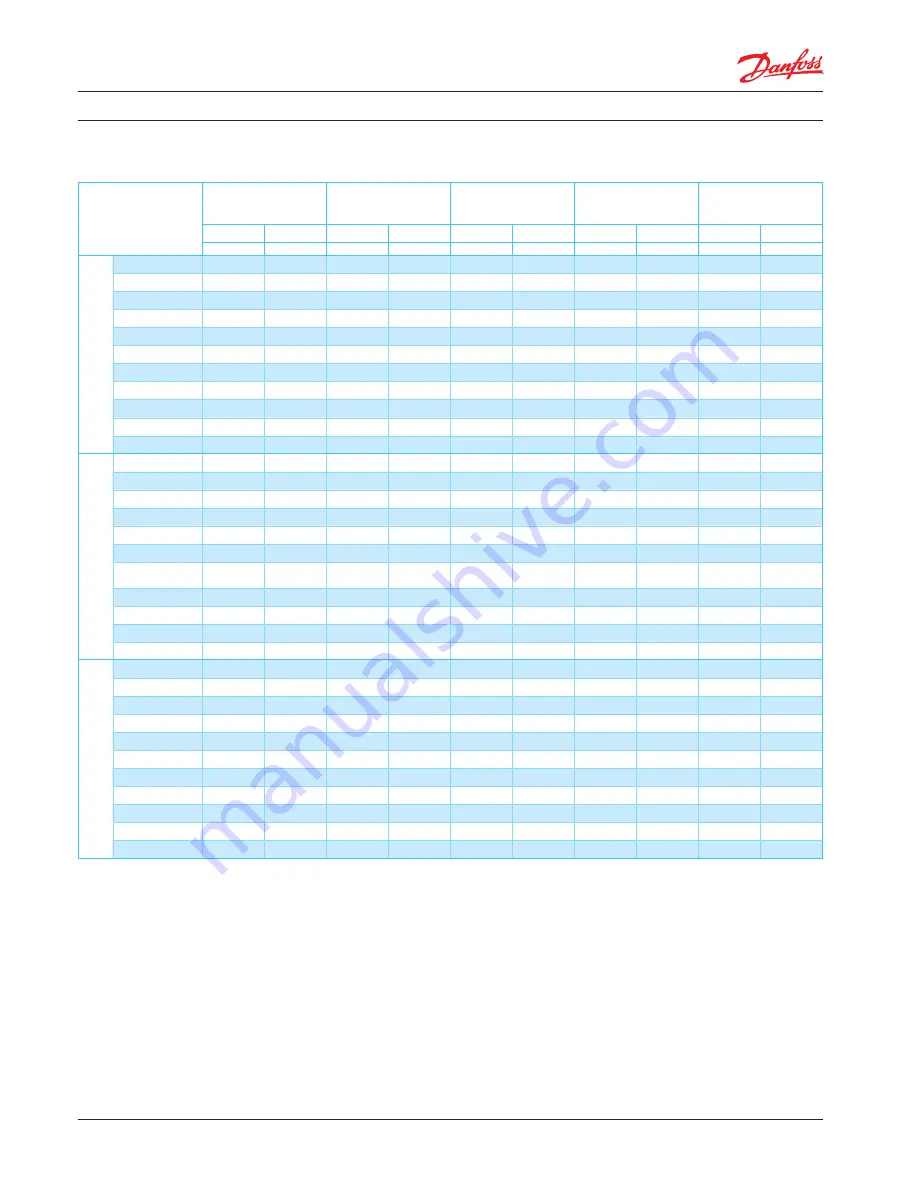
A
PPLICATION
GUIDELINES
T
ECHNICAL
SPECIFICATIONS
50 Hz
Models
SST = 20 °, SDT = 105 °F
RGT = 65 °F, SC = 0 °F
Cold room
SST = 25 °F, SDT = 105 °F
RGT = 65 °F, SC = 0 °F
Ice machine
SST = 32 °F, SDT = 105 °F
RGT = 65 °F, SC = 0 °F
Air drier
SST = 25 °F, SDT = 110 °F
RGT = 65 °F, SC = 0 °F
Milk tank
SST = 20 °F, SDT = 120 °F
RGT = 65 °F, SC = 0 °F
ARI MT conditions
Capacity
EER
Capacity
EER
Capacity
EER
Capacity
EER
Capacity
EER
(Btu/h)
(Btu/h/W)
(Btu/h)
(Btu/h/W)
(Btu/h)
(Btu/h/W)
(Btu/h)
(Btu/hr/W)
(Btu/h)
(Btu/h/W)
R404A *
MLZ015
MLZ019
18 400
9.49
20 300
10.52
23 300
12.12
19 400
9.42
15 800
6.75
MLZ021
19 500
9.51
21 600
10.51
24 700
12.07
20 600
9.42
16 800
6.75
MLZ026
24 400
9.60
27 000
10.63
30 900
12.21
25 800
9.53
21 000
6.82
MLZ030
29 400
9.74
32 500
10.78
37 300
12.37
31 000
9.67
25 200
6.94
MLZ038
35 100
9.71
38 800
10.71
44 400
12.25
37 000
9.61
30 100
6.94
MLZ045
42 200
10.17
46 700
11.23
53 400
12.86
44 500
10.08
36 200
7.24
MLZ048
46 000
10.09
50 800
11.16
58 200
12.82
48 400
10.00
39 400
7.17
MLZ058
54 800
9.76
60 900
10.86
70 200
12.47
57 700
9.69
45 700
6.75
MLZ066
62 800
9.92
69 300
10.90
79 300
12.35
66 200
9.84
54 100
7.17
MLZ076
72 400
9.94
79 900
10.89
91 500
12.35
75 600
9.74
60 300
6.98
R134a
MLZ015
MLZ019
10 900
9.22
12 300
10.32
14 500
12.05
12 000
9.46
9 900
7.07
MLZ021
11 600
9.46
13 100
10.59
15 400
12.35
12 700
9.71
10 500
7.26
MLZ026
14 400
9.61
16 200
10.76
19 100
12.55
15 700
9.85
13 000
7.34
MLZ030
17 300
9.74
