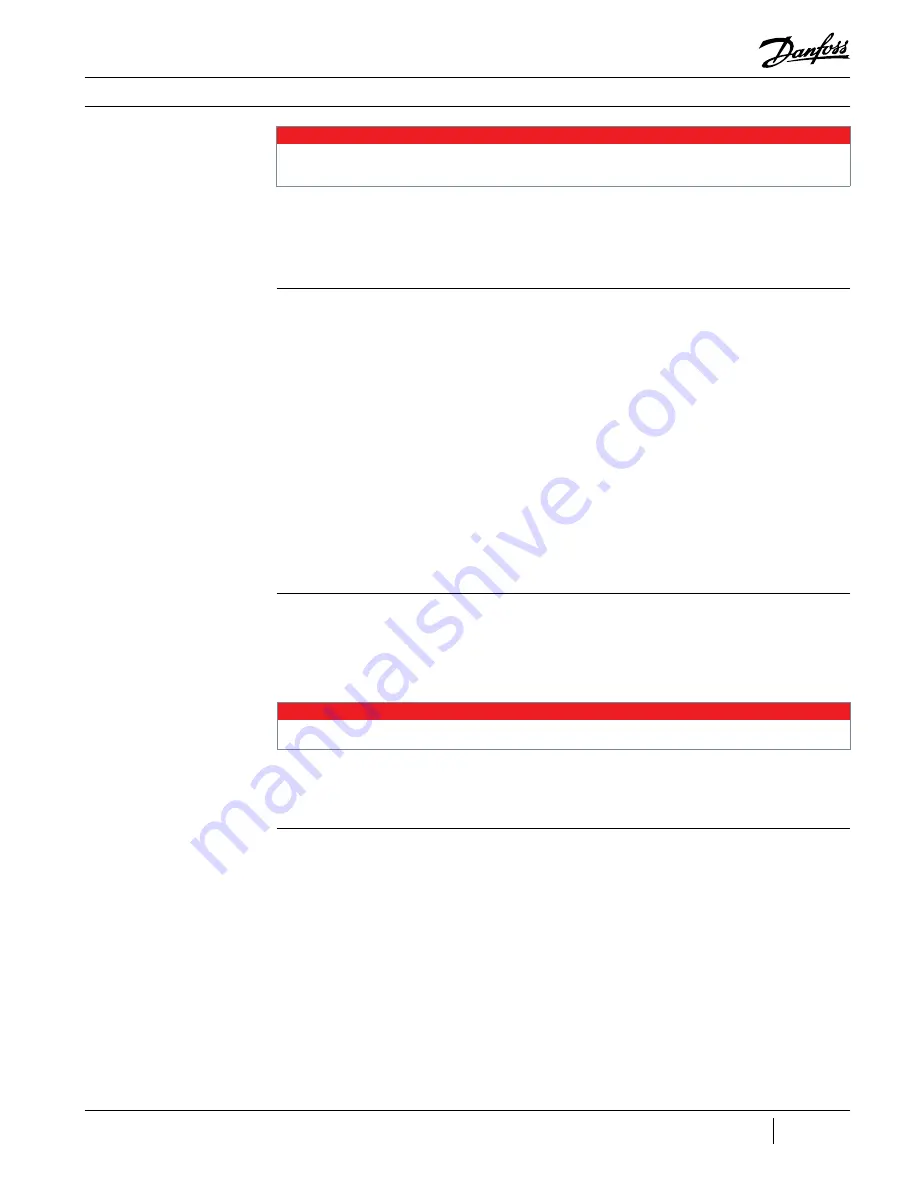
81 of 132
M-SV-001-EN Rev.E
Compressor Components
3.16.3 Verification
3.16.3.1 Verify if the
Bearing PWM Amplifier is
Draining Energy
3.16.3.2 Verify
Functionality Of The Five
Output Channels
3.16.3.3 Verify
Functionality Of The Five
Diode Sets
Several verification methods are available for the
PWM:
• Verify if the PWM is draining energy.
• Verify functionality of the five output channels.
• Verify functionality of the five diode sets.
1. Remove the Service Side Cover.
2. Disable compressor operation while keeping
the compressor energized.
3. Measure the voltage at the HV+, +17HV, and
+5V test points on the Backplane.
4. Isolate compressor power; wait for the LEDs on
the Backplane to completely turn off.
5. Disconnect the rear/axial bearing current
output cable and the front bearing current
output cable
6. Apply power to the compressor.
7. Measure and record the voltage at the HV+,
+17HV, and +5V test points.
8. Isolate compressor power; wait for the LEDs on
the Backplane to completely turn off.
9. Remove the PWM from the Backplane.
10. Apply power to the compressor.
11. Measure and record the voltage at the HV+,
+17HV, and +5V test points.
12. If the voltages do not change, the PWM is
not the source (or not the only source) of energy
drain.
1. Measure the voltage at the HV+, +17HV, and
+5V test points on the Backplane.
2. Verify the bearing coil resistances are within
specification.
3. Verify the bearing sensor resistances are within
specification.
4. Perform a bearing calibration using the SMT.
To verify the diode sets within the PWM channels,
complete the following steps:
1. Isolate compressor power.
2. Remove the Service Side Cover verifying the
LEDs on the Backplane have turned off.
3. Unplug the 250VDC input (J4) from the
Backplane. See Figure 66 (Bearing Power Feed
Throughs and PWM Connection Port).
4. Disconnect the PWM connectors from the
compressor housing bearing feed throughs,
keeping the PWM attached to the Backplane.
5. Using a multimeter set for diode
measurements, place the red (+) lead on the HV-
test point of the Backplane and the black (-) lead
in the first pin hole of the PWM connector, ensure
the lead makes contact with the clip in the pin
hole. See Figure 77 (Connecting Leads to PWM
Connector and HV- Test Point). The measured
voltage drop should be 0.39-0.46VDC.
5. If all bearing resistances are good and one or
more of the gains is/are 0, but not all the gains
are 0, the PWM is faulty.
NOTE
A faulty PWM Amplifier may be the result of a bearing failure and may cause a failure of the DC/DC resulting in a blown F1 fuse on
the Soft Start.
If a PWM Amplifier is found to be faulty, the bearing actuator coils, DC/DC and F1 Fuse must also be verified.
NOTE
If one of the PWM output channels has failed, the corresponding bearing channel returns a gain of 0 when a bearing calibration is
performed.
Summary of Contents for Turbocor TT-300
Page 2: ...THIS PAGE INTENTIONALLY LEFT BLANK...
Page 4: ...4 of 132 M SV 001 EN Rev E THIS PAGE INTENTIONALLY LEFT BLANK...
Page 12: ...12 of 132 M SV 001 EN Rev E THIS PAGE INTENTIONALLY LEFT BLANK...
Page 61: ...61 of 132 M SV 001 EN Rev E Compressor Components Figure 56 Stator Thermistor R T Curve 1...
Page 120: ...120 of 132 M SV 001 EN Rev E THIS PAGE INTENTIONALLY LEFT BLANK...
Page 130: ...130 of 132 M SV 001 EN Rev E Notes...