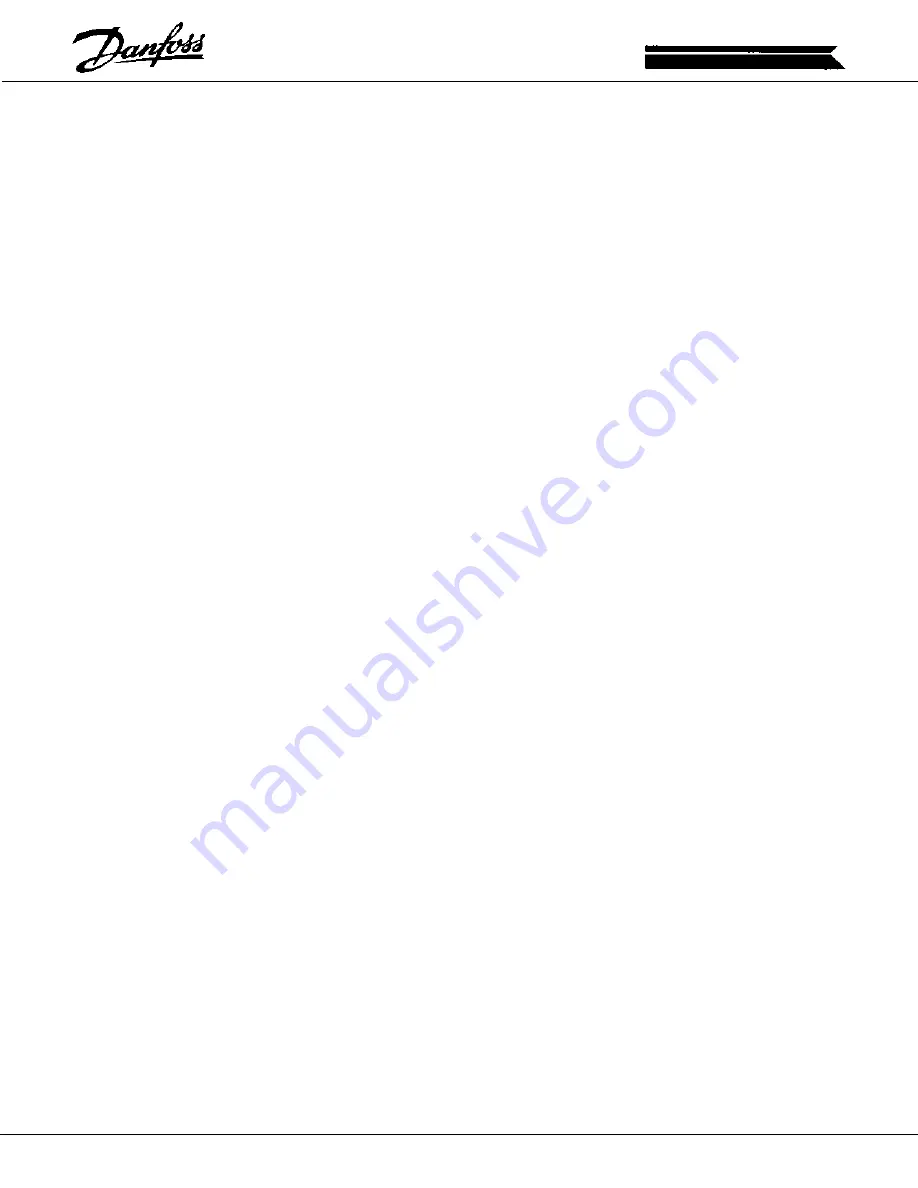
6
LOGIC SECTION
(continued)
A 10VDC supply is also available for use as a speed reference when
connected to an appropriate potentiometer. These two voltage
references are limited in the amount of available current they can provide
(see specifications in Instruction Manual). Attempting to power devices
which draw currents in excess of that available may result in an eventual
failure of the power supply. In addition, if the supply is loaded too
heavily, sufficient voltage will not be available to activate the control
inputs.
During the troubleshooting process it is important to remember that the
control card can only carry out instructions as it has been commanded.
Of course, it is possible that as a result of a failure the control card may
fail to respond to commands. For this reason lies the necessity to
isolate the fault to the control commands, the control program or the
control card itself. If, for example, the unit does not run, but yet an
obvious reason is not apparent, check for proper control signals. Has
a run command been provided on the correct terminal; and if so, has
that terminal been designated as such in the programming of the control
card. In addition, be sure to verify that commands are being received
by testing for the presence of voltage on the appropriate terminals.
Never assume the signal is present because it is suppose to be. If
ever in doubt of whether the remote controls are functioning properly, it
is possible to take local control of the unit to verify if the control card is
operational. A word of caution here: prior to taking local control, insure
all other equipment associated with the drive is prepared to operate.
In many cases, safety interlocks are installed which can only be activated
through the use of a normal remote control start. In the same sense
that the control card can only respond to commands, comes the situation
that the control card makes a response without the presence of an
actual command. By the term response, it is not meant to infer that the
control card initiates such actions as Run or Stop, but rather suggests
that the control card displays unknown data or its performance is affected
as in what might be speed instability. In these cases, the first instinct
may be to replace the control card; however, in most instances, this
type of erroneous operation is usually due to electrical noise being
injected onto the remote control signal wiring. Although the control
card has been designed to reject such interference, noise levels of
sufficient amplitude can, in fact, affect the performance of the control
card.
As mentioned, sufficient levels of electrical noise can cause such things
as speed fluctuations as a result of interference with the speed reference
or with the operation of the microprocessor. In these situations it is
necessary to investigate the wiring practices of the installation. For
example, are the control signal wires running in parallel with other higher
voltage signals such as the input or output power wiring? As wires are
passed in close proximity to one another, voltages are induced through
capacitive or inductive coupling. This type of problem can be corrected
by rerouting the wiring or through the use of shielded cable. When
employing the use of shielded cable, it is important to properly terminate
the drain wire. The drain wire is terminated only at the control card end
of the wire. Specific terminals are designated for this purpose. The
opposite end of the shielded cable drain wire is then cut back and
taped off to prevent it from coming in contact with ground or acting as
an antenna.