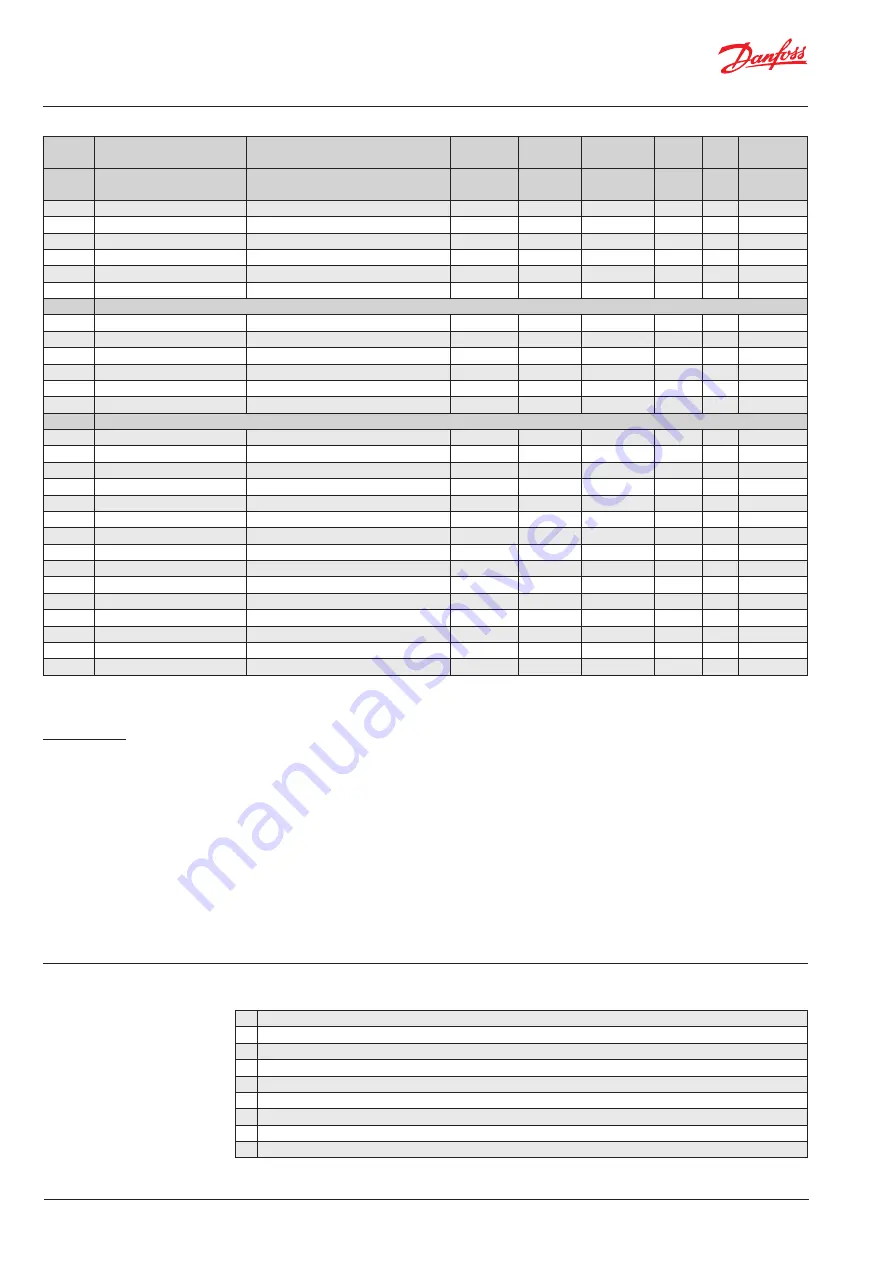
User Guide
|
Intelligent Purging System (IPS 8) for Ammonia - Technical data, installation and use
24 | BC344024774466en-000201
© Danfoss | DCS (ms) |
2021.03
13
14
15
16
17
18
AO
ANALOG OUTPUTS
1
2
3
4
5
6
DO
DIGITAL OUTPUTS
1
Compressor
Compressor relay
0
1
N.O.
Read
18007
2
Valve
Main purge valve relay
0
1
N.O.
Read
18008
3
Green
Status LED
0
1
N.O.
Read
18004
4
Yellow
Status LED
0
1
N.O.
Read
18005
5
DO_Red
Status LED
0
1
N.O.
Read
18006
6
ICFD_Valve
ICFD relay (solenoid valve)
0
1
N.O.
Read
18017
7
Valve1
Purge point valve relay
0
1
N.O.
Read
18009
8
Valve2
Purge point valve relay
0
1
N.O.
Read
18010
9
Valve3
Purge point valve relay
0
1
N.O.
Read
18011
10
Valve4
Purge point valve relay
0
1
N.O.
Read
18012
11
Valve5
Purge point valve relay
0
1
N.O.
Read
18013
12
Valve6
Purge point valve relay
0
1
N.O.
Read
18014
13
Valve7
Purge point valve relay
0
1
N.O.
Read
18015
14
Valve8
Purge point valve relay
0
1
N.O.
Read
18016
15
Alarm
IPS general alarm output
0
1
N.O.
Read
18002
Label ID
Parameter name
Description and selection options
MIN
MAX
VALUE/TYPE
UNIT
RW
Modbus
address
PARAMETERS & STATUS
VARIABLES
Modbus RTU
Good Practice
The wiring of Modbus RTU (RS485) must be carried out in accordance with the standard ANSI/TIA/EIA-485-A-1998.
Galvanic separation shall be provided for segments crossing buildings.
Common ground shall be used for all devices on the same network inclusive router, gateways etc.
All bus connections in the cables are made with twisted pair wires.
The recommended cable type for this is AWG 22/0.32 mm2. If used for longer distances please use a AWG 20/0.5mm2 or AWG 18/0.75mm2
cable. The cables characteristic impedance shall be between 100 – 130Ω The capacitance between conductors shall be less than 100 pf
per meter.
Note: the length of the cables influence the communication speed used. Longer cable lengths mean lower baud rate should be used.
Maximum cable length allowed is 1200m.
Use a minimum 20 cm distance between 110V/230V/400V power line cables and bus cables.
Maintenance/Service/
Disposal
Table 02
Maintenance checklist - Perform once a year minimum
1
Use P&I dagram and check that all powered components are working properly
2
Check for alarms in the MCX controller
3
Fans, air filters and fins must be cleaned for dirt and dust
4
Expansion valve must be inspected and must be replaced if damaged
5
Ensure expansion valves sensor bulb has good contact with suction line
6
Replace water in water bubble bath. Check pH level frequently and replace when pH > 12.6
7
Check cover is mounted correctly and all bolts are tightened accordingly
8
Check and verify the amperage of the unit
9
Check for abnormal compressor noises in normal operating conditions (may indicate loose bolts, worn bearings or pistons)