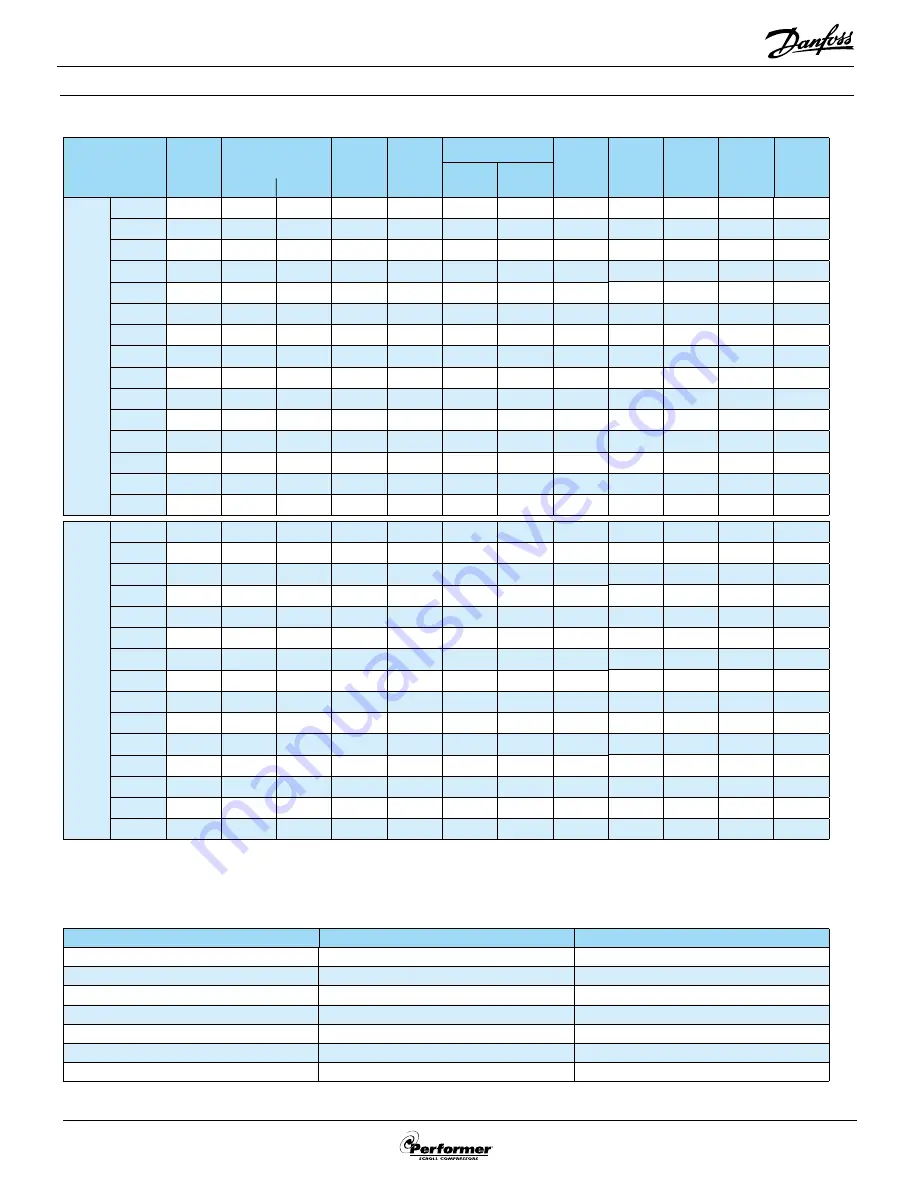
6
Model
Nominal
Cap. 60 Hz
TR
Nominal cooling
capacity**
W
Btu/h
Power
input
kW
A max
(code 4)
A
Efficiency
Sound
power
dB(A)
Swept
volume
cu.in/rev
Displace-
ment
cu.ft/h
Oil
charge
oz
Net
weight
lb*
COP
W/W
E.E.R.
