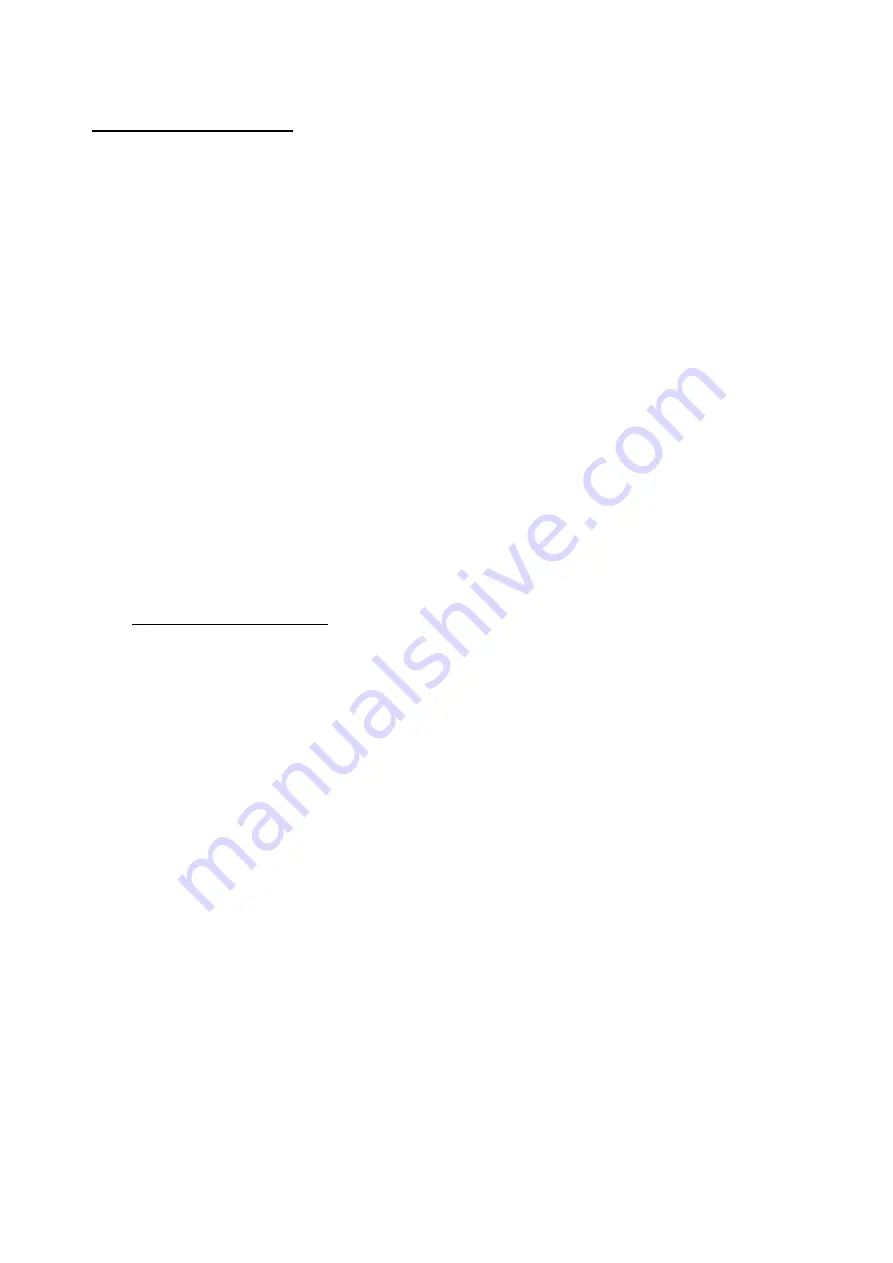
6.0 MAINTENANCE
The Excavator Mounted Vibrators have been designed to give years of trouble free service.
Providing the equipment is treated with respect and the basic maintenance procedures are adhered
to there will be little work additional work required.
The most important points are correct installation on good quality excavators, cleanliness when
connecting to the excavator’s hydraulic system and regular gearbox oil changes using appropriate
oils - again cleanliness is paramount.
Visual inspection of the EMV by a competent person on a daily basis and before being taken into
service can prevent many potential problems from occurring. Ensure that lifting accessory test
certificates are correct and valid at all times.
•
All service and maintenance work must be carried out by qualified personnel using
original Dawson parts. The use of other parts will invalidate the whole warranty for the
equipment.
•
The equipment should be inspected at ground level only and should be positioned so as
to be stable at all times.
•
Secure the equipment against unexpected starting during the maintenance process.
•
The equipment should be inspected by a Dawson technician or by one of their approved
distributors once a year or every 1000 working hours.
6.1 Daily
Maintenance.
a.
Grease the two grease points on the EMV300
– one on the Saddle Swivel and
the other on the side of the Clamp Body. Two or three pumps with a
molybdenum-based grease will be adequate.
b.
Check visible screws, bolts, fittings etc for tightness.
c.
Visually inspect all hydraulic hoses and fittings for leaks or damage.
d.
Check the gear oil level in the vibrator.
The level must be half way up the sight
glass.
e.
Inspect the lifting chain and chain clamp for damage.
The chain should be in
good order, free from any structural damage or permanent deformation of any
kind. The chain clamp should also be free from any structural damage and its
correct operation and safe function should be checked by depressing and releasing
several times – any binding or hesitancy with its operation should result in it being
changed for a new certified item. The chains Coupler and anchorage point should
be in good order showing no signs of damage, wear or cracking. Remember
if in
doubt change it
– Chains, Chain Clamps & Couplers require new test certificates
to be recorded when changed!
f.
Inspect the condition of the Hard Jaws.
To be acceptable these should look to
be in almost as new condition. The teeth on these pads have some flats on them
when new (approximately 1.5x1.5mm). Over time they will round off, flatten out
more and even become chipped. If not changed when required they will loose
Summary of Contents for EMV-300
Page 5: ...Figure 1 Basic Technical Specifications...
Page 28: ...DAWSON CONSTRUCTION PLANT LIMITED 9 0 PARTS LISTS FOR THE EMV300...
Page 29: ......
Page 30: ......
Page 31: ......
Page 32: ......
Page 33: ......
Page 34: ......
Page 35: ......
Page 36: ......
Page 40: ......
Page 45: ...STAND Remarks Inspect general condition of stand...