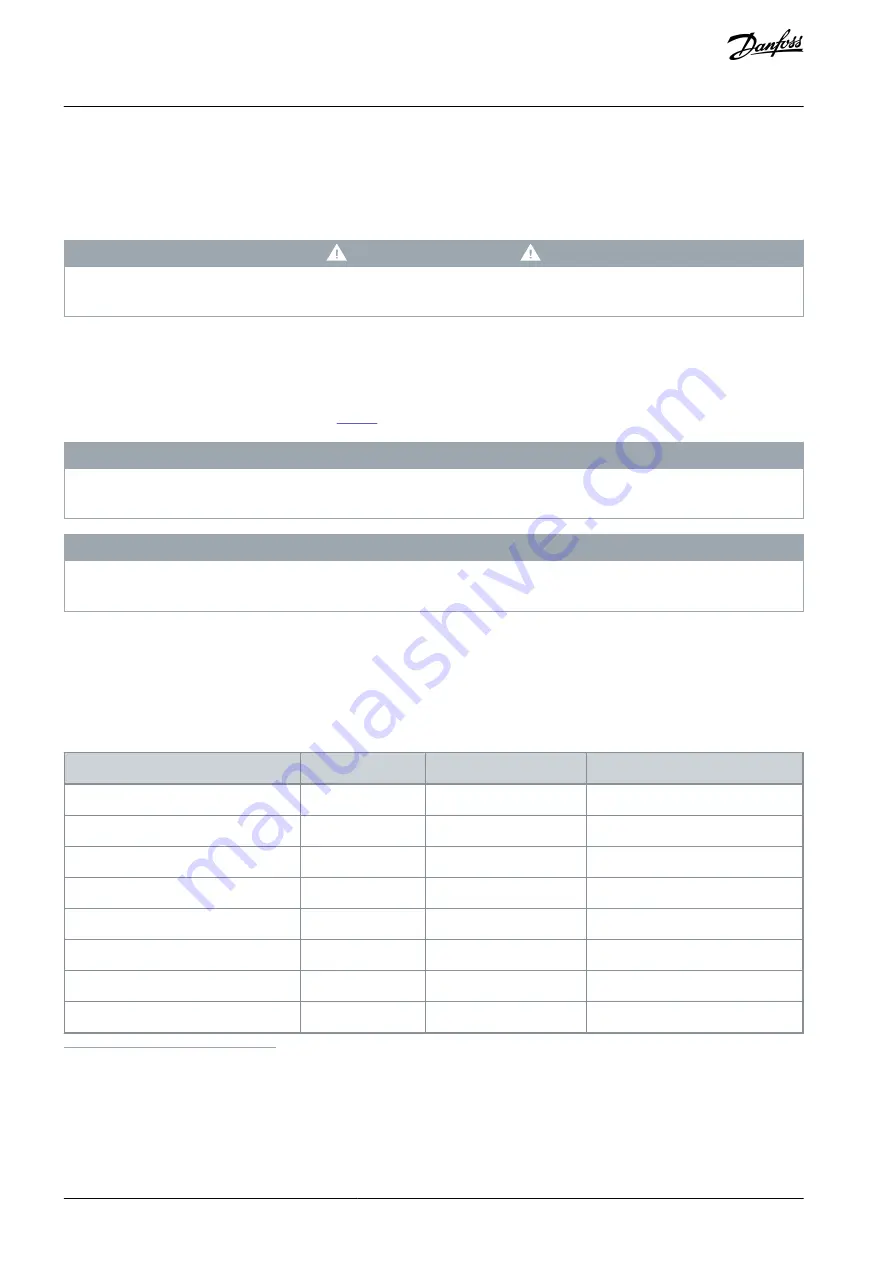
•
•
6.2.7 Warning 71, PTC 1 Safe Stop
STO has been activated from VLT
®
PTC Thermistor Card MCB 112 (motor too warm). Normal operation can be resumed when:
The MCB 112 applies 24 V DC to terminal 37 again (when the motor temperature reaches an acceptable level), and
The digital input from the MCB 112 is deactivated.
W A R N I N G
AUTOMATIC RESTART
When the conditions of the PTC circuit and/or emergency stop circuit have returned to normal, the motor restarts automatically.
6.2.8 Alarm 72, Dangerous Failure
STO with trip lock. If the combination of STO commands is unexpected, the dangerous failure-alarm is issued. This situation occurs if
the VLT
®
PTC Thermistor Card MCB 112 enables X44/10 without STO being enabled. Furthermore, if the MCB 112 is the only device
using STO (specified in
[4] PTC 1 alarm
or
[5] PTC 1 warning
in
parameter 5-19 Terminal 37 Safe Stop
), an unexpected combination
activates the STO without activating the X44/10.
summarizes the unexpected combinations that trigger this alarm.
N O T I C E
If X44/10 is activated in
[2] Safe stop alarm
or
[3] Safe stop warning
, this signal is ignored. However, the MCB 112 is still able to
activate STO.
N O T I C E
For correct and safe use of the STO function, follow the related information and instructions in the VLT
®
Frequency Converter -
Safe Torque Off Operating Guide.
Example
[5] PTC 1 Warning
is selected in
parameter 5-19 Terminal 37 Safe Stop
, and X44/10 is not activated, but STO is. This is an unexpected
selection.
[5] PTC 1 Warning
in
parameter 5-19 Terminal 37 Safe Stop
specifies that STO is only triggered from MCB 112.
6.2.9 Unexpected Combinations
Table 7: Unexpected Combinations Triggering Alarm 72 Dangerous Failure
Function
Number
X44/10 (DI)
STO terminal 37
PTC 1 Alarm
[4]
+
(1)
-
(2)
-
+
PTC 1 Warning
[5]
+
-
-
+
PTC 1 & Relay A
[6]
+
-
PTC 1 & Relay W
[7]
+
-
PTC 1 & Relay A/W
[8]
+
-
PTC 1 & Relay W/A
[9]
+
-
1
+ = Activated
2
- = Not activated
AQ267038105120en-000101 / 130R0104
28 | Danfoss A/S © 2022.08
Maintenance and Troubleshooting
VLT® PTC Thermistor Card MCB 112
Operating Guide
Summary of Contents for VLT PTC Thermistor Card MCB 112
Page 2: ......