7) can be used in
conjunction with the i-Safe handheld reading device and the web based portal to simplify inspection and
inventory control and provide records for your fall protection equipment.
5.2 FREQUENCY:
Before each use inspect the full body harness according to Section 5.3. The harness must
be inspected by a competent person
3
, other than the user, at least annually. Record the results of each
formal inspection in the Periodic Examination and Repair History at the back of the
“General Instructions for Use and
Maintenance” (5902392)
, or use the i-Safe™ inspection web portal to maintain your inspection records. If you
are a
fi
rst-time user, contact Capital Safety (see back cover). If you have already registered, go to: www.
capitalsafety.com/isafe. Follow instructions provided with your i-Safe handheld reader or on the web portal
to transfer your data to your web log.
IMPORTANT:
If the full body harness has been subjected to fall arrest or impact forces it must be
immediately removed from service and destroyed.
IMPORTANT:
Extreme working conditions (harsh environments, prolonged use, etc.) may require
increasing the frequency of inspections.
5.3 INSPECTION:
Inspect the ExoFit NEX™ Full Body Harness as follows:
Step 1.
Inspect harness hardware (buckles, D-rings, pads, loop keepers, vertical torso
adjusters):
These items must not be damaged, broken, distorted, and must be free of sharp
edges, burrs, cracks, worn parts, or corrosion. PVC coated hardware must be free of cuts, rips,
tears, holes, etc. in the coating to ensure non-conductivity. Ensure that release tabs on buckles
work freely and that a click is heard when the buckle engages. Inspect vertical torso adjusters
for proper operation. Ratchet knobs should turn with ease in a clockwise direction and should
only turn counterclockwise when the knob is pulled out. Readjust buckles and pads periodically to
expose and inspect hidden areas on webbing and hardware.
Step 2.
Inspect webbing:
Material must be free of frayed, cut, or broken
fi
bers. Check for tears,
abrasions, mold, burns, or discoloration. Inspect stitching; check for pulled or cut stitches. Broken
stitches may be an indication that the harness has been impact loaded and must be removed
from service. When performing the annual formal inspection, unsnap and open the back pad to
facilitate inspection of the webbing.
Step 3.
Inspect the labels:
All labels should be present and fully legible (see back pages).
Step 4.
Inspect system components and subsystems:
Inspect each system component or subsystem
according to manufacturer’s instructions.
Step 5.
Record inspection data:
Record the inspection date and results on the Periodic Examination and
Repair History at the back of the
“General Instructions for Use and Maintenance” (5902392)
.
Step 6.
Inspect the Stitched Impact Indicator:
The stitched impact indicator is a section of webbing
that is lapped back on itself and secured with a speci
fi
c stitch pattern holding the lap (see
Figure 8). The stitch pattern is designed to release when the harness arrests a fall or has been
subjected to an equivalent force If the impact indicator has been activated the harness must be
removed from service and destroyed.
Step 7.
Inspect Suspension Trauma Straps:
Check the trauma strap pouches for damage and secure
connection to the harness. Unzip the trauma strap pouch on each hip of the harness and inspect
suspension trauma straps. Webbing and pouch material must be free of frayed, cut, or broken
fi
bers. Check for tears, abrasions, mold, burns, discoloration, or knots. Verify that one pouch is
marked
‘Hook’
and the other marked
‘loop’
.
IMPORTANT:
If inspection reveals a defective condition, remove the unit from service immediately and
destroy it.
3 Competent Person:
One who is capable of identifying existing and predictable hazards in the surroundings or working
conditions which are unsanitary, hazardous, or dangerous to employees, and who has authorization to take prompt
corrective measures to eliminate them.