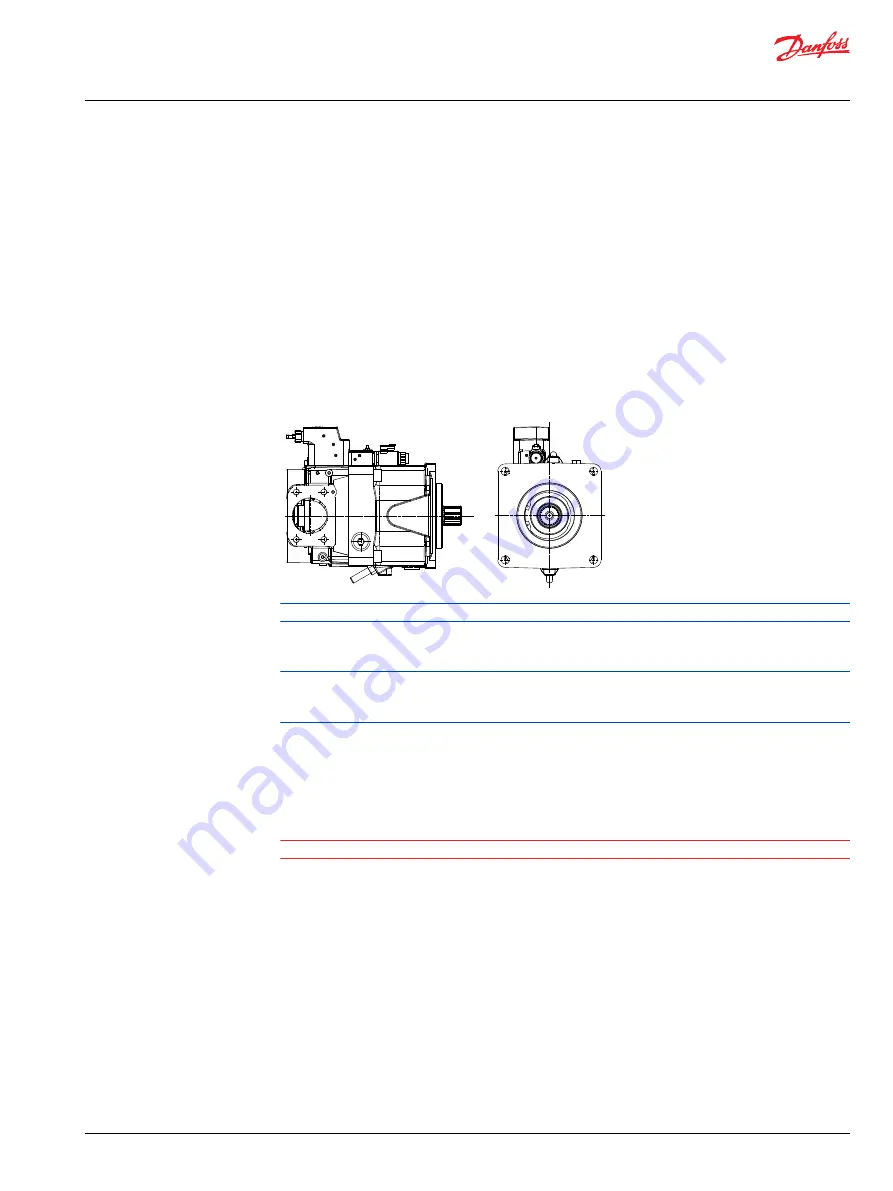
Operation
The purpose of this section is to indicate the necessary procedures to perform the pump start up.
Pre-start up controls for D1P pump
Before performing the first pump start up, the following points have to be checked.
Hydraulic components must be installed in accordance with their individual instruction.
1. To avoid contamination, plastic plugs in connection ports must not be removed until just before
connections are made.
2. Make sure the pump hydraulic connections allow the pump to rotate in the desired direction. For
pumps with standard direction of rotation:
Clockwise rotation (viewed facing the output shaft) with inlet pressure in the front port.
Counter-clockwise rotation (viewed facing the output shaft) with inlet pressure in the rear port.
Generic illustration shown.
3. Select the hydraulic fluid as specified in
4. Ensure full contact between pump mounting flange and connecting part.
Avoid pressing the pump into place by tightening the fixing bolts. Avoid unsuitable seal materials, for
example, twine and Teflon, on threaded unions. Use only the seals supplied, such as O-rings, steel
washers.
5. Make sure that all couplings are completely tightened to prevent leakage.
Do not use more torque than the maximum values given in the instructions.
6. Check to make sure the purity of the oil is greater than 22/20/16 (ISO 4406-1999) and always use a
filter when replenishing the system.
W
Warning
The pump must be filled with fluid prior to any load applications.
User Manual
ATEX certified D1P 130/145/193/260
Installation, operation and maintenance
©
Danfoss | August 2021
BC376161003883en-000101 | 11