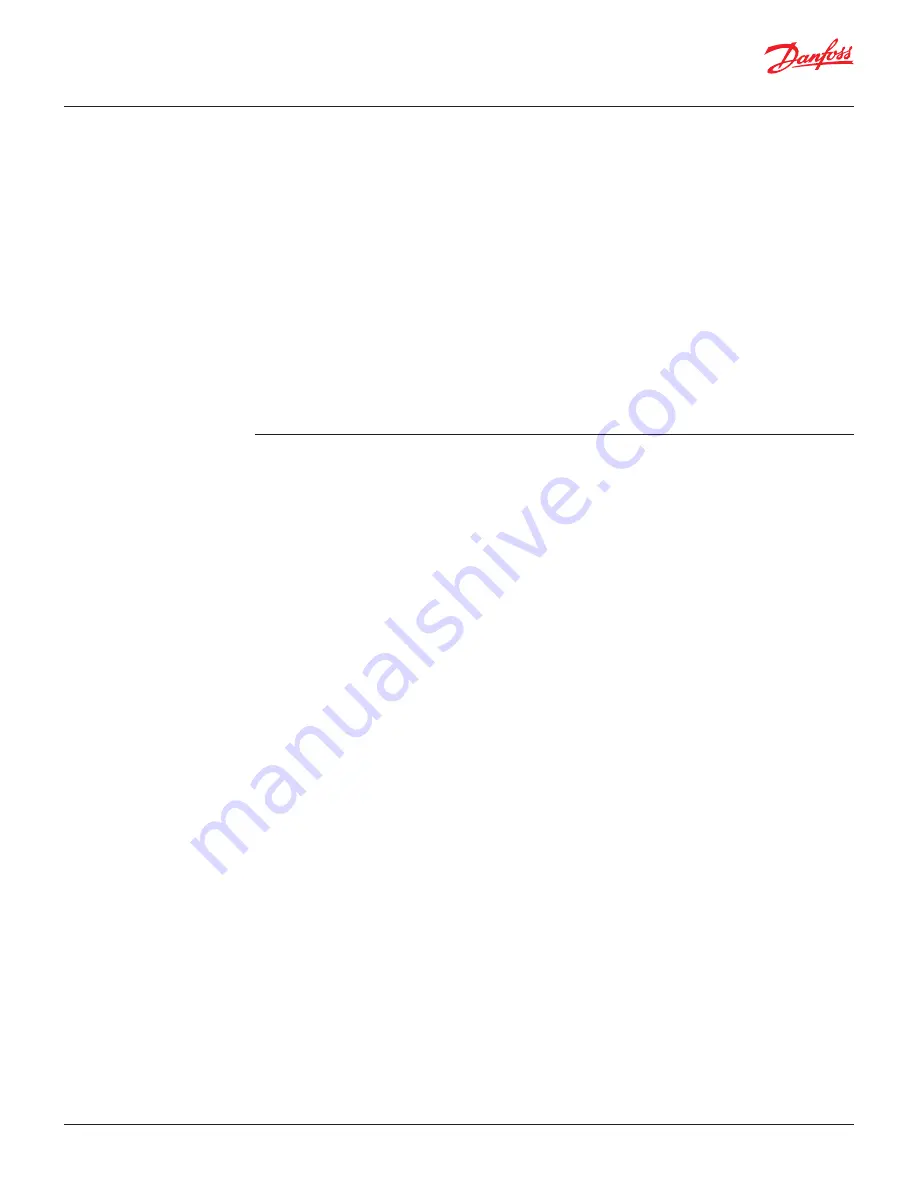
Quick Start Guide | ICM/ICAD Motorized Valves - Installation, Programming, and Troubleshooting
© Danfoss | DCS (MWA) | 2016.07
DKRCI.EI.HT0.B3.22 | 520H4763 | 15
Troubleshooting continued
The alarms and service values work together to allow the user to quickly diagnose the source of operating
issues. The most common alarms are:
A1
The user has not selected the valve type. Each ICAD actuator is capable of driving several
different valve sizes. Upon installation of the valve, it is mandatory that the user select the
valve size from parameter
¡
26.
A3
The control signal is out of the range of the selected values. The most common causes of
this problem are:
1. Improper wiring
2. Incorrect selection of control signal (parameter
¡
03)
3. The source of the control signal is not outputting the correct type of signal.
A9
The valve is locked, disconnect and remove motor. Use magnetic tool to slowly open/close the
valve thru the full range. There should be at no point a sticking/tight spot. You may need to
remove the valve bonnet/module to clean debris or replace the bonnet/module if it is damaged.
If A9 alarm continues please contact Danfoss with application details.
Of course, there are numerous other alarm messages designed to protect the equipment and help to
diagnose problems as pro-actively as possible. Most of these alarms are fairly self-explanatory.
The valve does not appear to close or stay closed completely.
• The display shows 0% opening degree but the valve can be driven further closed with the manual
tool.
Solution:
Recalibrate the valve. In addition, if the manual tool has been used to open or close the
valve, the valve should turn very easily. If there appears to be resistance in opening or closing the
valve, replace the module.
• The display shows 0% opening degree and the valve cannot be driven closed any further with the
manual tool.
Solution:
Pull the function module and check to ensure that there are 2 o-rings on the module for ICM
25 and larger. For size ICM 20, make sure valve seat is installed.
The valve does not appear to be moving to the correct position.
• Check service value
¡
51. This is the mA input from the control system. The degree of opening is
linearly proportional to the mA input. (For example, if 4-20 mA was chosen as the input range and
the service value shows 12mA, the valve should be 50% open.)
Solution:
Check parameter
¡
03 to make sure that the correct scale was selected.
• Compare service value
¡
51 to the value reported to be the output from the control system. If
necessary, measure the actual current into the ICAD.
Solution:
If the two values do not equate, check wiring, paying special attention to wire polarity. If
measured mA does not equate to the stated controllers output, the problem is likely to be in the
control system. If measured mA does not equate to the value seen in
¡
51 and everything is wired
properly, the problem is likely with the ICAD actuator.
• The ICAD was not mounted properly on the valve stem.
Solution:
Check to make sure that the ICAD set screws are evenly torqued around the base of the ICAD.
The valve does not appear to be opening fast enough or seems too fast
• The speed of the ICM valves are preset at the factory:
• For ICM valves 20, 25, and 32, the preset speed is 100%
• For ICM valves 40, 50, 65, 100, 125, and 150, the preset speed is 50%
Solution:
Check parameter
¡
04 to note the actual setting and adjust accordingly
The valve position feedback signal is not working with the customer supplied controller/PLC.
• A power supply was installed in the 4-20mA/0-20 mA feedback loop. The ICAD motor actuator
supplies power for the 4-20mA/0-20 mA feedback loop.
Solution:
Remove any power source that may be supplied to the feedback loop.
• Wiring problem.
Solution:
Check the service value of
¡
53 (the analog output signal) to see what the ICAD is outputting.
If nothing is revealed, check the output wire (blue) with an ammeter to verify the actual output value.
• The feedback output signal was not turned on in parameter
¡
06.
Solution:
Change this parameter to the appropriate signal.
Troubleshooting Tips