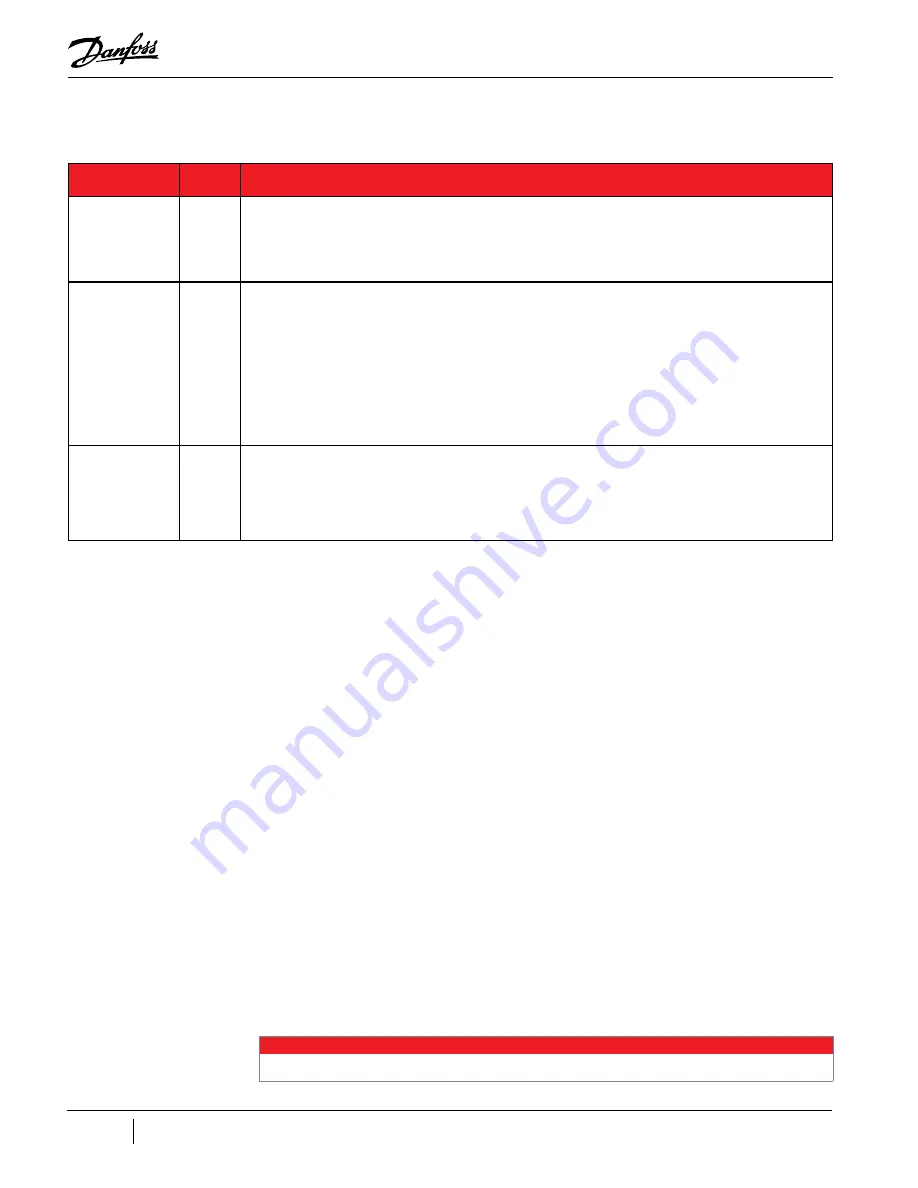
250 of 282
M-SV-001-EN Rev. G
5.2.3 Bearing Status
Table 5-9 Bearing Status
Bearing Fault
Description
Trigger
Method
Troubleshooting
Startup Calibration
Check Fault
INS
• During compressor start-up, the stored bearing calibration is verified. Indicates that the calibration failed during
compressor start-up. Manually calibrate the bearings and save to EEPROM, cycle the power.
• Review the calibration report to determine conditions related to the fault.
• If the bearings cannot pass calibration after three attempts, verify the PWM (refer to "4.29.3 PWM Verification"
on page 220), bearing sensors (refer to "4.31.3 Bearing Sensor Verification" on page 229) and bearings (refer to
"4.30.3 Bearing Verification" on page 223).
Bearing
Displacement
Fault
INS
• The shaft position has been measured outside the bearing displacement maximum in one of the five bearing
positions.
• This fault can be the result of system-related issues, such as EXV control issues (i.e., starving the evaporator or
pumping liquid), operating at the surge line, check valve failure, or IGV failure.
