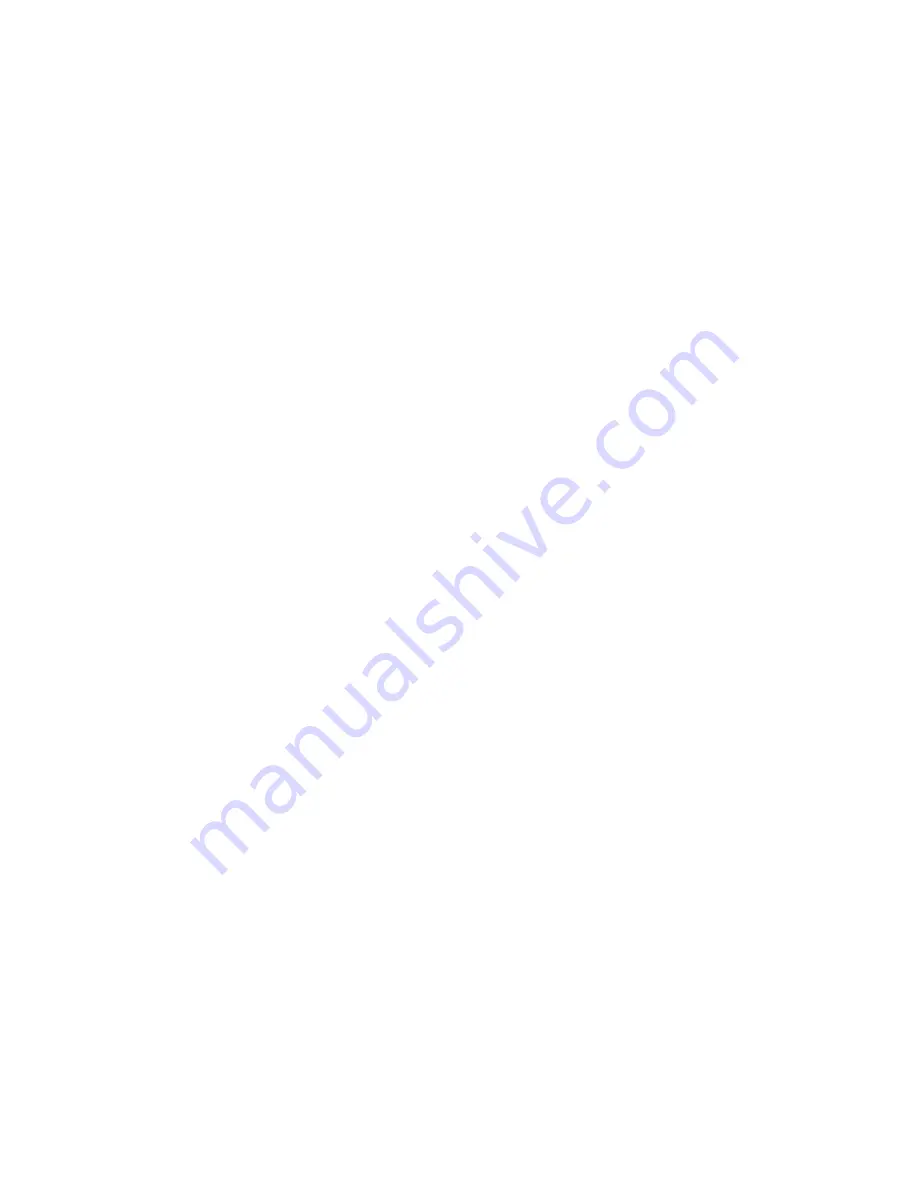
26
SF-1 SHURFLO PUMP WON’T RUN
If the pump has power to it (the fan runs), but the pump itself won’t run, the first thing to check
is the pressure switch. The pressure switch (part no. EL-FP-PS) is located on the wet end of the
pump and has two red wires plugged into it. Jump the two red wires together and see if the
pump runs. You can safely run the system with the pressure switch jumped, just keep an eye on
the pressure gauge and don’t let system pressure exceed 100 psi. Replace the switch when a
spare is available.
If the pump will not run with the pressure switch jumped, then it is most likely a problem with
the brushes or the overheat protection switch inside the motor. The motor will come completely
apart by removing the two screws on the end of the motor. Remove the rear cover and paper
insulator. Pull out the plastic brush holder. The thermal switch is located on one of the brush
leads. With an ohmmeter, check for continuity through the switch. If it is open, you can make
temporary repairs by wiring around it, being careful that your new wiring doesn’t chafe on the
moving parts, nor resist the springs that push the brushes on to the commutator.
If any corrosion is apparent, the brushes may be sticking. Once apart, clean all the carbon dust
from all the parts. Clean the commutator with light sand paper. Make sure to clean the small
grooves on the commutator with a small sharp tool to remove the carbon in between the seg-
ments. Adjust the springs on the brush holders so the brushes slide smoothly in and out. If the
bearings are rough and binding, remove the rubber dust cover and clean the best you can, grease
them, and work it free by hand. Don't service the bearing unless absolutely necessary. Reas-
semble in reverse order. You can hold the carbon brushes back with papers clips inserted
through the slots in the brush holder so they don't hang up on the bearing during assem-
bly. Make sure the corrugated bearing shim doesn't push out, if it does, push it back into place.
This will at least keep you going until the motor can be replaced if necessary.
6/03/04