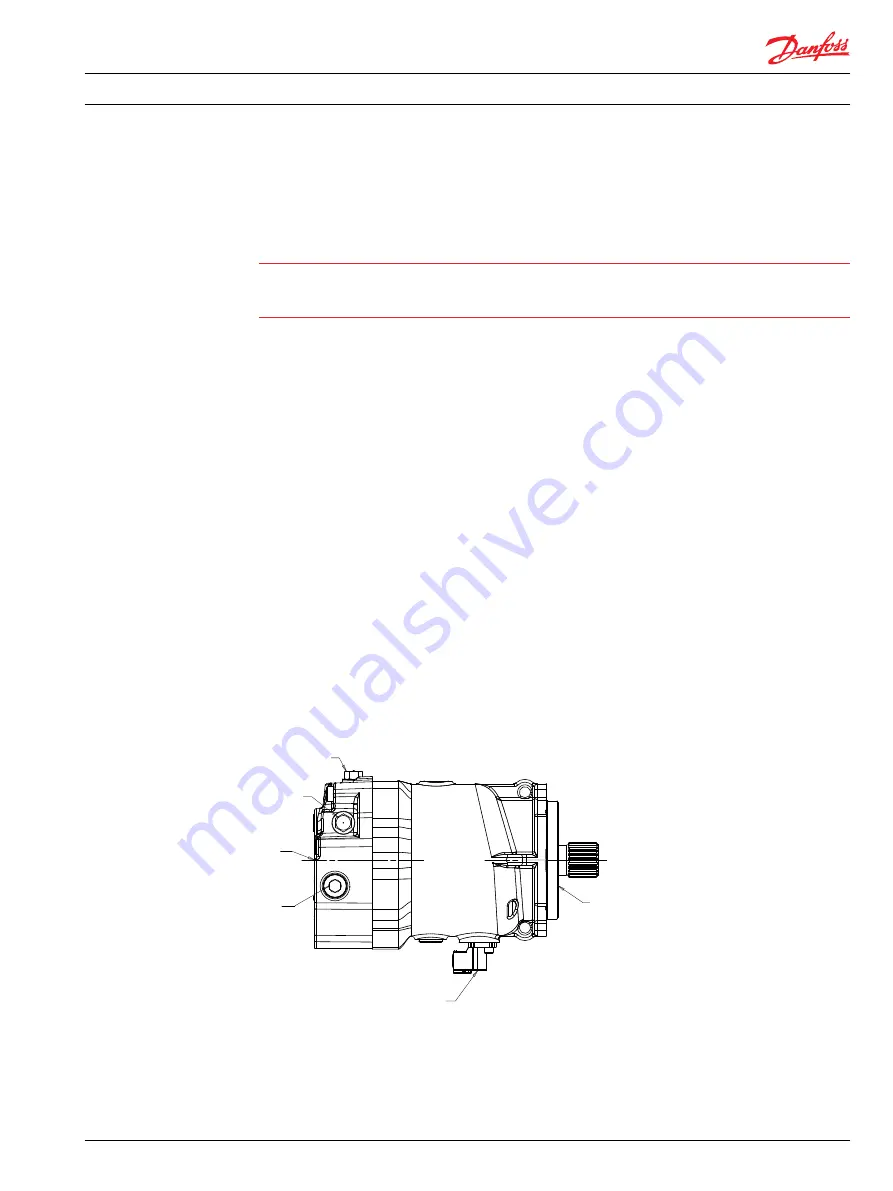
Standard procedures, removing the motor
Before working on the motor, thoroughly clean the outside. Tag and cap all hydraulic lines as they are
disconnected, and plug all open ports to ensure that dirt and contamination do not get into the system.
C
Caution
Contamination can damage internal components and void your warranty.
Take precautions to ensure system cleanliness when removing and reinstalling system lines.
Disassembly
1. With the prime mover off, thoroughly clean all dirt and grime from the outside of the motor.
2. Tag, disconnect, and cap each hydraulic line connected to the motor. As hydraulic lines are
disconnected, plug each open port, to ensure that dirt and contamination do not get into the motor.
Inspection
1. Ensure the work surface is clean and free of contaminants such as dirt and grime.
2. Inspect the system for contamination.
3. Look at the hydraulic fluid for signs of system contamination, oil discoloration, foam in the oil, sludge,
or metal particles.
Reassembly
1. Before replacing the motor, replace all filters and drain the hydraulic system. Flush the system lines
and fill the reservoir with the correct, filtered hydraulic fluid.
2. Attach the motor to the flange. Torque mounting screws according to the manufacturers
recommendation.
3. Fill the motor with clean, filtered hydraulic fluid.
4. Ensure the charge inlet line is filled with fluid.
Motor outline for minor repair reference
C
D
F
A
B
E
A – Loop flushing relief valve
B – Loop flushing valve
D – High pressure relief valve
E – Speed sensor
Service Manual
TMM Transit Mixer Axial Piston Motor, Size 070/084/089
Minor Repair
L1211037 • Rev AC • Apr 2014
23