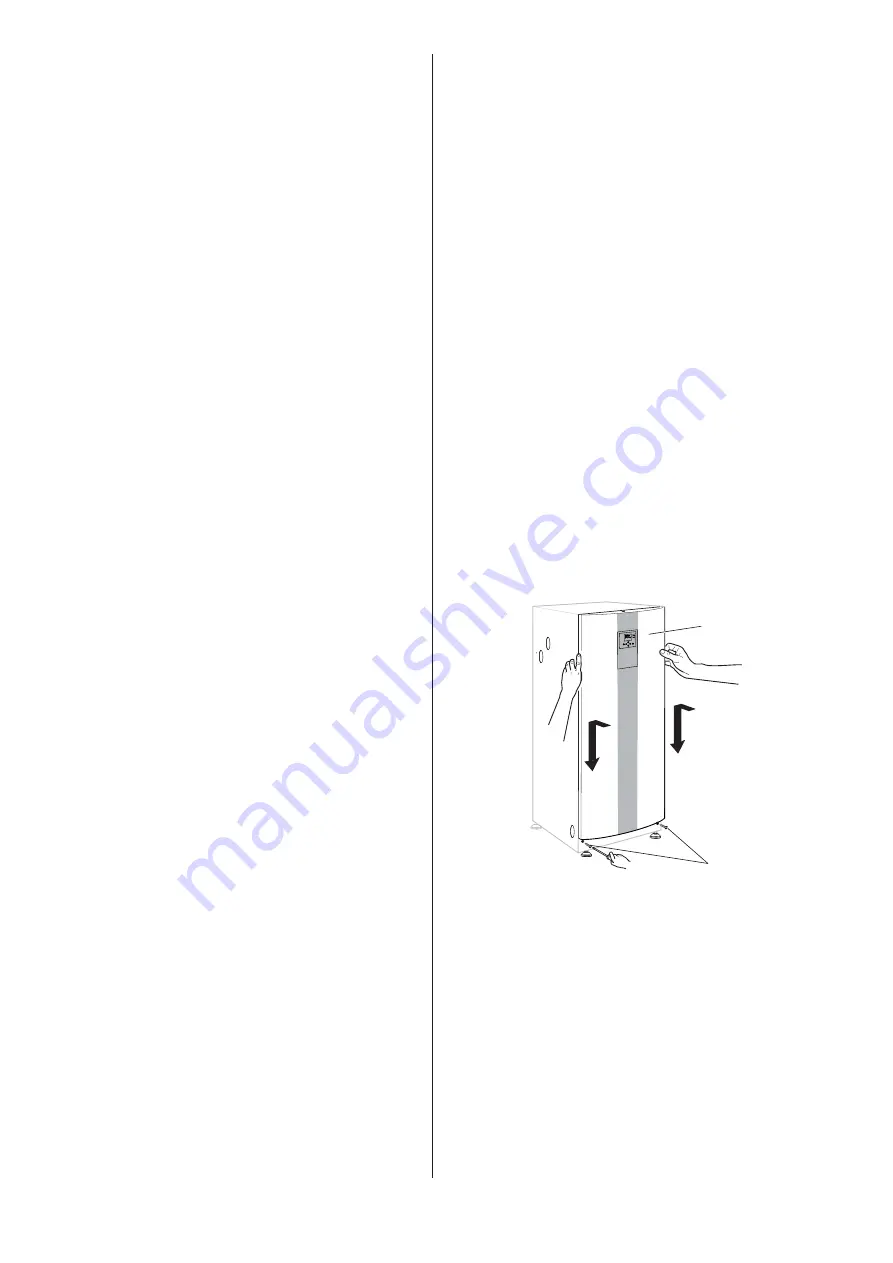
14
VMIFI102
13 Stop both the pumps and immediately close valve 1
and 2.
14 Open valve 3 and disconnect the filling hoses.
15 Open valve 6 and pressurise the system, and vent via
valve 1. Pressurise to max 1.5 bar.
16 Close valve 6.
17 Set switch S1 and S2 to Auto
(compressor and brine pump).
18 Clean the strainers after filling.
8
Start up
⚠
The installation may only start operation if the heat-
ing system, any hot water tanks and the coolant
circuit are filled. Otherwise the pumps can be dam-
aged.
In addition, the following points must be checked before
starting operations:
• Check the rotation direction of the coolant pump. This is
most easily done by setting switch S2 to manual. There
is an indicator lamp, under the cover of the coolant
pump connection terminal box, which lights when the
rotation direction is correct.
• Check that all connections are sealed.
• Check the compressor’s direction of rotation by start
-
ing the compressor and feel by hand if the pressure line
(upper pipe) is warm and the suction line (lower pipe) is
cold.
• If this is not the case, two of the phases in the power
supply must be switched (for example L1 and L3).
• Adapt the factory settings to the customer require
-
ments.
8.1
Installing the front cover
⚠
Take care not to damage the front cover!
Install the front cover as follows:
• Align the upper section of the front cover (2) in both the
side channels on the unit and slide it carefully down-
wards until it covers the entire front side.
• Tighten the screws (1).
1
2
Summary of Contents for DHP-R Eco
Page 1: ...VMIFI102 Installation instructions Danfoss heat pump DHP R Eco...
Page 4: ......
Page 18: ......
Page 19: ......