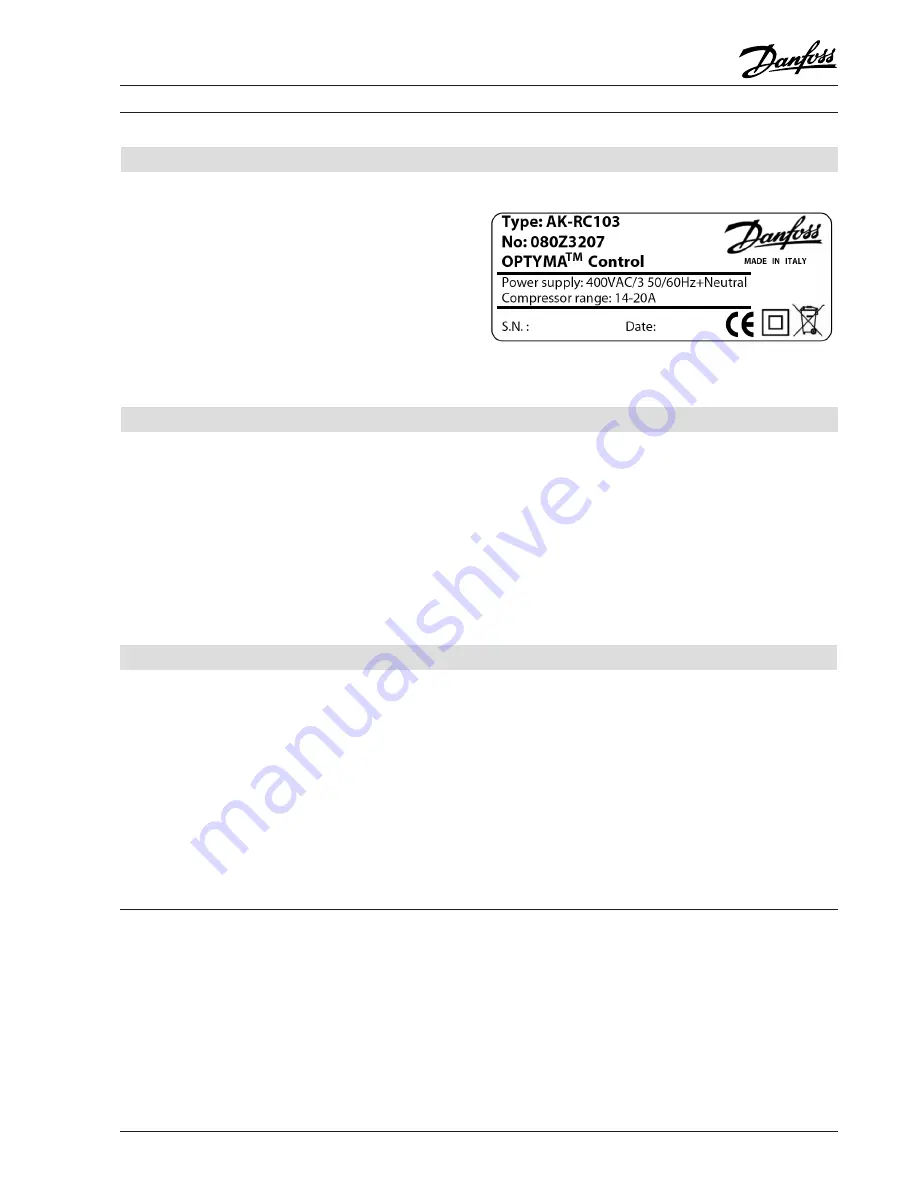
©
Danfoss A/S (RA Marketing/MWA), Nov. 08
RS8FE102, 080R9278
7
OPTYMA
TM
Control three-phase
Operation and Maintenance Guide
The OPTYMA
TM
Control three-phase unit is supplied with:
Standard assembly kit
Installation
• 4 rubber washers, to be fitted between the
fixing screws and the housing back panel
• 1 operation and maintenance guide
• 1 wiring instruction.
• 1 drilling layout.
•
2 sensors
• Each control is designed to be wall-mounted;
please select an appropriate fixing method
depending on the weight.
• Install the device in places where the protection
rating is observed.
• To effect the correct electrical connection and
maintain the protection rating, use appropriate
cable glands and plugs to ensure a good seal.
Mechanical assembly
• Install the device at an appropriate height for
ease of use and maintenance. The installer must
not be put at risk when working on the panel.
The device must be located at a height of between
0.6 and 1.7 m from the ground.
• Install the device away from fire and heat sources
and protect from the weather if necessary.
A label bearing the following information is affixed to
the side of the product described in this manual
• Name of manufacturer
• Product type and code number
• Product name
• Power supply
• Compressor range
• Serial number (10 digits)
• Date (Day/Month/Year)
Identification data
Each control is carefully packaged to ensure that
it arrives undamaged under normal transport
conditions. Prior to transportation, please ensure
that:
• No objects or loose parts are inside the control.
• The door is correctly closed and locked.
• If the original packaging is not used, the
product is sufficiently packaged to allow safe
transportation
Transport and storage
The storage room must be of a suitable temperature
and low humidity; avoid contact between the
electrical control and aggressive contaminants that
could impair functioning and electrical safety.
Example:
Installation to be done by authorised person only!
Summary of Contents for OPTYMA
Page 2: ......