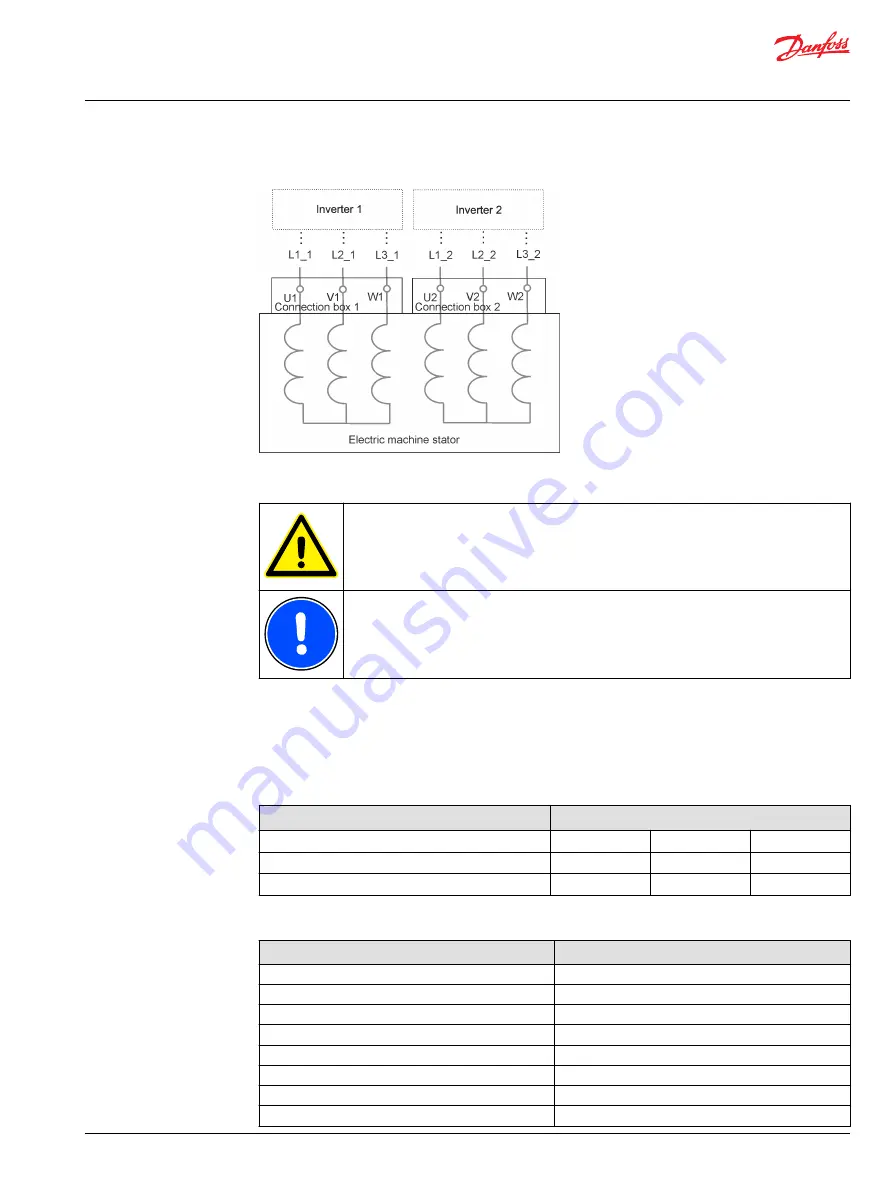
Connection diagram for DUAL option
Cable gland assembly and power line connection
If you are not using the recommended cable lugs, select cable lugs that leave 10 mm gap
between each and every cable lug on the same connection plate.
The pictures are schematic, and the actual components can look different.
This Chapter describes how to assemble screened power cables to the electric machine. See the cable
glands recommendations from the Table below. Cable gland assembly instruction can also be found from
PFLITSCH gland catalog available from
Use correct type of gland for different cable diameters. These are shown in the Table below.
Cable gland alternatives
Cable diameter
Cable gland
35 mm
2
50 mm
2
70 mm
2
Pflitcsh blueglobe mstri225
x
x
x
Pflitcsh blueglobe mstri232
x
x
Blueglobe cable gland tightening torques
Metric thread
Nominal torque
M10x1,0
3,0 Nm
M12x1,5
5,0 Nm
M16x1,5
8,0 Nm
M20x1,5
10,0 Nm
M25x1,5
15,0 Nm
M32x1,5
15,0 Nm
M40x1,5
20,0 Nm
M50x1,5
30,0 Nm
User Guide
EM-PMI540-T1500
Installation
©
Danfoss | July 2021
BC265856800806en-000201 | 41