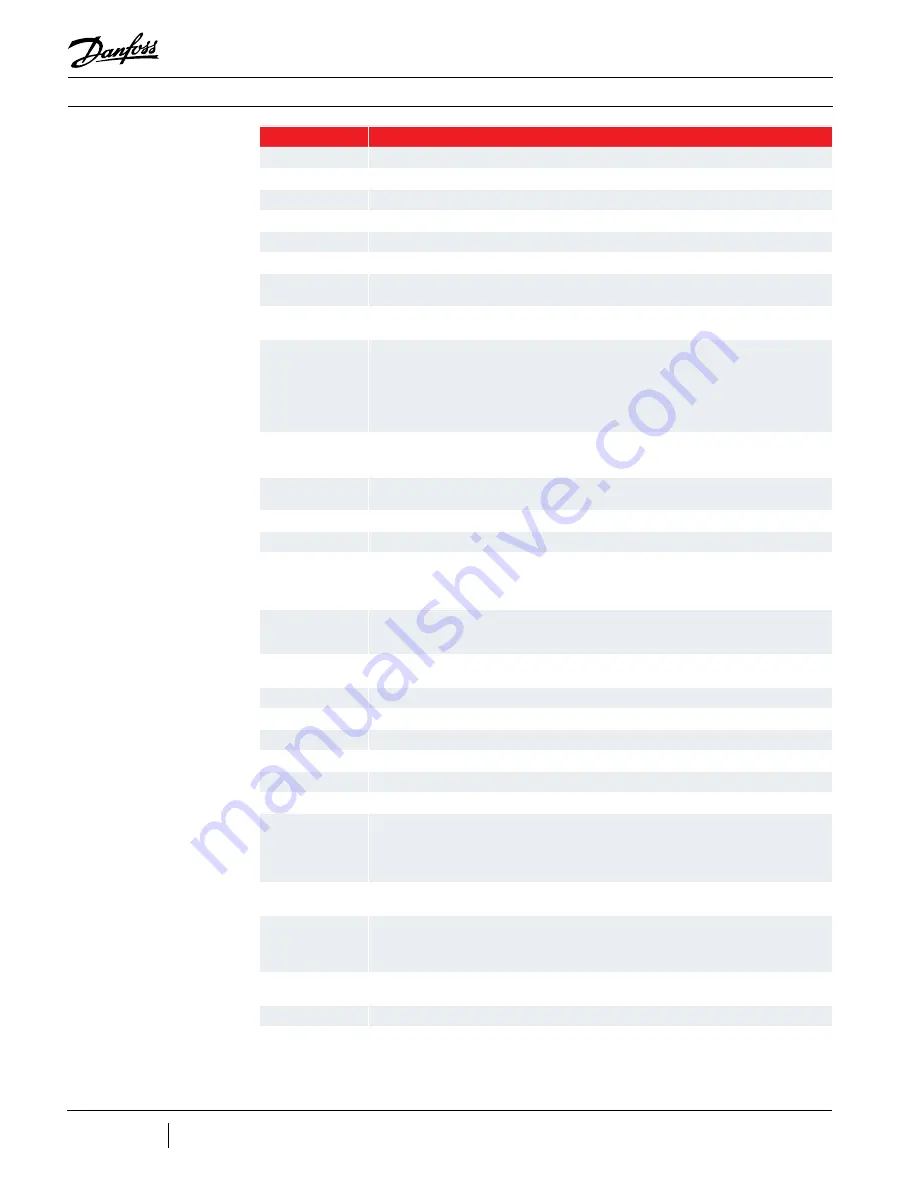
Page
12
of
108
M-AP-001-EN Rev. N
M-AP-001-EN Rev. N
Introduction
Acronym / Term
Definition
EMC
Electromagnetic Compatibility
EMF
Electromotive Force
EMI
Electromagnetic Interference
EMI Filter
A circuit or device that provides electromagnetic noise suppression for an electronic device
EPC
Extended Performance Compressor
ETL
ETL Testing Laboratories, now a mark of Intertek Testing Services
EXV
Electronic Expansion Valve. Pressure-independent refrigerant metering device driven by
electrical input
Event Log
A record of events occurring during the compressor’s lifecycle, indicating when events and
faults occur and in what order. The event log is held in the BMCC.
Faults (Critical)
Critical faults indicate an intolerable or unsafe condition that will result in equipment
failure if unchecked. They will cause the compressor controller to reduce speed and shut
down the system within 60 seconds.
This type of fault requires a manual reset.
Critical faults
include: Discharge Pressure Fault, 3-Phase Over-Current Fault, and Lock Out Fault. If any
of the following faults occur three times within a 30-minute period, they also will require
a manual reset: Inverter Temperature Fault, Cavity Temperature, SCR Temperature Fault,
Motor High Current Fault, and Motor back EMF is low.
