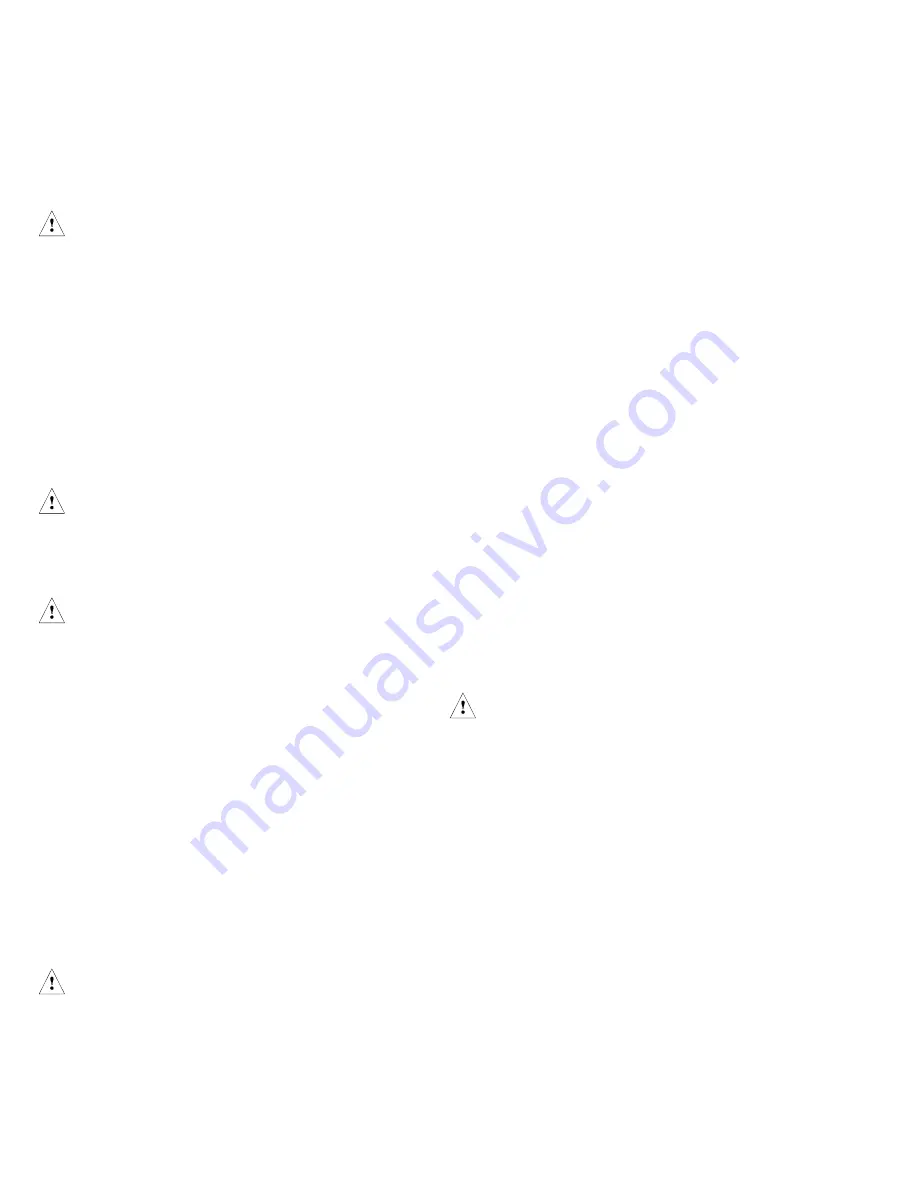
Airflex
®
DBB 8110 Brake Assembly
E-CLCL-TT001-E December 2012
10
3.2.1.3 Release the brake by applying full release pressure
through the ports in the cylinder (19) to allow the
brake to freely rotate.
Caution
Maximum applied pressure is 120 psig (8.2 bar) for
sizes 20DBBS, 25DBBS and 38DBBS. Maximum
allowable air pressure is 150 psig (10.3 bar) for
the 50DBBS. Minimum releasing pressure for low
pressure brakes is 60 psig (4.1 bar).
3.2.1.4 Run the motor to achieve a brake disc speed listed in
Table 6. Rapidly exhaust the air pressure in the brake
to the pressure listed in Table 6. Slip the brake for
the time specified in Table 6, but DO NOT ALLOW
THE BRAKE TO SLIP FOR MORE THAN THE TIME
SPECIFIED.
Caution
Slipping the brake at increased time intervals,
speeds, pressure or temperatures other than
specified may result in damage to brake components.
Caution
Brake pressures listed in Table 6 are for the standard
compliment of power springs in the DBBS brake.
The standard quantity is listed in Table 6. If a brake
contains less than the standard compliment of
springs, consult Danfoss/Airflex engineering for proper
brake pressure to wear-in the brake and spring
quantity if unknown for the specific brake.
3.2.1.5 After the brake has engaged/slipped for up to the
maximum slip time specified in Table 6, quickly apply
full air pressure to completely release the brake.
Smoke rising from the brake should be expected.
Freewheel the brake discs at speeds up to the
maximum freewheeling speed in Table 6 to allow
the brake discs to cool to a temperature at or below
120°F (49°C) use of fans or clean, dry compressed air
can be used to accelerate the cooling process.
Caution
Use proper safety precautions when using forced
ventilation.
Note
The brake pressure listed in Table 6 should provide
a dynamic torque target value as listed and resultant
power target at the brake speed listed. Since new
friction torque will be lower at the start of wear-in
procedure, pressure may need to be lowered to
achieve the target torque. An adequate control and
torque monitoring system must be used if pressure
values less than those listed are used for wear-in.
Target torque should be monitored to correspond to
values listed.
3.2.1.6 Monitor the brake discs temperature during
slipping and cooling. Do not allow the brake discs
temperature to exceed 250°F (121°C).
3.2.1. 7 Repeat steps 3.2.1.3 through 3.2.1.6 for the number
of cycles shown in Table 6 to allow for adequate
wear-in of the brake. Allow the brake disc to
completely cool to ambient temperature prior to
testing the torque capacity of the brake or returning it
to service.
3.2.2
If the brake engagement appears harsh, a flow
control valve may be installed in the brake air supply
line. When using a flow control valve, install so free
flow is to the brake and restricted flow is away from
the brake.
Caution
Excessive restriction of the brake exhaust air will
result in long stopping times and inconsistent
stopping position. Consult Danfoss Airflex Engineering
with questions.
3.2.3
If the DBBS brake is used in combination with a
clutch, clutch/brake overlap may occur which will
result in excessive heat generation and motor
overload. Overlap may be detected by monitoring the
drive motor current at the beginning and end of each
machine cycle. A current surge at the beginning
of the cycle usually indicates clutch overlap which
can be corrected by restricting the air flow to the
clutch or increasing the air pressure to the brake. A
current surge at the end of the machine cycle usually
indicates brake overlap (see Figure 3) which can be
corrected by installing and adjusting a flow control
valve in the brake air supply line, as indicated in 3.2.2.
DBBS Brakes
Summary of Contents for Airflex DBBS
Page 26: ......