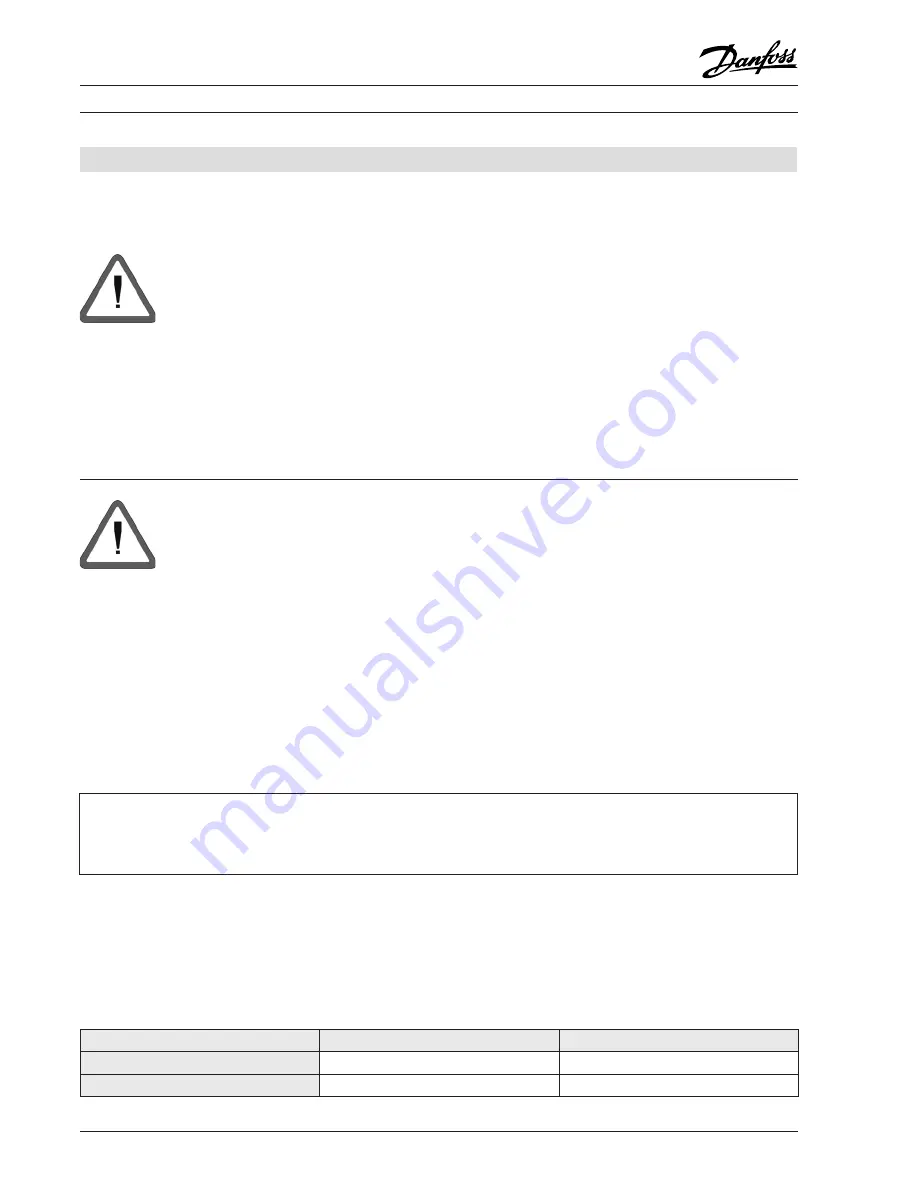
26
RS8FE102, 080R9278
©
Danfoss A/S (RA Marketing/MWA), Nov. 08
OPTYMA
TM
Control three-phase
Operation and Maintenance Guide
General safety instructions
Before carrying out any repairs or maintenance work on the electrical system, please disconnect
the voltage to the control by placing the general power supply switch in the open position
(O). Check the absence of voltage with a voltage detector before performing any operation.
Replace any defective element of the control with original spare parts only.
If the correction is required on the outside of the control, proceed as follows:
- Safely switch off the control power supply in one of the following ways:
1) Turn the OPTYMA
TM
Control main switch to the OFF position and secure the transparent
polycarbonate front cover with a padlock.
2) Cut off the power supply upstream of the permanently, using a padlock (on OFF position).
- Display signs indicating maintenance in progress.
Maintenance must be carried out only by skilled
technicians.
Please observe these safety instructions before proceeding with maintenance operations:
- Ensure that the control is voltage-free.
- Prevent unauthorized personnel accessing the intervention area.
- Display suitable notices to indicate “Device isolated for maintenance”.
- Wear suitable work clothing (overalls, gloves, shoes, headgear).
- Remove any item which could become entangled in any part of the control.
- Ensure that suitable tools for carrying out the maintenance operations are available.
- Ensure that the tools are correctly cleaned and greased.
- Ensure that all technical documentation required to carry out the maintenance work is
present (wiring instructions, tables, drawings, etc….)
- On completion of the maintenance operation, please remove all the residual materials and
carefully clean the inside of the control.
It is imperative that no additional parts are placed inside the control.
The manufacturer declines all responsibility in the event of failure
to observe the points described on this page.
Maintenance
Maintenance is necessary to ensure the correct
functioning of the control at all times and to prevent
faulty components putting people at risk.
Maintenance work must be carried out by skilled
and authorized technicians who observe the general
safety instructions.
Device
Type of operation
Frequency
Terminal block
Wires tightening
After first 20 days of functioning
Terminal block
Wires tightening
Annual
Summary of Contents for OPTYMA
Page 2: ......