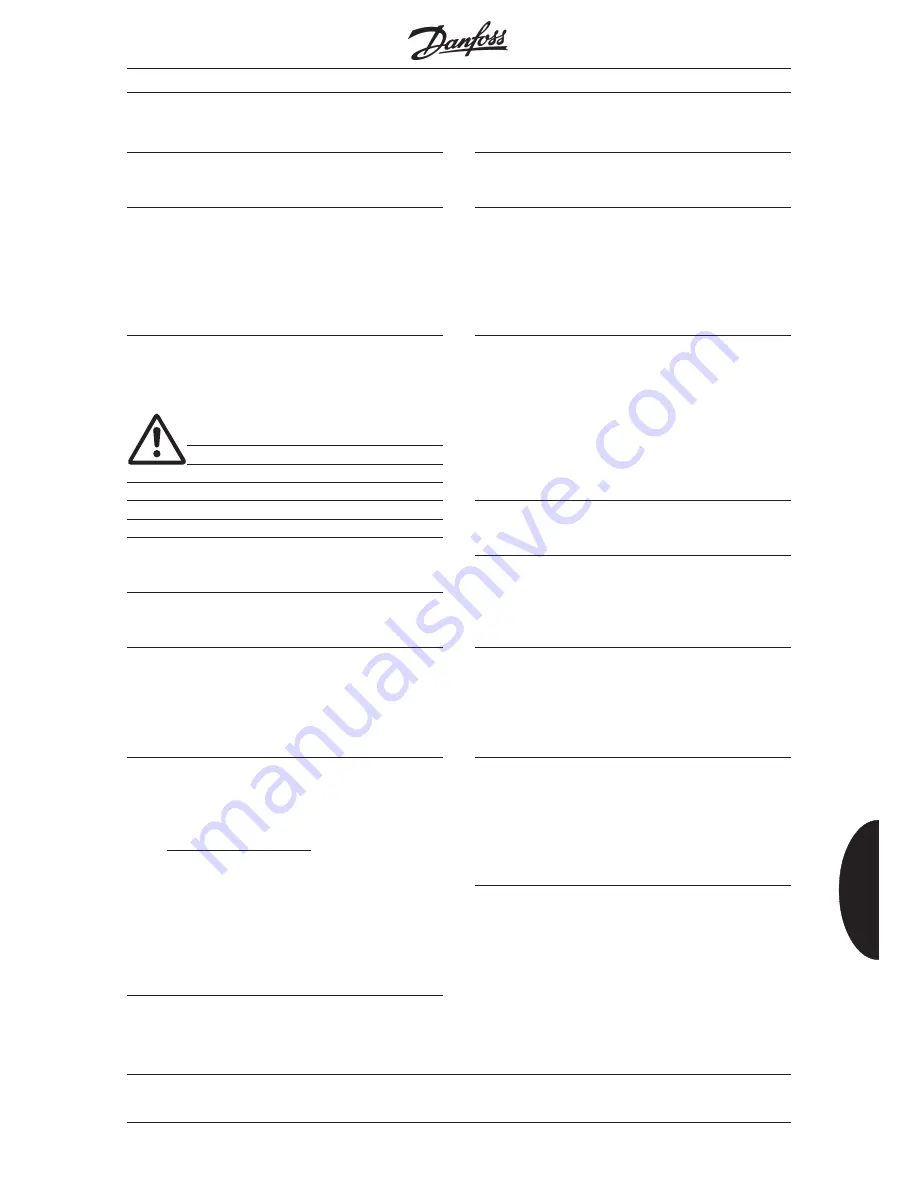
MG.20.B6.02 – VLT is a registered Danfoss trademark
65
VLT
®
2000 Series
Section 1
Section 2
Section 3
110 Start compensation
(START COMP.)
Value: (automatically set)
0.00 - 99 V/A
Function:
Using this parameter you can make a load-dependent
torque adaptation. This is for example used for mo-
tors and applications where there is a large difference
between the motor’s full-load current (parameter 107)
and no-load current (parameter 108).
Description:
If the factory setting is not sufficient, you can set the
parameter so that the motor can start at the actual
load. You can also combine start compensation with
parameter 109.
Warning: Should not be used with
synchronous motors and parallel-coupled
motors and where quick load changes may occur.
To avoid instability do not increase the value more than
necessary.
111 U/f ratio
(V/F. RATIO)
Value: (automatically set)
0.00 - 20 V/Hz
Function:
Using this parameter you can change the linear ratio
between voltage (U) and frequency (f) to ensure
correct motor magnetisation, optimal dynamics,
accuracy or efficiency,
Description:
Use the parameter only if you cannot record the
correct motor data in parameters 104 and 105.
The value can be calculated as follows:
U/f =
Motor voltage (para. 104)
Motor frequency (para. 105)
The value of the factory setting is based on no-load
operation. Therefore it is lower than the value
calculated.
The compensation will give the necessary voltage
supplement.
112 Slip compensation
(SLIP COMP)
Value: (automatically set)
0.0 - 20Hz
Function:
Slip compensation
increases the output frequency
and voltage of the VLT frequency converter with an
increasing load to compensate for the motor’s
increasing slip (loss). This achieves a load-
independent speed.
Description:
Choose a value so that the speed remains constant
when the load increases. If the value is too high the
speed increases with the load. This may lead to
unstable motor operation.
When you use synchronous motors and motors
connected in parallel, set slip compensation to 0 Hz.
Slip compensation should be avoided in case of high
dynamics.
114 Feedback type
(FEEDBACK TYPE)
Value:
Voltage (VOLTAGE 10 V)
[0]
✭
Current (CURRENT 20 mA)
[1]
Pulses (PULSES)
[2]
Function:
Using this parameter you can choose the process
feedback type when you use a PI controller (must
be selected). See also the decription of parameter
101 and the section on the PI controller, page 53.
Description:
When using the PI controller, you must use one of the
inputs of terminal 29, 53 or 60 for the feedback sig-
nal. Parameters 405, 412 and 413 must be set
according to the feedback signal selected. Naturally
these choices block the same type of reference sig-
nal.
✭
= Factory setting. Text in ( ) = Display text. The figures in [ ] are used in bus communication.
Description of parameters
■
■
■
■