• Review
Fault and Event Log
details to determine conditions related to the fault. Using the
Compressor Configuration
tool
, set the Control Mode to Manual. Using the
Compressor Monitor
, levitate the shaft and record the bearing
forces. Greater than 2A indicates a bearing issue.
• Manually calibrate the bearings, save to EEPROM and identify if bearing forces improve.
• If the bearings cannot be calibrated after three attempts, verify the PWM (refer to "4.29.3 PWM Verification" on
page 220), bearing sensors (refer to "4.31.3 Bearing Sensor Verification" on page 229) and bearings (refer to
"4.30.3 Bearing Verification" on page 223).
• Review the calibration report to determine conditions related to the fault.
Bearing
Overcurrent
Fault
INS
• Indicates that the current drawn by the bearing exceeds the maximum amps in one of the five bearing positions.
Using the
Compressor Configuration
too
l, set the Control Mode to Levitate Only Mode. Using the
Compressor
Monitor
,
levitate the shaft and record the bearing forces.
Greater than 2A indicates an issue.
• Manually calibrate the bearings, save to EEPROM and identify if bearing forces improve.
If the bearings
cannot be calibrated after three attempts, verify the PWM (refer to "4.29.3 PWM Verification" on page 220),
bearing sensors (refer to "4.31.3 Bearing Sensor Verification" on page 229) and bearings (refer to "4.30.3 Bearing
Review the calibration report to determine conditions related to the fault.
5.3 Bearing Calibration
5.3.1 When to Calibrate the Bearings
5.3.1.1 Calibration when Commissioning
A bearing calibration can be performed at commissioning for the purpose of comparing current
calibration values to factory saved calibration values. After the calibration has been performed, a
calibration report should be created and saved for future comparison. There is no requirement to save
the calibration to EEPROM when commissioning the compressor.
5.3.1.2 Regular Maintenance Calibration
Calibration can be performed during regular maintenance visits for the purpose of comparing the
values stored in EEPROM to the latest current calibration values to determine changes over time. There
is no benefit to save the calibration to EEPROM if the compressor has been operating normally.
A calibration report should always be created for future comparison.
5.3.1.3 Calibration when Troubleshooting
Troubleshooting procedures that require a bearing calibration to be performed will need to be saved
to EEPROM. Click on the “Save to EEPROM” button even if a message indicating values are out of range
is displayed. Ensure that “Stored” values are updated to be identical to “Latest” values. Cycle power
to the compressor ensuring the green LED on the I/O board turns off. This may need to be repeated
multiple times. Create a calibration report before any change is made and after each calibration.
Ensure the shaft levitates correctly by clicking “Validate” after calibration values have been saved to
EEPROM.
NOTE
The compressor performs an automatic startup check bearing calibration after a power cycle.
Summary of Contents for Turbocor TTS Series
Page 14: ...14 of 282 M SV 001 EN Rev G THIS PAGE INTENTIONALLY LEFT BLANK...
Page 30: ...30 of 282 M SV 001 EN Rev G THIS PAGE INTENTIONALLY LEFT BLANK...
Page 38: ...38 of 282 M SV 001 EN Rev G THIS PAGE INTENTIONALLY LEFT BLANK...
Page 40: ...40 of 282 M SV 001 EN Rev G THIS PAGE INTENTIONALLY LEFT BLANK...
Page 46: ...46 of 282 M SV 001 EN Rev G THIS PAGE INTENTIONALLY LEFT BLANK...
Page 50: ...50 of 282 M SV 001 EN Rev G THIS PAGE INTENTIONALLY LEFT BLANK...
Page 238: ...238 of 282 M SV 001 EN Rev G THIS PAGE INTENTIONALLY LEFT BLANK...
Page 240: ...240 of 282 M SV 001 EN Rev G THIS PAGE INTENTIONALLY LEFT BLANK...
Page 260: ...260 of 282 M SV 001 EN Rev G THIS PAGE INTENTIONALLY LEFT BLANK...
Page 262: ...262 of 282 M SV 001 EN Rev G THIS PAGE INTENTIONALLY LEFT BLANK...
Page 268: ...268 of 282 M SV 001 EN Rev G THIS PAGE INTENTIONALLY LEFT BLANK...
Page 276: ...276 of 282 M SV 001 EN Rev G THIS PAGE INTENTIONALLY LEFT BLANK...
Page 280: ...280 of 282 M SV 001 EN Rev G THIS PAGE INTENTIONALLY LEFT BLANK...