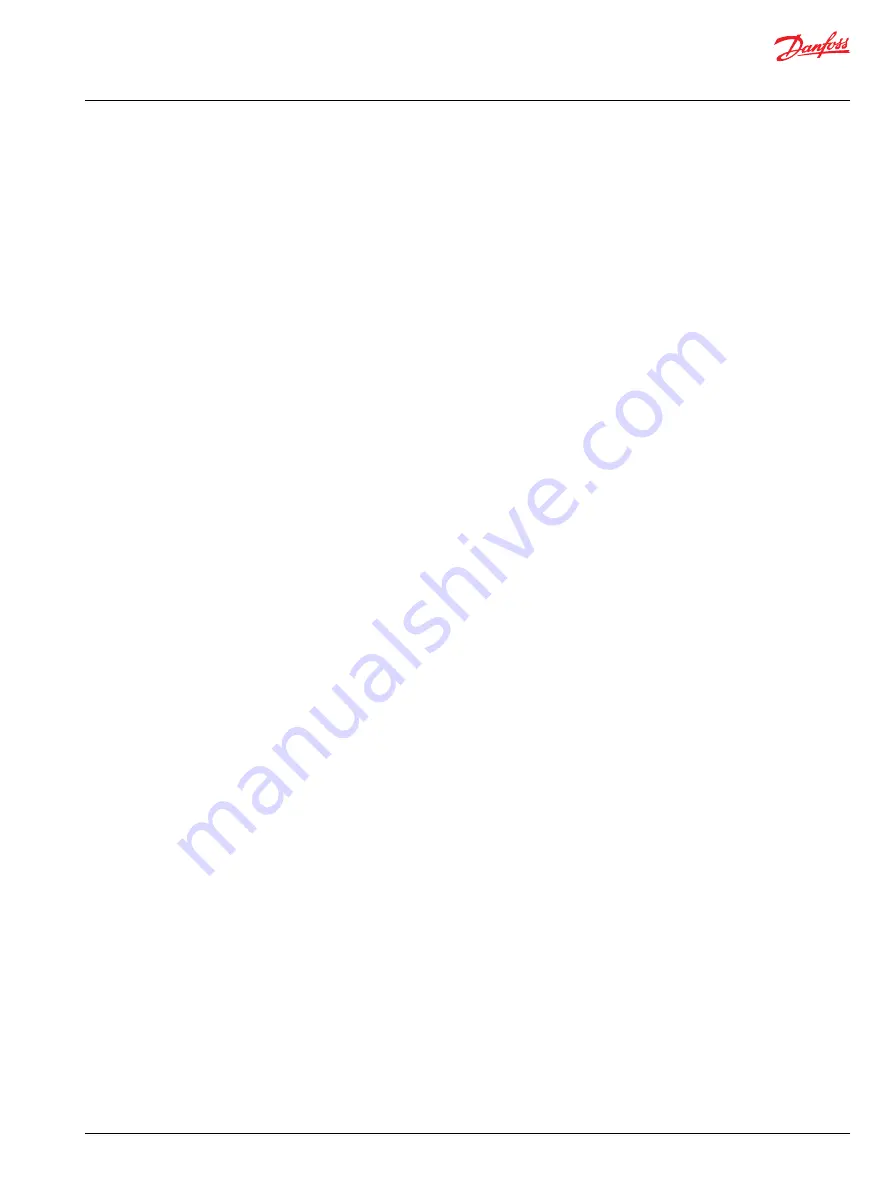
This amplifier is designed to drive Vickers by Danfoss SM4 and SP4 servovalves and most other industry
standard servovalves such as Moog, Atchley, Pegasus, Rexroth, etc. in open and closed loop servo
systems. The package offers flexible circuitry in a standard rack mount format requiring a 24 vdc
supply.
Control Input Stage
The amplifier can accept control signals of either voltage or current. The command signal input at pin B6
and the feedback signal input at pin B8 are voltage type up to ± 10. Control inputs at these pins can
utilize the amplifier's "Ratio" potentiometer which provides for amplitude ratio balancing. The signals
may be inverting or non-inverting via on board switch S1-2 (see switch descriptions). For current loop
inputs, pin Z6 is used to accept the current and pin Z8 is used as a current return. Signal inputs on pin Z6
can be inverting or non-inverting via on board switch S1-1 (see switch descriptions). Input at pin Z6 can
be either a command or a feedback signal of voltage type however, the Ratio potentiometer will have no
influence. All above mentioned control signal inputs can be monitored at front panel test point TP1.
By adjusting the on board potentiometer "Input Bias" a ± 10v signal can be added (summed) to the
control signals, providing input offset when required. The signal present at TP1 is also monitored by the
Tracking Error circuitry. The circuitry performs a comparison of the signal at TP1 to that of a user set
reference point, set by on board potentiometer "Tracking Err." This comparison feature allows the user to
establish a tracking error set point. If the signal at TP1 exceeds the "Tracking Err" set point the front panel
yellow LED will illuminate and the on board "Alarm Output" will energize (opto-coupled transistor turns
on).
P.I.D. Compensation Stage
Signals at test point TP1 are applied to the P.I.D. compensation section of the amplifier. The Proportional,
Integral, and Derivative stages of this amplifier are independently adjustable and switch selectable. On
board switch S1-3 is used to activate the Proportional Gain stage, switches S2-1, S2-2, and S2-3 are used
to activate the Integral Gain stage and switches S2-4, S2-5 and S2-6 are used to activate the Derivative
Gain stage (see switch descriptions for details).
The Proportional Gain can be used to influence system stiffness and possibly accuracy. This stiffness is
typically described as system response.
The Derivative Gain provides a means for system damping. This damping is effective in reducing control
signal overshoot. Damping may be required in systems that require high stiffness or accuracy. Integral
Gain can be used to reduce static error. Static errors are typically those errors that exist but do not
generate enough error signal for load correction. In positioning systems, the Integral Gain is typically not
applied until the actuator approaches position. To facilitate this function an "Integrator Reset Input" is
provided at pin Z24. This pin allows fr external control of the Integral stage.
The summed result of the Proportional, Derivative and Integral stages are present at output pin B18.
(maximum output is ± 10v at 5 ma).
Power Pre-amplifier and Current Limiter Stage
The output of the P.I.D. compensation network (present at pin B18) is also applied to the Power Pre-
amplifier stage. This Pre-amplifier provides yet more adjustable Proportional Gain if desired. This Pre-
amplifier directly feeds the voltage to current driver and its output is ± 6v at 2 ma).
In parallel with this Pre-amplifier are two current limiting circuits. These circuits are used to establish the
maximum positive and negative output currents. This feature allows the user to customize the amplifier
for a particular valve in use, thus protect the valve from currents that exceed its rating. By adjusting on
board potentiometers "+ Current Limit" and "- Current Limit" the amplifier output current can be limited
from 0 to 100% of full scale output.
Current Output Stage
The output of the power pre-amplifier and current limiters is applied to the current output stage. This
stage converts the voltage signal into an appropriate current output. Current is applied to the valve
through pin B26. A current return path from the valve is supplied at pin B28 providing closed loop
temperature compensation.
Installation Guide
Servo Amplifier
Servo Amplifier Discussed
©
Danfoss | August 2023
BC459665217198en-000101 | 5