Faults (Non-Critical)
Faults indicate an intolerable or unsafe condition that will result in equipment failure if
unchecked. They will cause the compressor controller to reduce speed and shut down the
system within 60 seconds.
This type of fault has an automatic reset.
Feedthrough
An insulated conductor connecting two circuits on opposite sides of a barrier such as a
compressor housing or PCB.
FIE
Fully Integrated Electronics version of the compressor.
FLA
Full Load Amps
Generator Mode
A function of the compressor where the stator becomes a generator, creating sufficient
power to allow for the shaft to graduate slowly and drop onto the touchdown bearings
safely. This occurs when the inverter has insufficient power to sustain safe and normal
operation and is typically due to a loss of power.
Genlanolin
A type of grease. In certain climates where the dew point falls below the operating
temperature of some of the electronic components, it is necessary to apply Genlanolin to
certain parts of the compressor to prevent moisture accumulation.
Harmonics
Harmonics are multiples of the fundamental frequency distortions found in electrical
power, subjected to continuous disturbances.
HFC
Hydrofluorocarbon
HFC-134a
A positive-pressure, chlorine-free refrigerant having zero ozone depletion potential.
Hermetic Motor
A motor that is sealed within the refrigerant atmosphere inside the compressor.
ICD
Integrated compressor Design
IEEE
Institute of Electrical and Electronic Engineers (www.ieee.org)
IGBT
Insulated Gate Bipolar Transistor. See Inverter.
IGV
Inlet Guide Vanes. The IGV assembly is a variable-angle guiding device that pre-rotates
refrigerant flow at the compressor intake and is also used for capacity control. The IGV
assembly consists of movable vanes and a motor. The vane angle, and hence, the degree of
pre-rotation to the refrigerant flow, is determined by the BMCC and controlled by the Serial
Driver. The IGV position can vary between approximately 0-percent and 110-percent open.
Impeller
Rotating part of a centrifugal compressor that increases the pressure of refrigerant vapor
from the lower evaporator pressure to the higher condenser pressure.
I/O Board
Input/Output Board facilitating a connection between the compressor controller and/
or PC and the compressor. It allows the user to control the compressor and allows the
compressor to return status and sensor information to the user. Also known as the
Compressor Interface Module (CIM).
Inverter
The Inverter converts the DC bus voltage into an adjustable frequency and adjustable
amplitude, three-phase simulated AC voltage.
IPLV
Integrated Part Load Value
LBV
Load Balance Valve. A modulating valve that can be installed to bypass discharge gas to the
inlet of the evaporator to provide gas flow at certain conditions such as startup, surge, and
further unloading of the compressor.
Summary of Contents for Turbocor TT Series
Page 2: ...Page 2 of 108 M AP 001 EN Rev N THIS PAGE INTENTIONALLY LEFT BLANK...
Page 8: ...Page 8 of 108 M AP 001 EN Rev N THIS PAGE INTENTIONALLY LEFT BLANK...
Page 18: ...Page 18 of 108 M AP 001 EN Rev N THIS PAGE INTENTIONALLY LEFT BLANK...
Page 32: ...Page 32 of 108 M AP 001 EN Rev N THIS PAGE INTENTIONALLY LEFT BLANK...
Page 36: ...Page 36 of 108 M AP 001 EN Rev N THIS PAGE INTENTIONALLY LEFT BLANK...
Page 44: ...Page 44 of 108 M AP 001 EN Rev N THIS PAGE INTENTIONALLY LEFT BLANK...
Page 50: ...Page 50 of 108 M AP 001 EN Rev N THIS PAGE INTENTIONALLY LEFT BLANK...
Page 52: ...Page 52 of 108 M AP 001 EN Rev N THIS PAGE INTENTIONALLY LEFT BLANK...
Page 54: ...Page 54 of 108 M AP 001 EN Rev N THIS PAGE INTENTIONALLY LEFT BLANK...
Page 56: ...Page 56 of 108 M AP 001 EN Rev N THIS PAGE INTENTIONALLY LEFT BLANK...
Page 58: ...Page 58 of 108 M AP 001 EN Rev N THIS PAGE INTENTIONALLY LEFT BLANK...
Page 70: ...Page 70 of 108 M AP 001 EN Rev N THIS PAGE INTENTIONALLY LEFT BLANK...
Page 74: ...Page 74 of 108 M AP 001 EN Rev N THIS PAGE INTENTIONALLY LEFT BLANK...
Page 82: ...Page 82 of 108 M AP 001 EN Rev N Physical Data Figure 16 9 Suction Port All Models...
Page 88: ...Page 88 of 108 M AP 001 EN Rev N THIS PAGE INTENTIONALLY LEFT BLANK...
Page 90: ...Page 90 of 108 M AP 001 EN Rev N THIS PAGE INTENTIONALLY LEFT BLANK...
Page 92: ...Page 92 of 108 M AP 001 EN Rev N THIS PAGE INTENTIONALLY LEFT BLANK...