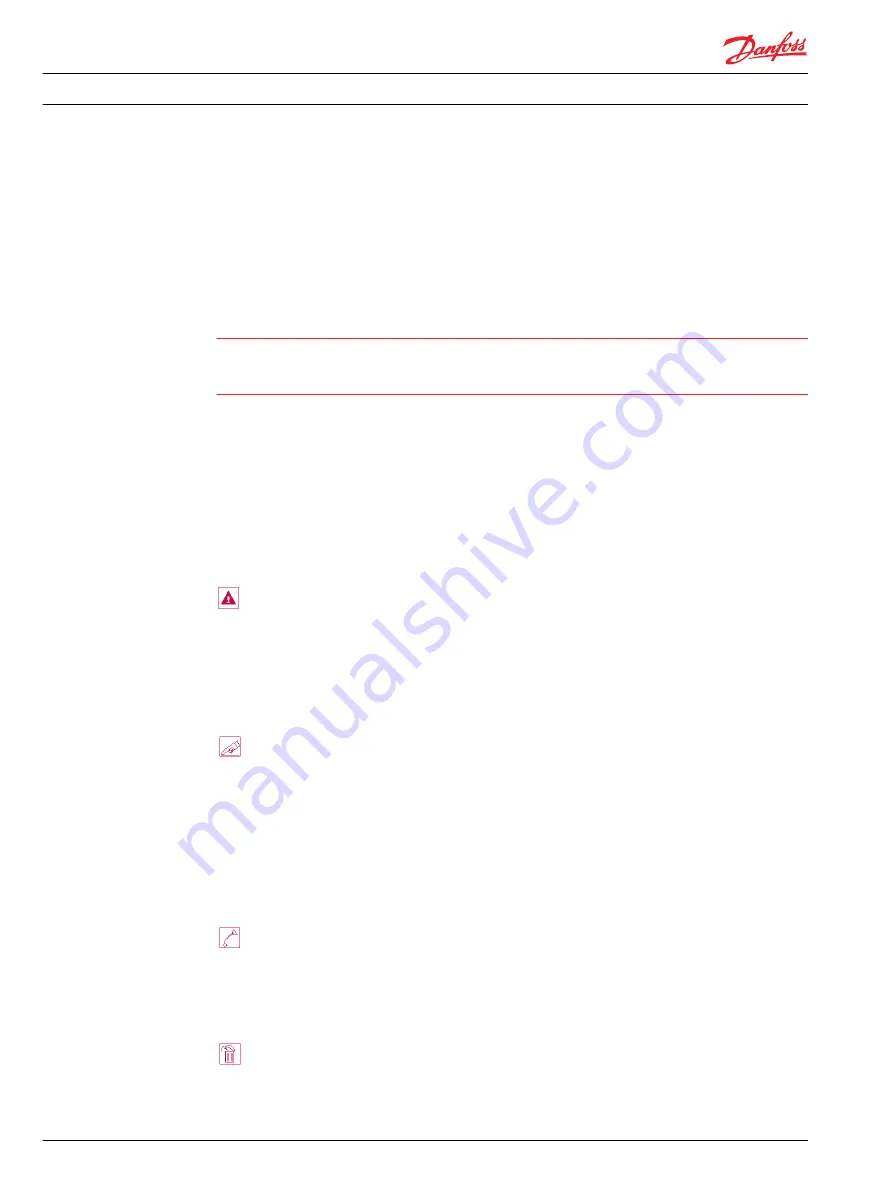
Overview
This manual details repair procedures for Series 51 bent axis motors. These include the complete
disassembly, inspection, and reassembly of the unit. Where rework of worn or damaged components is
possible, specifications are given to ensure these parts meet factory tolerances. Only Danfoss Global
Service Partners may perform major repairs. Danfoss trains Global Service Partners to perform major
repairs and certifies their facilities on a regular basis.
W
Warning
Use of components that do not comply with rework specifications may result in loss of performance,
which may constitute a safety hazard. Do not reuse components that don't comply to given
specifications: replace with genuine Danfoss service parts.
Minor repair procedures, adjustments, and troubleshooting information are given in the Series 51 and
51-1 Service Manual, 11008567. Minor repairs include service operations you can perform without
removing the unit's endcap. Removal of the endcap voids your warranty.
General instructions
Follow these general procedures when repairing Series 51 bent axis variable displacement closed circuit
motors.
Remove the unit
Prior to performing major repairs, remove the unit from the vehicle/machine. Chock the wheels on the
vehicle or lock the mechanism to inhibit movement. Be aware that hydraulic fluid may be under high
pressure and/or hot. Inspect the outside of the pump and fittings for damage. Cap hoses after removal to
prevent contamination.
Keep it clean
Cleanliness is a primary means of assuring satisfactory pump life on either new or repaired units. Clean
the outside of the pump thoroughly before disassembly. Take care to avoid contamination of the system
ports. Cleaning parts with a clean solvent wash and air drying is usually adequate.
As with any precision equipment, you must keep all parts free of foreign materials and chemicals. Protect
all exposed sealing surfaces and open cavities from damage and foreign material. If left unattended,
cover the pump with a protective layer of plastic.
Lubricate moving parts
During assembly, coat all moving parts with clean hydraulic oil. This assures that these parts are
lubricated during start-up.
Replace all O-rings and gaskets
Danfoss recommends you replace all O-rings, gaskets, and seals. Lubricate O-rings with clean petroleum
jelly prior to assembly. Grease must be soluble in hydraulic fluid.
Repair Instructions
Series 51 and 51-1 Bent Axis Motors Repair Instructions
Introduction
4
11009449 • Rev BA • December 2014