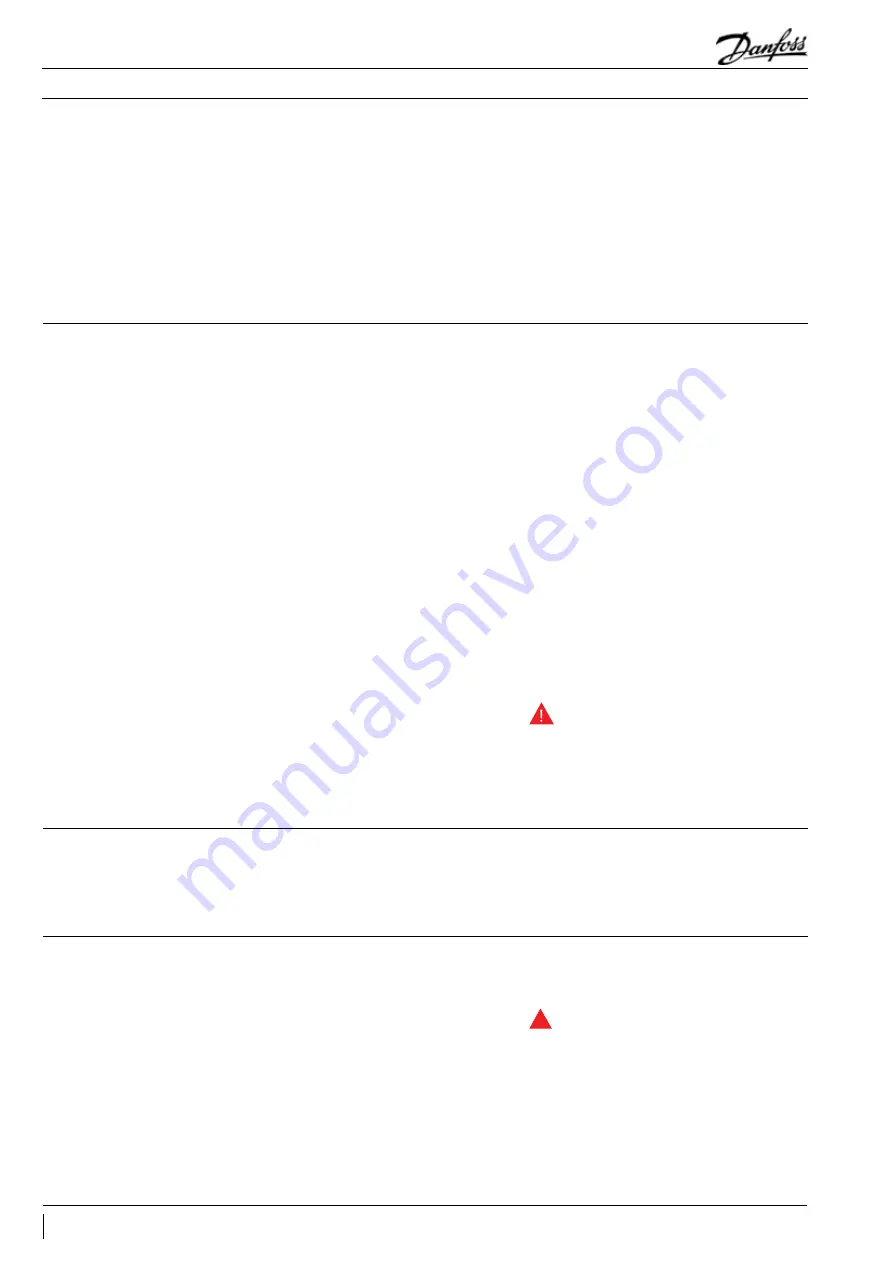
Installation and service
Start-up
Vacuum pump-down and
dehydration procedure
Leak detection
Before initial start-up or after a prolonged shut-
down period, energise the crankcase heater 12
hours prior to start-up. If the crankcase heater
cannot be energised long enough before start-
up, the compressor shall be heated in another
way (for example with an electric heater or
flood light) to boil off refrigerant from the oil.
This is particulary important when ambient
temperature is low at commissioning.
Moisture obstructs proper operation of the
compressor and the rest of the refrigeration
system. Air and moisture reduce service life,
increase condensing pressure and cause
excessively high discharge temperatures,
which are capable of destroying the lubricating
properties of the oil. Air and moisture also
increase the risk of acid formation, thus giving
rise to copper plating. All these phenomena
can ultimately induce mechanical and electrical
compressor failure. To eliminate these risks, it is
recommended to perform the following vacuum
pull-down procedure:
1. To the extent possible (i.e. if valves are
present), the compressor must be kept isolated
from the system.
2. After leak detection, the system must be
pulled-down under a vacuum of 500 microns
(0.67 mbar). A two-stage vacuum pump shall be
used with a capacity appropriate for the system
volume. It is recommended to use connection
lines with a large diameter and to connect these
lines to the service valves and not to the schrader
connection, so as to avoid excessive pressure
losses.
3. Once the vacuum level of 500 microns is
reached, the system must be isolated from the
vacuum pump. Wait 30 minutes during which
time the system pressure should not rise. When
the pressure rapidly increases, the system is
not leak tight. Bring the system pressure up
to atmospheric pressure with dry nitrogen or
another suitable inert gas in order to reform
a new leak detection. After repairing all leaks
the vacuum pull-down procedure should be
restarted from Step 1. When the pressure slowly
increases, this indicates the presence of moisture.
In this case Steps 2 and 3 should be repeated.
4. Connect the compressor to the system by
means of opening the valves. Repeat Steps 2 & 3.
5. Break the vacuum with either nitrogen or the
ultimate refrigerant.
6. Repeat Steps 2 and 3 on the total system.
Upon commissioning, the system moisture
content may be as high as 100 ppm. During
compressor operation, the filter drier must
reduce this content to a level of 20 to 50 ppm.
Do not use a megohmmeter or apply power
to the compressor while it is under vacuum as
this may cause motor winding damage, and
never run the compressor under vacuum as this
may cause the compressor motor to burnout.
Whenever possible the compressor must be kept
isolated from the system during leak detection
by closing the suction and discharge valves. Use
a mixture of nitrogen and the final refrigerant
(eg. R404A or R507A) and use a leak detector
for the applied refrigerant. A spectrometric
detection system using helium can also be
applied. Note that leak detection with refrigerant
may not be allowed in some countries. Do
not use other gasses such as oxygen, dry
air or acetylene as these gasses can form an
inflammable mixture with the compressor oil.
Never use CFC or HCFC refrigerants for leak
detection of HFC systems. Leak detecting
additives shall not be used as they may affect the
lubricant properties. Warranty may be voided if
leak detection additives have been used.
Eventual leaks shall be repaired respecting the
instructions written above.
Refrigerant charging
It is recommended that charging be done to the
high side of the system. Charge refrigerant as
close as possible to the nominal system charge
before starting the compressor. Then slowly
add refrigerant on the low pressure side as far
away as possible from the compressor suction
connection. The refrigerant charge quantity
must be suitable for both winter and summer
operation. All zeotropic mixtures must be
charged in the liquid phase.
R
When a liquid line solenoid valve is used, the
vacuum in the low pressure side must be broken
before applying power to the system.
AB245486497018en-000601
28
Application Guidelines