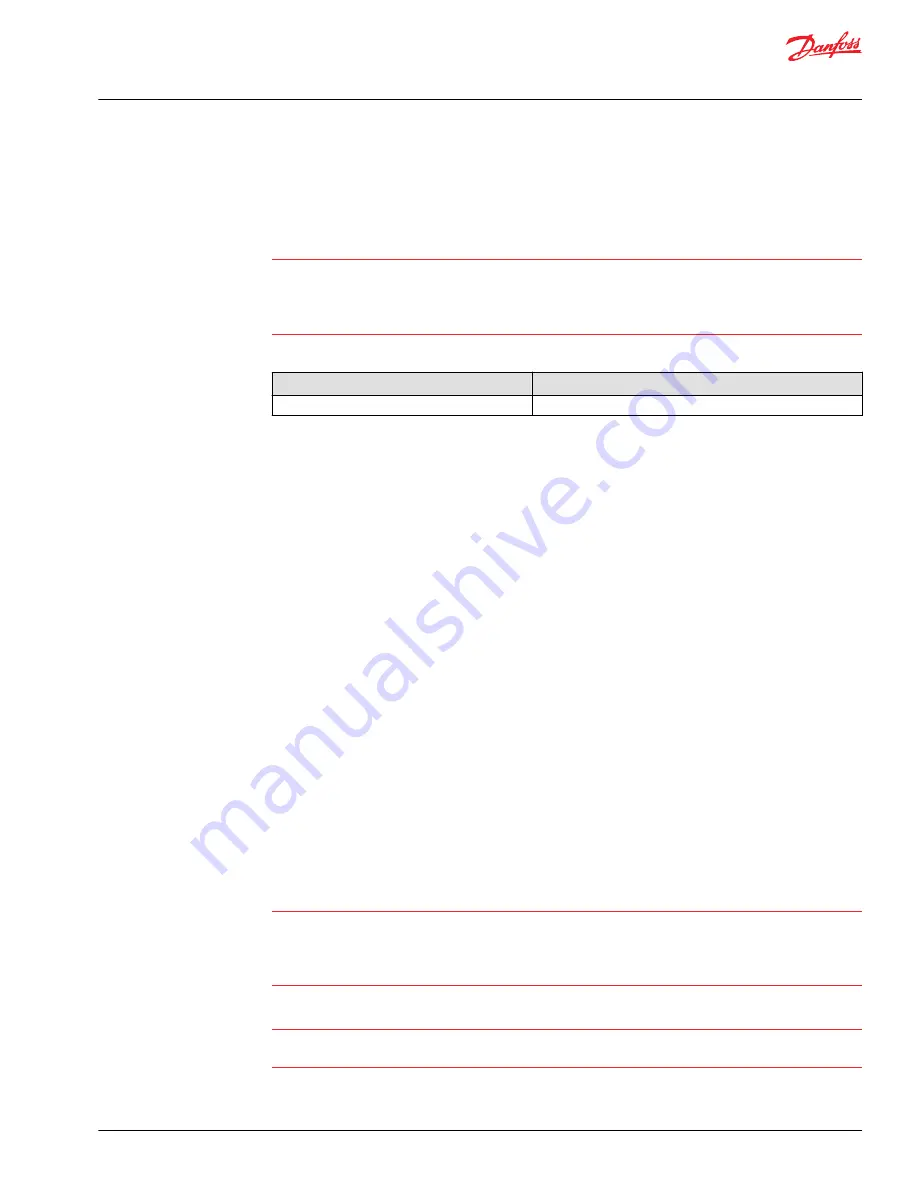
If the module is side or stack mounted, provide a drip loop in the harness. If the module is mounted
vertically, the connector should be on the bottom of the module.
Provide strain relief for mating connector wires.
C
Caution
Module damage may occur.
Use caution when installing modules. Due to the size of the mating connector wire bundle, it is possible
to twist off the end cap of the module if excessive pressure is applied during the installation of harness
strain relief.
Fasteners
Recommended outer diameter (OD)
Recommended torque
6.0 mm (0.25 in)
2.26 N•m (20 in•lbs)
Machine diagnostic connector
It is recommended that a diagnostic connector be installed on machines that are controlled by PLUS+1
®
modules. The connector should be located in the operator's cabin or in the area where machine
operations are controlled and should be easily accessible.
Communication (software uploads and downloads and service and diagnostic tool interaction) between
PLUS+1
®
modules and personal computers is accomplished over the vehicle CAN network. The diagnostic
connector should tee into the vehicle CAN bus and have the following elements:
•
CAN +
•
CAN -
•
CAN shield
Grounding
Proper operation of any electronic control system requires that all control modules including displays,
microcontrollers and expansion modules be connected to a common ground. A dedicated ground wire
of appropriate size connected to the machine battery is recommended.
Hot plugging
Machine power should be off when connecting PLUS+1
®
modules to mating connectors.
Machine wiring guidelines
W
Warning
Unintended movement of the machine or mechanism may cause injury to the technician or bystanders.
Improperly protected power input lines against over current conditions may cause damage to the
hardware. Properly protect all power input lines against over-current conditions. To protect against
unintended movement, secure the machine.
C
Caution
Unused pins on mating connectors may cause intermittent product performance or premature failure.
Plug all pins on mating connectors.
Technical Information
PLUS+1® MC0XX-1XX Controller Family
Product installation and start-up
©
Danfoss | April 2018
L1321895 | BC00000227en-US0401 | 25