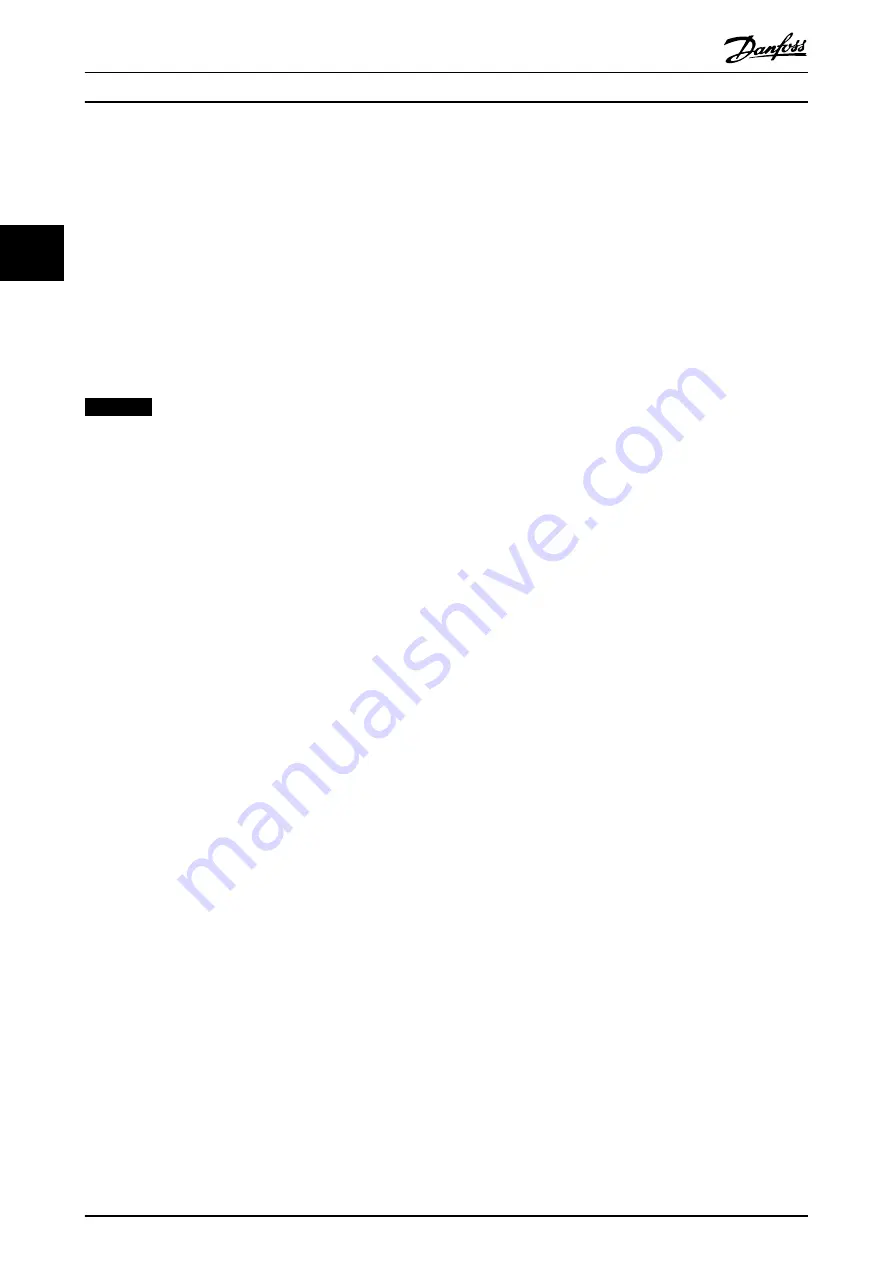
At the first power up, the option shows Blank Initial State.
Properties of safety parameters
•
They are kept separate for each monitoring
channel.
•
During start-up, a checksum (Cyclic Redundancy
Check, CRC) over the safety parameters is
generated and checked. The parameters are
stored on the non-volatile memory on the option.
A reset of the safety parameters to the factory setting can
be executed via MCT 10 Set-up Software.
NOTICE
If the safety option is reinstalled in another frequency
converter, all safety parameters can be selected either
from the safety option or from the frequency converter
in which the option is now installed. A commissioning
test must always be performed to ensure the correct
functionality.
3.6.11 Encoder Interface
CAUTION
Some of the diagnostics performed on the encoder
signals require motion to detect faults. Make sure that
motion occurs at least once every 12 months.
To detect the standstill or the motor speed, the speed
(frequency) is measured using a TTL encoder (MCB 150), an
HTL encoder (MCB 151) or a PNP proximity switch (MCB
151). The HTL encoder uses 2 signal tracks, A and B. TTL
encoders uses 4 signal tracks A, B and their inverted tracks
nA, nB.
Use twisted-pair, individually screened cable to connect
encoders to the safety option.
3.7 Limitations
3.7.1 Exceeded Limit Value and Internal
Errors
•
Exceeding set limit values activate the stop
braking ramp.
•
Any internal error on the safety option or
frequency converter activates the safety function
Safe Torque Off. The frequency converter coasts
the motor.
Internal errors always result in a fault, requiring a power
cycle of the frequency converter to reset the failure.
Alternatively, use
42-90 Restart Safe Option
to restart the
safety option after internal failure without power cycling
the frequency converter.
3.7.2 Compatibility between Safety and
Frequency Converter Functions
The safety option is compatible with all VLT
®
AutomationDrive FC 302 frequency converters in the range
of 0.37 kW to 75 kW. Compliance to higher power ranges
is to come. Contact the local supplier for latest
information.
MCB150/151 can be combined with the following A-
options:
•
PROFIBUS MCB 101
•
DeviceNet MCA 104
•
CanOpen MCA 105
•
PROFINET MCA 120
•
Ethernet/IP MCA 121
•
Modbus TCP MCA 122
•
PowerLink MCA 123
•
EtherCAT MCA 124
The safety option is compatible with asynchronous and
synchronous (PM) motors. Asynchronous motors can be
used in U/f and VVC
+
in closed and open loop as well as in
FLUX open loop control. Synchronous (PM) motors can be
used in U/f open or closed loop control. Compliance to
further motor types and control modes is to come. Contact
the local supplier for latest information.
The following software versions are required as minimum
for using MCB150/151:
•
LCP software version 7.0
•
VLT
®
AutomationDrive FC 302 Firmware Version
6.64
All frequency converters, options and control mode
combinations not listed above are not permitted.
Functions and System Overvi...
Operating Instructions
24
Danfoss A/S © Rev. 2014-02-11 All rights reserved.
MG34W302
3
3
Summary of Contents for VLT Safety Option MCB 150
Page 2: ......