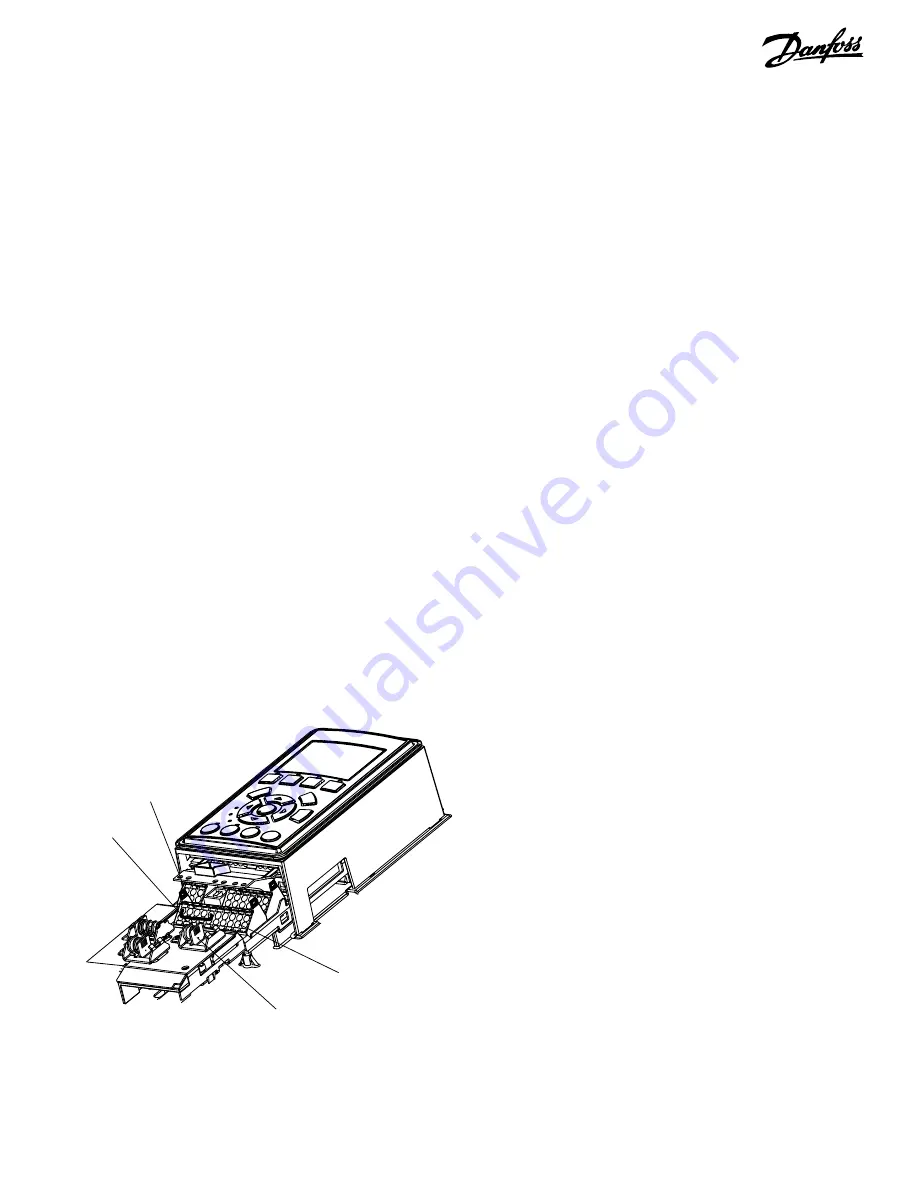
21
Control Wiring
•
It is recommended that control wiring is rated
for 600 V for 480 V and 600 V drives and 300
V for 200-240 V drives.
•
Isolate control wiring from high power
components in the drive.
•
See label inside of panel cover for details.
NOTE
R
UN INPUT POWER
,
MOTOR WIRING AND CONTROL WIRING IN THREE
SEPARATE METALLIC CONDUITS OR RACEWAYS FOR HIGH FREQUENCY
NOISE ISOLATION
. F
AILURE TO ISOLATE POWER
,
MOTOR AND
CONTROL WIRING COULD RESULT IN LESS THAN OPTIMUM DRIVE
AND ASSOCIATED EQUIPMENT PERFORMANCE
.
Figure 3-10. Control Terminals Location
Detailed instructions for terminal functions, control
wiring installation, and operation is shown in Section
5
Electromechanical Bypass (EMB) Operation
and
Section 6
Electronically Controlled Bypass (ECB)
Operation.
Jumper
wire
Control terminals
Electrical Installation
Serial Communication Bus Connection
The ECB reports serial communication data to host
systems through the drive. Connection to the serial
communication network is made either through the
EIA-485 terminals on the drive (Figure 3-10) or, for
other protocols, terminals located on the
communication option card. For option card
connection, see the option card instructions
provided with the unit.
•
For ECB serial communication protocols using
the EIA-485 terminals, make connections in the
following manner.
NOTE
I
T IS RECOMMENDED TO USE BRAIDED
-
SHIELDED
,
TWISTED
-
PAIR
CABLES TO REDUCE NOISE BETWEEN CONDUCTORS
.
1. Connect signal wires to terminal (+) 68 and
terminal (-) 69 on control terminals of drive.
(See the drive support materials for wire size
and tightening torque.)
2. Terminate shield to grounded restraining clip
provided by stripping wire insulation at point
of contact.
3. If shielded cabling is used, do not connect
end of shield to terminal 61.
Programming
Serial communication point maps, parameter
settings, and other details for bypass option
functionality are included in the serial
communication materials supplied with the unit.
EIA-485 terminal
Grounded restraining clips