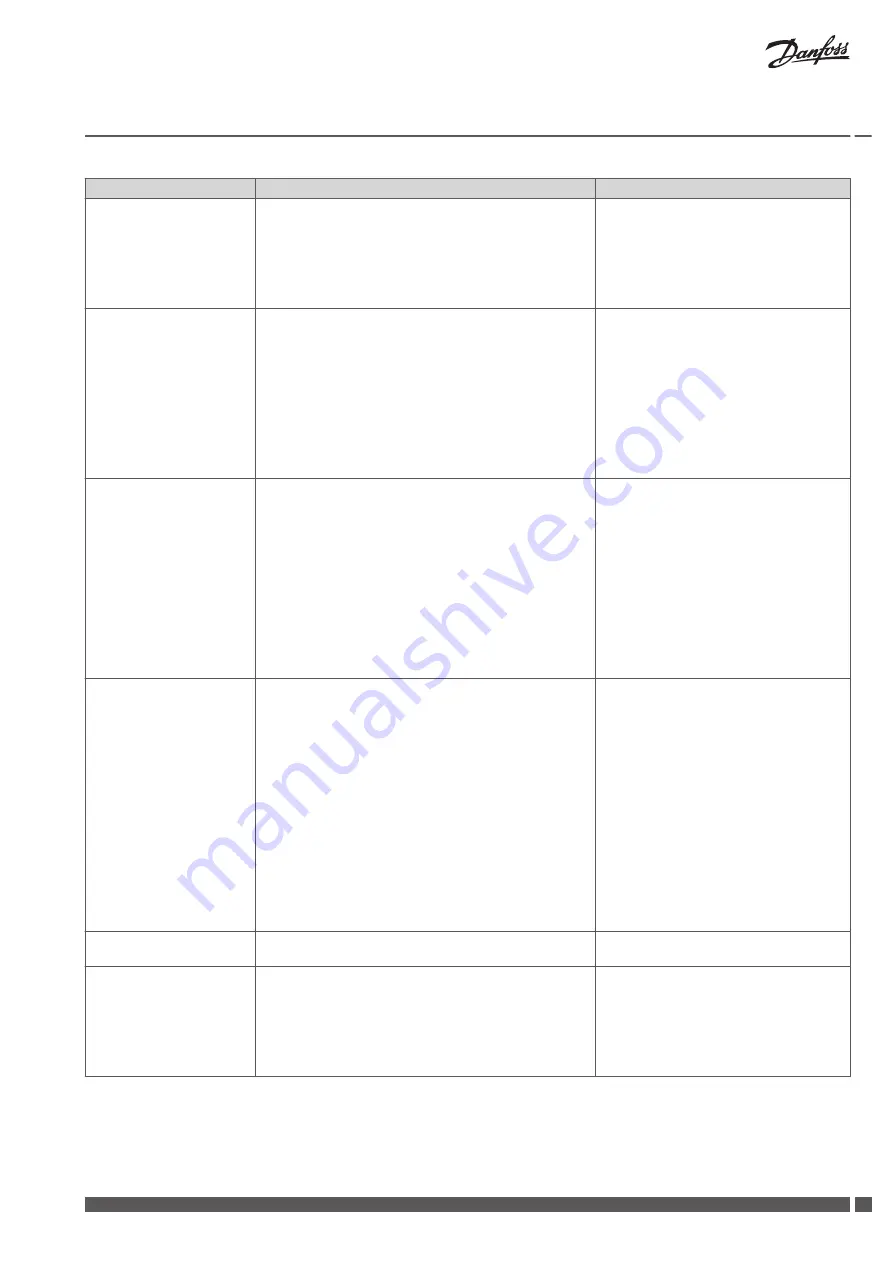
Cause
Troubleshooting
Remedy
5. The interval for peak heat
operation has changed to a
lower value than the factory
set value. This results in the
heat pump going into peak
heat operation more often
than calculated.
Check the specified interval for peak heat operation in the
control computer.
If there is a shorter interval between the
peak heat productions, this explains why
the unit consumes more current than calcu-
lated, but this does not mean for sure that
it should be increased, there might be a
reason why the interval has been changed.
6. The heat pump has stop-
ped on HIGH RETURN.
▪
Check what the MAX RETURN value is set at in the
heat pump’s control computer. It must be adjusted to
the unit’s maximum supply temperature and the sys-
tem’s delta temperature so that it does not cut at too
high a return temperature when the highest supply
temperature is transmitted.
▪
Check what the return line sensor shows. Is it a plausi-
ble/actual value? If not, take a resistance reading from
the sensors and check against the ohm table in Meas-
If the MAX RETURN value is not adjusted for
the system according to the troubleshoot-
ing window, adjust it. If the sensor is defec-
tive, replace it.
7. The compressor runs
backwards. The incoming
phases have the incorrect
sequence (only applies to 3-
phase heat pumps). If the
compressor runs backwards,
it will not cope with com-
pressing the refrigerant and
therefore does not produce
the correct power, which
leads to the control comput-
er requesting auxiliary heat-
ing.
▪
If the text ERR PHASE SEQ. appears in the display
when the heat pump is powered, (only appears in the
first 10 minutes) this means that the phases have the
incorrect sequence.
▪
When the compressor is running, check the pressure
pipe temperature by feeling the pressure pipe. If the
phases are correctly sequenced it should be hot (not
just warm) even a distance from the compressor.
▪
When the compressor runs with the phases incorrect-
ly sequenced a strange noise may be heard (loud, rat-
tling) when the compressor runs backwards.
If the phases are in the incorrect order,
switch two incoming phases at the main
terminal block and recheck according to
the troubleshooting window.
8. The compressor has been
stopped by the operating
pressure switch or delivery
line sensor.
Check if a square appears in the display’s lower left corner.
If so, the operating pressure switch is open or the delivery
pipe sensor triggers an alarm for too high temperature.
▪
The operating pressure switch is most easily checked
by using a buzzer to see if it is connected.
▪
The delivery line sensor value is read off from the con-
trol computer in the HEAT PUMP menu. Is it a plausi-
ble/actual value? If not, take a resistance reading from
the sensor and check against the ohm table in the in-
stallation instructions.
▪
The compressor has been stopped by the delivery line
sensor and you have established that it shows the
correct temperature. This may have been caused by a
leak in the refrigerant circuit.
If the operating pressure switch has stuck in
the open position, try gently tapping on
the pressure switch head. If this does not
help, or it sticks in the open position re-
peatedly, replace the pressure switch. If the
delivery line sensor is defective, replace it. If
the delivery line temperature gets so hot
that the compressor stops, start by leak-
tracing the unit. Rectify the leak, if a leak is
found. If no leak is found, try draining and
refilling the unit and then restarting the
heat pump and seeing what the delivery
line temperature is. If the problem persists,
replace the compressor.
9. Expansion valve defective
or incorrectly set.
Using manometer apparatus and thermometer check what
the overheating reading of the unit is.
If the expansion valve is defective, replace
it.
10. Lack of refrigerant, not
enough refrigerant in the
system.
Using manometer apparatus and thermometer, check that
the unit’s overheating is correct for the specific refrigerant.
If there appears to be a leak in the refriger-
ant circuit, carry out leak tracing and any
necessary corrective action. If leak tracer is
not available, brush soap water on the sus-
pected leak and look for bubbles. Also
check for oil as this can come out from the
refrigerant circuit.
Service Instructions
DHP-AQ
Danfoss Heating Solutions
VMGFJ202
31