Btu/h /W
R-22
single
sM084
7
20400
69 600
6.12
17
3.33
11.4
70
6.99
703
111.6
159
sM090
7.5
21800
74 400
6.54
17
3.33
11.4
70
7.35
741
111.6
159
sM100
8
23100
79 000
6.96
19
3.33
11.3
70
7.76
782
111.6
159
sM110
9
25900
88 600
7.82
20
3.32
11.3
75
8.80
886
111.6
176
sM115
9.5
28000
95 600
8.31
25
3.37
11.5
76
9.46
952
128.5
176
sM120
10
30100
102 800
8.96
29
3.36
11.5
75
10.17
1024
111.6
176
sM125
10
30100
102 800
8.93
25
3.37
11.5
76
10.17
1024
128.5
176
sM148
12
36100
123 100
10.80
32
3.34
11.4
79
12.14
1222
121.7
176
sM160
13
39100
133 500
11.60
29
3.37
11.5
79.5
13.22
1331
135.3
207
sM161
13
39000
133 200
11.59
32
3.37
11.5
79.5
13.22
1331
121.7
190
sM175
14
42000
143 400
12.46
35
3.37
11.5
80
14.22
1432
209.6
227
sM185
15
45500
155 300
13.62
35
3.34
11.4
80
15.25
1535
209.6
227
sY240
20
61200
208 700
18.20
50
3.36
11.5
82
21.22
2137
270.5
353
sY300
25
78200
267 000
22.83
69
3.43
11.7
82
26.70
2687
270.5
353
sY380
30
92000
313 900
26.82
79
3.43
11.7
85
32.42
3263
284.0
359
tecHnical speciFications
50 Hz data
Subject to modification without prior notification
For full data details and capacity tables refer to Online Datasheet Generator :
www.danfoss.com/odsg
sM/sY compressors
sZ compressors
Refrigerant
R-22
R-407C
Frequency
50 Hz
50 Hz
Standard rating conditions
ARI standard conditions
-
Evaporating temperature
45 °F
45 °F (dew point)
Condensing temperature
130 °F
130 °F (dew point)
Subcooling
15 °F
15 °F
Superheat
20 °F
20 °F
Rating conditions
TR = Ton of Refrigeration
COP = Coefficient Of Performance
EER = Energy Efficiency Ratio
R-407
c
single
sZ084
7
19300
66 000
6.13
17
3.15
10.7
71
6.99
703
111.6
159
sZ090
7.5
20400
69 600
6.45
17
3.16
10.8
72
7.35
741
111.6
159
sZ100
8
21600
73 700
6.84
19
3.15
10.8
73
7.76
782
111.6
159
sZ110
9
24600
84 000
7.76
20
3.17
10.8
77
8.80
886
111.6
176
sZ115
9.5
26900
91 700
8.49
25
3.16
10.8
77
9.46
952
128.5
176
sZ120
10
28600
97 600
8.98
29
3.18
10.9
77
10.17
1024
111.6
176
sZ125
10
28600
97 500
8.95
25
3.19
10.9
78
10.17
1024
128.5
176
sZ148
12
35100
119 800
10.99
32
3.19
10.9
79
12.14
1222
121.7
176
sZ160
13
37600
128 200
11.58
29
3.24
11.1
80.5
13.22
1331
135.3
207
sZ161
13
37900
129 500
11.83
32
3.21
10.9
79
13.22
1331
121.7
190
sZ175
14
40100
136 900
12.67
35
3.17
10.8
81
14.22
1432
209.6
227
sZ185
15
43100
147 100
13.62
35
3.16
10.8
81
15.25
1535
209.6
227
sZ240
20
59100
201 800
18.60
50
3.18
10.9
83.5
21.22
2137
270.5
353
sZ300
25
72800
248 300
22.70
69
3.20
10.9
84
26.70
2687
270.5
353
sZ380
30
89600
305 900
27.60
79
3.25
11.1
86.5
32.42
3263
284.0
359
*
with oil charge & accessories
** at nominal speed
2900 rpm at 50 Hz
3500 rpm at 60Hz
Summary of Contents for Performer SM 084
Page 39: ......