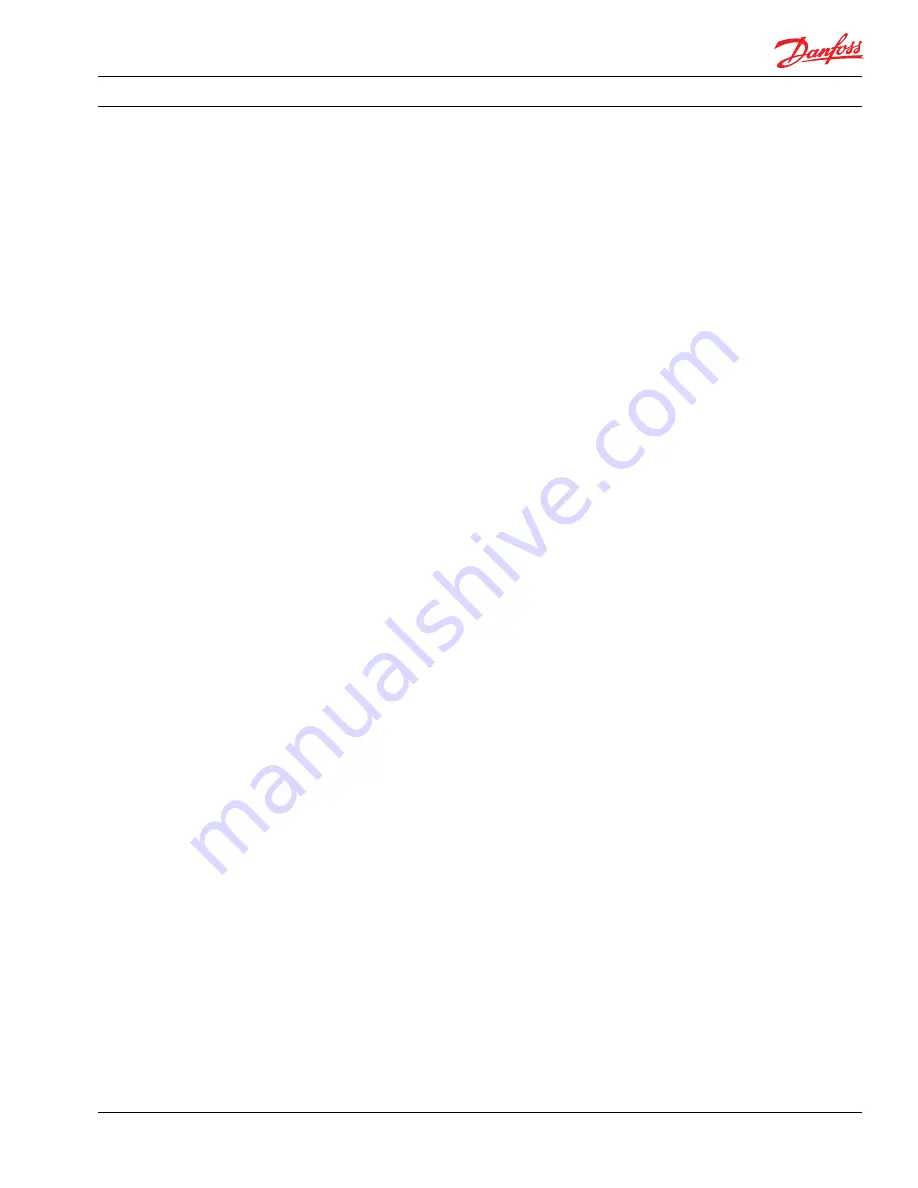
Service Manual and
Axial Piston Motors Series 20
Repair Instructions
L1003443
• Rev BA • Jun 2014
7
Start-up procedure
Preconditions for Trouble-
free Operation
Cleanliness
Ensure that the pipes, pipe connections and hoses as well as all other components are completely
clean.
Ventilation and venting of the oil reservoir
via an air filter.
Operating fluid
HLP fluid according to DIN 51524, ATF type A SUFFIX A, HD-SAE motor oils, see
Fluid Manufacturers,
Technical Information.
Oil level:
(The inlet pipe and return flow port must always be below the surface of the oil). No
funnel-shaped eddying at the inlet connection pipe. No formation of foam at the return flow pipe.
The inlet connection pipe must be substantially above the bottom of the reservoir. A partition plate
should be located between the inlet and return flow connection pipes.
Filtration
Filtration grade = 10
µ
m [394
µ
inch] nominal.
Inlet pressure of charge pump:
0.85 bar [12.3 psi] absolute (- 0.15 bar [-2.2 psi]) with a new filter
element and at an operating temperature of approx. 50 °C [122 °F].
A charge pump inlet pressure less than 0.75 bar [10.9 psi] absolute (-0.25 bar [-3.6 psi]) is permissible
for a short time with a reservoir temperature of less than 50 °C [122 °F] on a cold start in order to warm
up the system under no-load.
If frequent cold starts are to be made, the system should be warmed up by a reservoir heater.
If the charge pump inlet pressure is less than 0.75 bar [10.9 psi] absolute (-0.25 bar [-3.6 psi]) on
operating temperatures higher than 50 °C [122 °F],
the filters must be changed
.
A charge pump inlet pressure of less than 0.5 bar [7.3 psi] absolute (- 0.5 bar [-7.3 psi]) is not
permissible.
The filter requires changing or the operating temperature is too low.
Venting
the pump and motor housing as well as the connection lines and other components.
The return flow to the oil reservoir must be free of bubbles. After venting the system, check the fluid
level and fill to proper level if necessary.
Carry out a leak test
on the transmission (inlet line, filter, pipe and hose lines, valves, control
elements, pump and motor) giving due consideration to the service life of the transmission,
environmental protection and the reduction of oil consumption.
Tighten up any leaking joints and other connections while the system is not under pressure.
Pressure fluid temperature range:
min. = -40 °C [-40 °F], max. = 95 °C [203 °F].
Viscosity range:
max. = 1000 mm
2
/s [4630 SUS*] (cSt) (for a short time only on a cold start).
min. = 7 mm
2
/s [49 SUS*] (cSt).
Recommended viscosity range: 12-60 mm
2
/s [66-278 SUS*] (cSt).
*SUS (Saybolt Universal Second)
Changing the oil:
The oil should be changed after max. 80-100 hours of operation, but at the latest
one year after first-time operation.
The second oil change should be after max. 500 hours of operation but at the latest one year after the
first change of fluid.
Thereafter, the oil should be changed every 1000 hours of operation but at least once a year. It is not
permissible to mix oil.
Renew the inlet filter
each time the oil is changed or when the inlet pressure of the charge pump
falls below the permissible tolerance.
Clean the air filter
whenever too much dirt has accumulated.
The max. speed
is as specified in the catalogue
L1003621
Series 20 Axial Piston Pumps, Technical
Information or
L1003465
Series 20 Axial Piston Motors, Technical Information
.