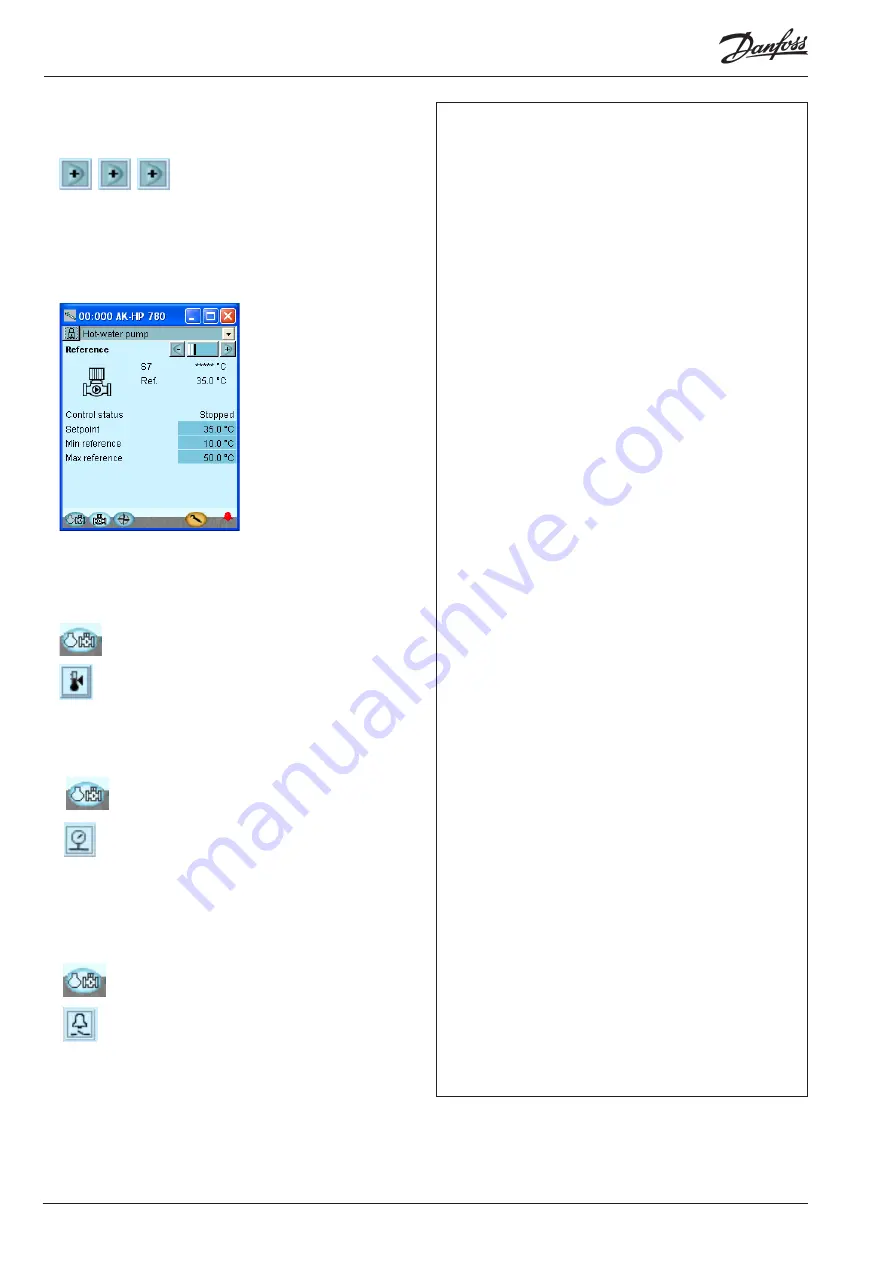
70
Heat pump controller RS8GF202 © Danfoss 2015-08
AK-HP 780
7. Move on through all the individual displays for the
pump.
Change displays with the +- button. Remember the settings at
the bottom of the pages – the ones that can only be seen via
the ”Scroll bar”.
8. Safety limits
9. Go back to the overview and Move on to the ther-
mostat group
Check the settings.
10. Go back to the overview and Move on to the press-
sostat group
Check the settings.
11. Go back to the overview and on to the general
alarm inputs
Check the settings.
12. The controller setup has been completed.
Check of settings - continued
The last page contains reference settings