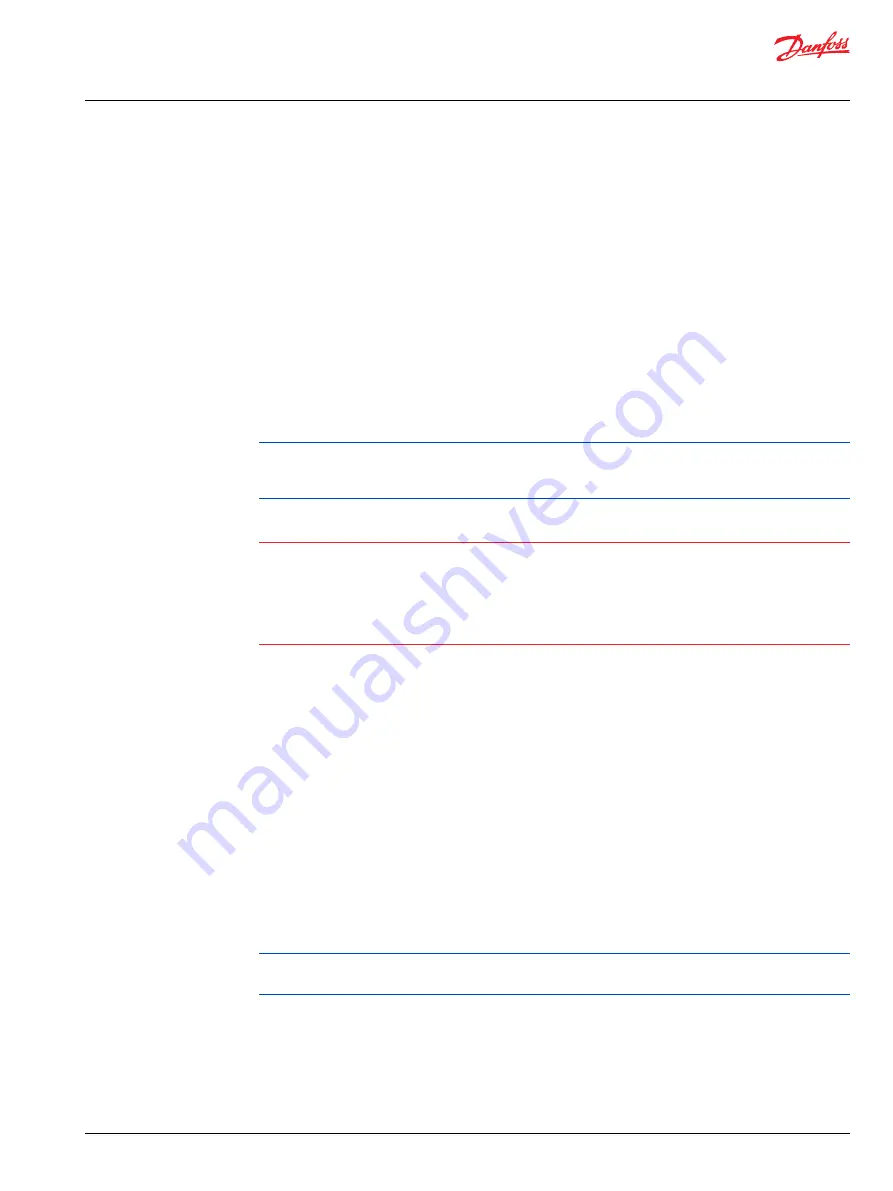
H1F output speed
Start and low speed stability. The motor produces maximum starting torque at maximum
displacement. Stable operation can be achieved at 15–34 rpm, ± 5 %, depending on system pressure, in
applications that require low speed stability. Motor output speed becomes more stable as speed
increases.
Rated speed is the highest output speed recommended at full power condition. Operating at, or below
this speed will yield satisfactory product life. Do not exceed rated speed in open circuit applications.
Maximum speed is the highest operating speed permitted. Exceeding maximum speed reduces the
product life and can cause loss of hydrostatic power and dynamic braking capacity. Never exceed the
maximum speed limit under any operating conditions.
Operation between rated and maximum speed is reserved for intermittent operation (see
on page 11 ) not to exceed 10 minutes durations, 2% of duty cycle based load-life, and 310
bar system delta pressure. Speed above rated are anticipated to occur during downhill braking (negative
power). Contact factory for any operation above Rated speed when negative power is not involved.
During hydraulic braking and downhill conditions, the prime mover must be capable of providing
sufficient braking torque in order to avoid pump over speed. This is especially important to consider for
turbocharged and Tier 4 engines.
W
Warning
Unintended vehicle or machine movement hazard.
Exceeding maximum speed may cause a loss of hydrostatic drive line power and braking capacity. You
must provide a braking system, redundant to the hydrostatic transmission, sufficient to stop and hold the
vehicle or machine in the event of hydrostatic drive power loss. The braking system must also be
sufficient to hold the machine in place when full power is applied.
H1F system pressure
System pressure is the differential pressure between high pressure system ports. It is the dominant
operating variable affecting hydraulic unit life. High system pressure, which results from high load,
reduces expected life. Hydraulic unit life depends on the speed and normal operating, or weighted
average, pressure that can only be determined from a duty cycle analysis.
Application pressure is the high pressure relief or pressure limiter setting normally defined within the
order code of the pump. This is the applied system pressure at which the driveline generates the
maximum calculated pull or torque in the application.
Maximum working pressure is the highest recommended application pressure. Maximum working
pressure is not intended to be a continuous pressure. Propel systems with application pressures at, or
below, this pressure should yield satisfactory unit life given proper component sizing.
Maximum pressure is the highest allowable application pressure under any circumstance. For
applications which are above the maximum working pressure, please contact Danfoss
Minimum pressure must be maintained under all operating conditions to avoid cavitation.
All pressure limits are differential pressures referenced to low loop (charge) pressure. Subtract the low
loop gauge pressure from the high loop gauge pressure readings to compute the differential.
Summing pressure is the sum of both the low and high loop pressures. Summing pressure above 30 bar
[435 psi] guarantees reliable use within the rated speed.
Case pressure
Under normal operating conditions, the rated case pressure must not be exceeded. During cold start,
case pressure must be kept below maximum intermittent case pressure. Size drain plumbing accordingly.
Service Manual
H1F Bent Axis Fixed Displacement Motors, Size 080
Operating parameters
©
Danfoss | December 2023
AX465363259664en-000102 | 17