19 500
10.91
22 900
12.74
18 900
9.99
15 700
7.45
MLZ038
20 400
9.40
23 000
10.52
27 000
12.25
22 300
9.62
18 400
7.18
MLZ045
25 300
10.19
28 600
11.44
33 700
13.38
27 600
10.44
22 800
7.72
MLZ048
26 800
10.01
30 300
11.20
35 600
13.05
29 300
10.24
24 200
7.59
MLZ058
32 000
9.56
36 000
10.63
42 100
12.27
34 800
9.73
28 800
7.30
MLZ066
37 100
9.75
41 800
10.86
48 900
12.57
40 400
9.94
33 500
7.45
MLZ076
41 400
9.56
46 600
10.65
54 600
12.32
45 100
9.74
37 300
7.30
R22
MLZ/MLM015
MLZ/MLM019
17 300
10.11
19 200
11.20
22 200
12.77
18 600
10.24
15 600
7.71
MLZ/MLM021
18 400
9.91
20 400
10.99
23 500
12.54
19 800
10.06
16 700
7.48
MLZ/MLM026
23 400
10.90
25 900
12.03
29 800
13.70
25 100
10.94
21 300
8.13
MLZ/MLM030
27 500
10.25
30 500
11.49
35 100
13.13
29 600
10.49
24 700
7.74
MLZ/MLM038
32 100
10.15
35 700
11.34
41 200
12.96
34 600
10.36
29 100
7.67
MLZ/MLM045
40 000
10.70
44 200
11.70
50 900
13.38
42 900
10.68
36 400
8.09
MLZ/MLM048
43 200
10.59
48 100
11.67
55 600
13.39
46 800
10.68
39 500
8.04
MLZ/MLM058
50 200
10.54
56 300
11.81
65 700
13.66
54 600
10.77
45 100
7.81
MLZ/MLM066
58 800
10.93
65 700
12.13
76 000
13.85
63 900
11.14
53 900
8.39
MLZ/MLM076
68 000
11.11
75 500
12.23
87 100
13.95
73 400
11.19
61 800
8.32
EER = Energy Efficiency Ratio
All performance data are for motor voltage code 4, 400 V / 3ph / 50 Hz
* R507 performance data are nearly identical to R404A performance data
Capacity data at other conditions are available in the datasheets at: www.danfoss.com/odsg
8
FRCC.PC.016.A1.22